Tools for getting started with SDIY
2018-06-26 electronics SDIY intro
Visit the North Coast Synthesis SDIY page!
It's a fairly common question "What tools do I need to get started with synthesizer do-it-yourself building?" and most people who ask or answer this question seem to think it starts and ends with a soldering iron. That tunnel vision then becomes part of the unrealistic expectation that SDIY is "a good way to save money." That's not the reason to do it!
Never mind why you want to get into building your own synthesizers, here's my attempt at a more realistic list of tools you'll need to get started without extreme frustration, including some notes on things that aren't necessary but are nice to have. This is mostly based on looking at what's on my own workbench. Whether you're building from full kits like those in the North Coast Synthesis online store, "PCB and panel," or doing real DIY from a schematic alone, you'll need to set up your workshop along these lines.
Another common beginner question is about electronic components worth stockpiling for general use; that's covered in a separate entry.
Hand tools
Necessary: Needlenose pliers; diagonal cutters; two or three each of flat and Philips screwdrivers in small to medium sizes; utility knife (I like the kind with a disposable blade that can be snapped off a section at a time to get a fresh edge).
Nice to have, but not necessary: Combination wrenches ("spanners" to some of you) in different sizes corresponding to the panel components you use (the ones I keep on my workbench all the time are 5/16", 10mm, and 1/2" - SDIY really requires both metric and US measurements). A metal ruler graduated in both inches and millimetres. Basic non-needlenose pliers. Permanent markers, especially "Sharpie Ultra Fine"; it is useful to know that scrubbing with isopropyl alcohol, the same procedure used to remove solder flux, will also remove Sharpie ink from most smooth surfaces. Nutdrivers (5.5mm is my most commonly used size). The special tool for tightening knurled jack socket nuts without risking damage to the panel. "Automatic" wire strippers that work by gripping and pulling apart the insulation without a blade. A crimp tool for solderless terminals, such as are used on the better class of power wiring. Soldering gizmos - see section on soldering below. A few extra of the basic necessary tools, maybe in different sizes.
Not recommended: Wire strippers that operate by cutting through the insulation with a blade at right angles to the wire - you won't be able to get them adjusted to the wire diameter properly (especially with cheap wire that may not be exactly the correct diameter) and you WILL nick the wire.
Maybe a necessary evil: if you will be building your own ribbon power cables, you'll probably end up with one of the $40 IDC crimp tools with the red (rarely blue) handles and yellow plastic crimping die. These are sold in many different outlets under many different brand names but they're all alike worldwide and I think they must all be made in the same factory in China. These tools suck! But there's nothing else available until you get up to about the $700 level (and many of the brand-name manufacturer-approved tools are in the thousands of dollars range, at which point you might as well shell out the tens of thousands for a robotic production machine.) The $40 tool is nonetheless enough better than just trying to make do with a bench vise, that I do recommend it if you're planning on making your own ribbon cables. But seriously consider buying ribbon cables ready-made instead; you have to make a lot of cables before making them pays for itself.
Power tools
I don't think that any classical "power tools" are necessary for most SDIY, but if you will be getting into making your own modular panels, or enclosures for non-modular things like standalone synths and guitar pedals, then you will probably need a drill and ideally a drill press. The drill press is necessary if you'll be doing homemade PCBs, which I really don't recommend. Some people like handheld spinning tools ("Dremel" and its imitators) for general "hobby" applications but I've never seen a compelling reason someone would need one for SDIY in particular.
You can certainly find ways to use a laser cutter, 3D printer, robotic milling machine, metal lathe, and so on, but these are more in the nature of separate hobbies in themselves rather than directly part of SDIY.
Soldering
Necessary: A soldering iron with at least a fixed-temperature thermostat. Adjustable temperature is nice to have but not absolutely necessary starting out. I won't go into much detail on the soldering iron here because it's the only point that everybody covers in detail when advising beginners; maybe I'll take a stab at it myself some other time. But I'll say that beyond the iron itself you really need a proper stand for the iron - when you buy a low-priced iron sometimes all you get is the iron itself with no stand, or a really bad one. (The Weller W60P, for instance, which is quite a good basic iron and the one I most often use myself, just comes with a piece of sheet metal you're supposed to fold into a stand, and that's dangerous to use and better thrown out.) For safety reasons you need a stand with some kind of sleeve, or the traditional spring, into which you can slide the iron when you set it down and then grab at the iron without looking and be pretty sure your fingers won't hit the hot part. Finally, you need some kind of tip cleaner. A sponge with slits cut into it is traditional but most people today prefer a metal coil (like a stainless steel pot-scrubber soaked in water). The coil is more efficient but also wears out the tip faster. If something like this comes with your soldering iron stand, great, but you can also just go buy a sponge or pot scrubber where household cleaning products are sold, cut slits in it in the case of the sponge, and use that. There's no need to pay more for one specifically sold for use with soldering irons. (If you go the sponge route, be sure to get a cellulose, not plastic sponge; the plastic one will melt.)
