Circuit board shopping
2017-09-10 PCBs electronics design
This week I'm planning to order the prototype boards for the Leapfrog Filter, and it makes a good opportunity to go through some common questions beginners ask about shopping for PCBs. When you go to buy PCB production services you're typically hit with a form asking you to select which features you want, and it's not always clear what the consequences of the different answers may be. In this entry I go through some of those options, and give some other notes on shopping for PCBs.
First of all, note that PCBs in this context are Printed Circuit Boards, the (nowadays usually fibreglass laminated with metal and plastic) boards on which components are mounted in electronic equipment. Don't confuse circuit boards with Polychlorinated Biphenyls, the other kind of PCBs - those are a category of highly toxic oily substances which historically were also used in electronics and electrical systems, mostly for insulation in capacitors and cooling in power transformers. The oil kind of PCBs are especially nasty because in addition to being toxic, they don't break down easily, so once they contaminate a site it can be very difficult to clean it up. Back in The Day, you could actually buy PCB-insulated capacitors at Radio Shack ("Dykanol A" capacitors, page 96 in the linked catalog from 1957), and you may still find them in some old equipment. I've even seen them pulled from old equipment and listed on eBay for use as replacements, which is almost certainly illegal - if you're unlucky enough to come into possession of one today, you're obligated to dispose of it as hazardous waste, not sell it to the unwary.
When it comes to the kind of PCBs that are circuit boards, the thing is that in general they have to be custom-made for any given project, so you're looking at hiring a factory somewhere (often, China; and often the city of Shenzhen in particular) to make your boards for you, usually in small quantities. Some hobbyists still etch their own PCBs at home, but I think that's not advisable. The industry has progressed to the point that there's just no way for a home hobbyist to match the quality and features of a board made by a commercial small-batch manufacturer. People who claim they save money and time by doing it themselves are both putting zero value on their own labour and failing to compare identical-quality products. You may be able to make a single-sided board with no silkscreen, no solder mask, and no plating, in your bathtub (and then dispose of the waste improperly) for less than it costs to order a two-sided board from China with silkscreen, solder mask, HASL surface treatment, plated through holes, and at least a promise (which may or may not be accurate) that they're following the environmental regulations... but that's hardly a fair comparison. And then there are the safety questions, but I will reserve most of my rant about peroxide-boosted acids for another day. About the only remaining advantage to home production of PCBs is that it's possible to do just one at a time, whereas very few commercial manufacturers will handle batches smaller than three or five identical boards.
On choosing a manufacturer: you want one who will give you acceptable quality, and can do whichever features you're looking for including stuff like turnaround time that goes beyond the physical features of the boards themselves; and most people take price as an important consideration, too. I usually deal with either OSH Park (based in Oregon, USA) or Elecrow, in Shenzhen. There's a useful comparison site called PCB Shopper where you can put in your requirements and get a comparison across many different manufacturers; there are some relevant details not captured by this automated comparison, though, so you still need to go look carefully at the individual manufacturers' Web sites.
UPDATE: As of April 2020, I no longer use or recommend OSH Park. They made a faulty batch of prototype boards for me, with some holes too small for the corresponding components to fit into, in a time-critical situation. The boards were worse than useless. Since the affected components happened to be late in the build, I wasted a couple days' work and a bunch of components building most of the project before I discovered that I couldn't go on and had to scrap the whole thing. OSH Park's customer service did not seem interested in working with me to resolve the problem quickly, instead starting an argument over who was at fault. They claimed that I had specified the holes too small in the first place - against evidence that the holes were smaller than I had specified by more than the applicable tolerance, and I had used the same specification on hundreds of other boards before, including boards made by OSH Park and by other manufacturers, without any problems.
They refunded my payment after I presented more solid evidence that the holes really were significantly smaller than specified, but that didn't undo the problems that had already been caused by the wasted time.
Surface finish is one important feature to consider. Probably the most popular one, and the cheapest, is called Hot Air Solder Levelling (HASL). That's where they dip the board in liquid solder, and as it's coming up from the dip, they pass it through a flat jet of hot air that blows away the excess, leaving a relatively thick plating of solder on the board. This can be done with lead-based or lead-free solder. Many manufacturers will offer a choice, though more and more are going lead-free only. They may or may not charge extra for the lead-free version if they offer both, but if you want to sell products in Europe, you pretty much have to stick to lead-free. Ideally, you should use whichever form matches the solder you plan to use. Putting lead-free solder on a lead-based HASL board, or vice versa, entails mixing the alloys and ending up with something of unknown composition that may not work as well as either alloy alone. In practice this is seldom a big problem.
HASL is probably the easiest finishing option to work with when you're doing through-hole: one of the biggest issues people have while assembling boards is getting the solder to stick to the copper, and with HASL, it's already there. You only have to deal with getting solder to stick to itself. However, this surface finish isn't the best for shelf life because there's some possibility of the surface oxidizing. It also isn't perfectly flat. The hot air blast leaves a wavy surface that can interfere with properly seating surface-mount components, especially the smallest ones and when you're doing it automatically with robots.
The next level up in surface finish is what they call ENIG: "Electroless Nickel, Immersion Gold." That puts a thin layer of nickel (without using electroplating, thus "electroless") on top of the copper, and then a very thin layer of gold on top of the nickel. The overall result is very flat, which is nice for surface-mount work, and it doesn't tarnish. It also looks nice and has the cachet of involving a precious metal, so you see it on premium boards (like those I sell in my kits). Solder wets this surface quite well, though maybe not as easily as it would with a HASL finish; on ENIG boards it's not usually appropriate to expect solder to wick through and form a visible fillet on both sides, the way people aim for when soldering HASL through-hole boards. Most PCB manufacturers offer ENIG, but they may charge extra for it.
One may well ask, if we want a gold surface, why not just plate the gold directly onto the copper - what's the nickel good for? There are two sides to the answer. First, this gold surface is thin. It's good for anti-corrosion, but it dissolves right out from under the solder when the solder is applied. It's really the nickel layer that you are soldering onto and the gold protects it; but a plain nickel plating wouldn't be good because it oxidizes. On the other hand, to the extent the gold is the main plating, you can't just plate gold onto copper, at least not with the "immersion" process used here. The two metals are too similar, and they tend to mix together. Instead of getting a thin and stable layer of gold on top of the copper, the gold would soak into the copper and you'd end up with solid copper alloyed with a trace amount of gold. Nickel does not mix well with gold or copper (something like an oil-and-water effect, though I think it really comes from their having different crystal structures) and so the nickel forms a barrier over the copper surface, preventing the gold from diffusing deeper.
It's possible to go further with surface coatings, but you won't see many others in hobbyist work, and the less-popular options may not be easy to find from small-batch manufacturers. There have sometimes been problems with the nickel layer in ENIG reacting with impurities in the different plating baths and forming a defective surface. A fancier option called ENEPIG (Electroless Nickel, Electroless Palladium, Immersion Gold) adds yet another layer, of palladium, in between the nickel and the gold to help prevent that. Much heavier gold plating (called "hard gold" or "soft gold" depending on the details of the alloy, methods used, and intended application) is used for things like the contact fingers on video game cartridges and PC expansion boards, where the board plugs into a slot and might be subjected to repeated friction. The thicker gold options cost a fair bit of money per unit area, so they are usually applied only to the edge connectors while the rest of the board gets some cheaper treatment.
Silver, instead of gold, is sometimes used as a whole-board coating for RF circuits that need the lowest resistance on the surface because of the skin effect at very high frequencies; but it tarnishes, and great care must be taken to protect such boards. There's an option called OSP (Organic Solderability Preservative) which is often billed as environmentally friendly because applying it generates less waste than a metal plating: it's bare copper with no other metal plated on, just a coating of water-soluble chemicals intended to prevent corrosion for a time. The main disadvantage is that it has a short shelf life. The boards need to be assembled relatively soon after manufacture or the OSP will not prevent the copper from oxidizing to the point of interfering with solderability. And that brings us to the final option of not putting any coating on the copper but just taking it straight out of the etching bath, rinsing it off, and trying to solder it immediately. That's what people who make their own boards usually do, but you won't see it in professional boards.
People sometimes ask how thick the copper should be - given that manufacturers offer different options, usually at different prices, with no guidance on what's good. Copper thickness on PCBs is traditionally measured in "ounces," never mind that that is the wrong dimension and part of a deprecated system of measurements. One "ounce" of copper is equal to the thickness of copper that you would get if you spread one ounce (the ordinary ounce Avoirdupois of 28 grams, despite that copper might be considered a precious metal suitable for measurement in ounces Troy) of copper over one square foot of circuit board. This works out to one ounce being about 35 microns of thickness. And "one ounce" copper is the usual default, at least for boards meant to be assembled by humans. This refers to the finished thickness of the copper; quite often it's actually made up by etching a thinner copper foil and then plating more copper onto it (prior to the other plating steps described above) to build the desired thickness, partly so as to include the copper plating on the inside of plated-through holes and partly because doing it that way allows for more precise control during the etching process.
You'll sometimes see exceptions to the one-ounce default; for instance, a common deal for four-layer boards is that you get one ounce on the outer two layers and half an ounce on the inner layers. My opinion is that in general, thicker copper is better (because then you get less resistance), but it's not appropriate to pay extra for extra copper beyond the default unless you know you need it - as might be the case, for instance, with a board carrying heavy current, like a bus board. If in doubt, you have to do a proper calculation of how much current you have, how wide your traces are, how much resistance and heating you're willing to tolerate, and so on. Most people design their boards with the traces too narrow anyway, and it's easier and cheaper to fix that than to ask for a thicker copper layer.
I'll close for now by mentioning "blind" and "buried" vias - which you will mostly hear about in manufacturers' lists of specifications for what they do not offer. It's not easy to find a manufacturer who really will do blind and buried vias, and if you must have those things, you will certainly pay extra for it. A via is a connection between two or more layers in a multi-layer board. Typically you've got a hole (with through-plating coating its inside) going right through the board through however many layers, and then the layers that are supposed to connect to it will have pads that connect to the plating, and the ones that are not supposed to connect, will have cut-away sections in their copper so as not to touch the via. And the usual kind of via is a "through" via that goes all the way through every layer of the board, whether they electrically connect to it or not.