You need some way of holding components in place on the board while you work on them, especially when you're doing traditional through-hole. I usually use some combination of pieces of electrical tape and Blue-tac (sometimes called "poster putty" or by other brand names - a sort of rubber glob that can hold things in place and then be removed).
Ventilation: It's important not to breathe the smoke and fumes from soldering, especially if you are working lead-free (because lead-free solder is applied at a higher temperature and produces nastier smoke; the metal itself, lead or not, is not the main health risk for the person actually working with the solder). People's sensitivity and level of concern about this vary. You can get elaborate "fume extractor" systems which suck the smoke away from your workspace; at the very least you should probably have a fan to blow the smoke out of your face, and general good ventilation. See comments on workspace, below.
Nice to have: A flux pen. I recommend using one with no-clean flux; many of the places where you'd need to use it are places where it's difficult or inadvisable to use water-soluble flux. I've seen this on some people's lists of bare necessities and that surprises me. The solder you'll be using comes with built-in flux which is almost always sufficient to get the job done. The pen is usually just for making it a little pleasanter on especially tricky joints. Different sizes of spare tips for the soldering iron. Desoldering tools or supplies. You can either go for a desoldering pump, or a spool of desoldering braid. I get the best results with the braid, but I've found it absolutely necessary to use one specifically intended for the type of solder I use (that is, lead-free); I've had terribly frustrating results trying to use old braid that was meant for lead solder, on new lead-free joints, maybe because of limited shelf life or maybe because of the different temperature. A clip-on heat sink may help you feel better about working on some heat-sensitive parts, though the clip leads I recommend as test equipment can serve this purpose without your needing to buy a specific thing officially called a "heat sink."
If you want to play with surface-mount, you may get some benefit from a hot air gun (also handy for shrinking heat-shrink tubes, though I wouldn't buy it just for that) and there's a whole rabbit hole you can dive into of homemade reflow oven technologies, which usually start with buying a used kitchen toaster oven in a garage sale and then possibly modifying it with a customized temperature controller. Surface-mount tools might also include tweezers, a syringe-type paste applicator, and so on. They're mostly beyond the intended scope of this article.
Cleaning: Stuff for cleaning off solder flux counts as "nice to have" if you're working with no-clean flux, but "necessary" if you're using water-soluble flux. I suggest a paintbrush (I use a 1-1/2" natural bristle brush with the bristles cut short to make them stiffer) and 99% isopropyl alcohol. If you can't get that alcohol, then a lower percentage, or ethyl alcohol instead, are okay. Solvent specifically marketed as flux cleaner is usually ethyl alcohol with traces of other things, partly to improve its function as a solvent and partly to make it undrinkable. If it's an industrial product worth taking seriously then it will have an official safety data sheet explaining exactly what's in it, and you can entertain yourself by noting that "rubbing alcohol" sold specifically for the purpose of rubbing it on your skin usually warns you on the safety data sheet that you should take precautions to avoid skin exposure. Be sure that the solvent you use is something that will evaporate without leaving a residue. Products sold under the name "rubbing alcohol compound" or similar often have stuff like camphor mixed in to make them undrinkable and to provide some benefit in their intended medical application. Camphor doesn't evaporate and will leave your boards dirtier than before. Even with water-soluble flux, after you do the main cleaning with water, it's a good idea to go over it with alcohol afterward to remove the slow-evaporating water.
Work space and storage
Necessary: Beginners often underestimate the requirement for an appropriate work space. You need a decent-sized bench, table, or desk where you can spread out all your stuff, plug in your soldering iron, and so on. You need bright lighting for it, preferably from several directions at once to reduce shadows. I use three desk lamps on arms which I can swing around to shine on my work from different directions. For soldering, you need good ventilation.
Many people try to work in temporary spaces (e.g. the family kitchen table) where they have to pick everything up and put it away at the end of every DIY session. If that's a hard requirement for you, okay, you do what you have to; but having a dedicated work space where you can leave things set up for an extended period and not have little sisters, cats, or other family members interfere, is sufficiently "nice to have" that it borders on "necessary."