In principle, you could have a via where the hole does not go all the way through, but starts on one side, goes down to some internal layer, and then stops. That's a "blind" via. The next step would be one that does not pierce either surface of the fully-assembled board; instead it starts on some internal layer, goes down to some other internal layer, but is fully covered over at both ends. That's a "buried" via. These are only meaningfully defined for boards with more than two layers in the first place, and they are difficult and expensive to manufacture, but in the very highest-density multi-layer boards, people sometimes want to have them so as to be able to pack together as many connections into a small space as possible, or for various special purposes that may require not having a hole go all the way through the board. As I say, at the hobby level you will mostly only hear about them in manufacturers' refusals; but it's worth at least knowing what the terms mean, so you can amaze your friends at parties.
◀ PREV Video picks || Fun with fractal chord progressions NEXT ▶
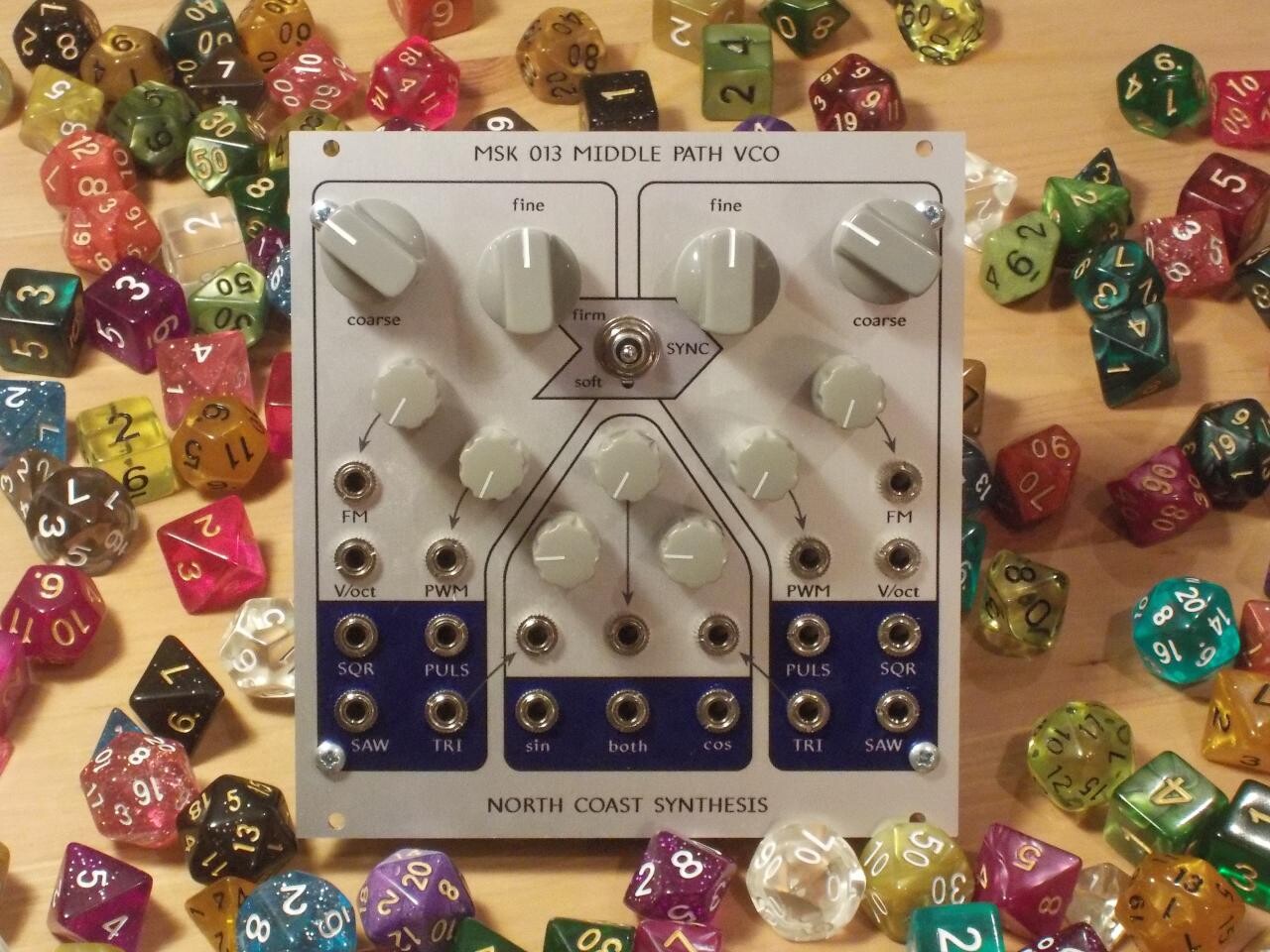