Nice to have: A vise. I don't list this as a necessity but some people would. Really, with some care you can usually do fine just setting the workpiece on the bench surface and working on it there; but it can be nice to have it held more firmly in place. I usually work without a vise but I have a small one I pull out and set up when it seems like it'll help. At the high end there's a product called Panavise, which is a modular system of bench-top vises and different attachments specifically meant for holding circuit boards at adjustable angles; that's nice to have but costs at least a few hundred dollars and there are a lot of other things it would make sense to spend money on first. A static-protective surface, possibly with an anti-static wristband that connects to it. Typically you can get a rubberized static-dissipating mat that you unroll over your work surface to reduce the chances of damaging components. However, static is not really an issue for the bipolar analog electronics used in synthesizers, and even the MOS-based digital stuff isn't very delicate these days, so static protection while working isn't as big a deal for SDIY as it would be in some other realms of electronics. One side benefit to getting an anti-static mat is that when you're forced to work in a temporary location like on a kitchen table, your anti-static mat can help keep the table clean and undamaged, which may be good diplomacy toward other users of the space.
Storage: You need some way of storing your tools and components when you're not using them, and the space requirements for components in particular will tend to grow over time. If you're disciplined about it (labelling, in particular, is important) you can go a long way just by saving and re-using the cardboard boxes in which mail-order components arrive. Nice if you can afford it, but lower-priority than stuff like test equipment, is to go to Uline or similar and get industrial modular wire shelving and stackable bins. I use smaller conductive stackable bins for storing partly-built projects and larger plain plastic stackable bins for inventory components (which, if static-sensitive, need to be in their own shield bags inside the bins). Sadly, I don't get any referral bonus for those links - I include them only to make clear the kind of product I mean, not as specific recommendations of where to buy.
Test equipment
In order to build electronic equipment, you need to already have some electronic equipment. I think the answer to the chicken-and-egg question that implies, is "Nikola Tesla." Test equipment is one of the things people usually leave out of the price estimate when describing how much it costs to get started in SDIY. The only piece of test equipment I'd consider an absolute necessity for an SDIY beginner is a multimeter; other items on this list are described in more or less the order I think you should buy them. Each could be the subject of a Web log posting all by itself, so this is just a brief summary.
Multimeter: These days only digital multimeters are practical. I have heard some claim that analog and digital multimeters have different strengths and weaknesses and so ideally you'd get one of each, but I think that's mostly some kind of life-is-fair fallacy, as well as an outdated impression of the disadvantages of early digital multimeters decades ago, which no longer are relevant to the present generation. At this point, especially as a beginner, really the best thing to do is shell out maybe $200 or so for a pretty good digital multimeter and leave it at that. You need to be able to measure voltages (down to millivolts and up to about the scale of your synth power supplies), currents in microamps to a few hundred milliamps, and resistances between one ohm and maybe 10 megohms. Extreme precision is not needed and will cost a lot of extra money. You can spend much more money trying to get the very best digital meter, or an analog one as well as the digital one, but you're probably better off putting that money toward the next few items on the list. "Nice to have" features for digital multimeters include component-testing ranges (I use the "diode test" on mine all the time - it's useful for general sanity checking on entire circuits, not only diodes - and the capacitor and transistor ones occasionally). Some meters have "auto-ranging," which is presented as a selling point and some people like it, but I honestly find it annoying and prefer to use a meter without that. In practice, I always know what range my measurement ought to be in, and if it's not there, I'd rather be told "out of range" than have the meter switch to a different range and not make it instantly obvious that something's wrong.
It is worth having both pointed probes and clip-type leads for your multimeter, and buying the other one if it doesn't come with both.
Alligator clip leads: Seriously, these are like $10 for a double handful, you need them all the time when testing things, and people don't usually think of them at all when making lists of necessary test equipment. They can also double as clip-on heat sinks for soldering sensitive components.
Bench power supply: It was a toss-up whether to list this before or after the oscilloscope, but I think most SDIY builders will end up needing a bench power supply before they really need the 'scope. Obviously, you need some kind of power supply to power your modules at all once you build them; but I'm talking here about a separate power supply for benchtop testing, which has somewhat different parameters. The one I use is typical: it has three outputs, two of which are adjustable voltage 0 to 24V and the third fixed at 5V. There are current and voltage meters for the two adjustable outputs on the front panel. Each output has "floating" positive and negative rails so they can be put in series to generate the "split" power supply usually required by analog circuitry, and the two adjustable ones can be set to "track" at the same voltage. So I usually have mine set to generate Eurorack power (+-12V and +5V) and it could also easily produce +-15V for other synth formats. One of the key features of this kind of supply is current limiting: you can set a maximum current and then if your circuit tries to draw more than that, the power supply just drops the voltage as necessary to prevent it going over the maximum current. When you have a build error in your circuit, current limiting often means the difference between getting a red warning light and a chance to fix the problem with no damage, or getting a small explosion and a bunch of ruined components to replace. You should expect to pay between about $200 and $300 for a decent, probably Chinese-made, bench top power supply in this class. You can probably get it down to about $100 and still have something worth using if you shop on AliExpress and delete features you don't absolutely need. I advise caution in thinking "I'll build my own power supply!"; safety considerations make that not an ideal project for beginners, and it's doubtful whether you can really save money on a homemade bench supply because a lot of the price tag for this particular item is going to things like the power transformer itself and the digital panel meters, which you can't realistically make from scratch and would have to buy at prices higher than what the Chinese manufacturers are paying.
Oscilloscope: Pretty much the circuit-debugging tool. There are three kinds you would be looking at as an SDIY beginner: toys, which are along the lines of Arduinos or Raspberry Pis with little LCD displays (or even just the same software running on a PC or tablet and using the microphone input); basic digital bench-top oscilloscopes (Rigol or Chinese off-brands); and analog oscilloscopes from flea markets. The price of any oscilloscope pretty much goes in proportion to its bandwidth, which measures the highest frequency of signal it can measure, and we're lucky in the analog synthesizer realm because the signals we deal with are in the range of at most a few tens of kilohertz. (Top-end oscilloscopes used by cell phone manufacturers' labs, with bandwidth in the gigahertz, can cost upwards of one million dollars.) Toy oscilloscopes typically have just enough bandwidth to cover audio, and are typically priced in the $30 to $80 range - maybe even free of charge if you just download "oscilloscope" software to run on your PC. They are not great, but a whole lot better than nothing. If you look at oscilloscopes meant for general electronics, not only analog audio, then you might be looking at something with a bandwidth from 10MHz to 50MHz, whether analog or digital. That's far more than you need for audio, but it may be useful if you're also interested in the digital microcontrollers used in some synth circuits; and it's also about as low as you can go on bandwidth and still be dealing with a "real" non-toy oscilloscope. As with multimeters, if you are looking to buy an oscilloscope new, then digital is the only realistic choice; claimed advantages of analog scopes are less relevant with the current generation of digital than maybe they once were, and newly-manufactured analog scopes still are made but aren't easy to find. Then you're looking at paying somewhere from $200 to $700, and (especially at the higher end of that range) you can expect to get some extra features like a second input (very nice to have), and on-screen measurements for times, phases, voltages, and so on. Old analog oscilloscopes with similar bandwidth, preferably dual-input, are available used in the $50 to $300 range. They will have fewer of the spiffy measurement features, and they'll be physically bulky, but they are still very usable and superior to both the toys and to having nothing at all. The biggest thing, really, is that you'll get a lot of benefit from having an oscilloscope at all.
Breadboard: Priority for this depends on how "DIY" your "DIY" really is. If you're building from kits, you probably don't need it at all. By the way, through North Coast Synthesis Ltd. I sell a range of high-quality kits with exceptionally easy-to-follow build instructions, and your support of my business is what makes it possible for me to provide public resources like this Web log. But if you're not building from kits and you want to experiment with modifying designs, working from poorly-documented schematics you download from places other than North Coast, or even inventing your own circuit designs, then you'll probably want an easier way to put together circuits for testing without soldering them up, and that's where the breadboard comes in handy. Be careful of quality with this: you can get them for like $5 each from Tayda in Thailand, but the ones obtained that way may be almost-disposable quality with flimsy and intermittent connections. You may be better off spending more like $20 for one that will be more reliable.
Signal generator: It's nice to be able to feed a controlled signal with known parameters into your circuit. If you have a modular synthesizer, your synth basically is a signal generator and can be used to sub for a standalone device; but if you're in the process of building your synth, you may feel some need for a different source of signals. This is the sort of thing I would keep my eyes open for at flea markets; you can certainly rush out and buy something new but most of us don't need to do that.
Digital device programmer: If you're programming your own microcontrollers, you may need a programmer which plugs into your computer and allows it to download software into the device; at one time you'd usually need a separate one of these for every model of device you wished to program, but nowadays they are usually pretty universal, or at least at the level of a single "programmer" that works for a given chip manufacturer's entire line. Most SDIY beginners won't be looking at programming microcontrollers right off the bat, though. If you need one of these, expect to spend between about $50 and $600 depending on how many "comfort" features you want and the specific devices you want to program; don't shop for one until you have a specific project in mind.
Other test equipment: Very many pieces of specialized test equipment exist (audio analyzers, impedance bridges, spectrum analyzers, different kinds of digital-logic analyzers, and the list goes on). Basically all of these fall into the category that if you needed one, you would know, and as a beginner, you can pretty much ignore it. The other items on my list, with careful use, can usually substitute. The more exotic tools exist primarily for use in large commercial labs where time is money and it's worth spending some money to get a thing that can solve a specific testing problem faster than the general-purpose oscilloscope or multimeter would.
◀ PREV Walking the hypercube || Transistors for the Perplexed NEXT ▶
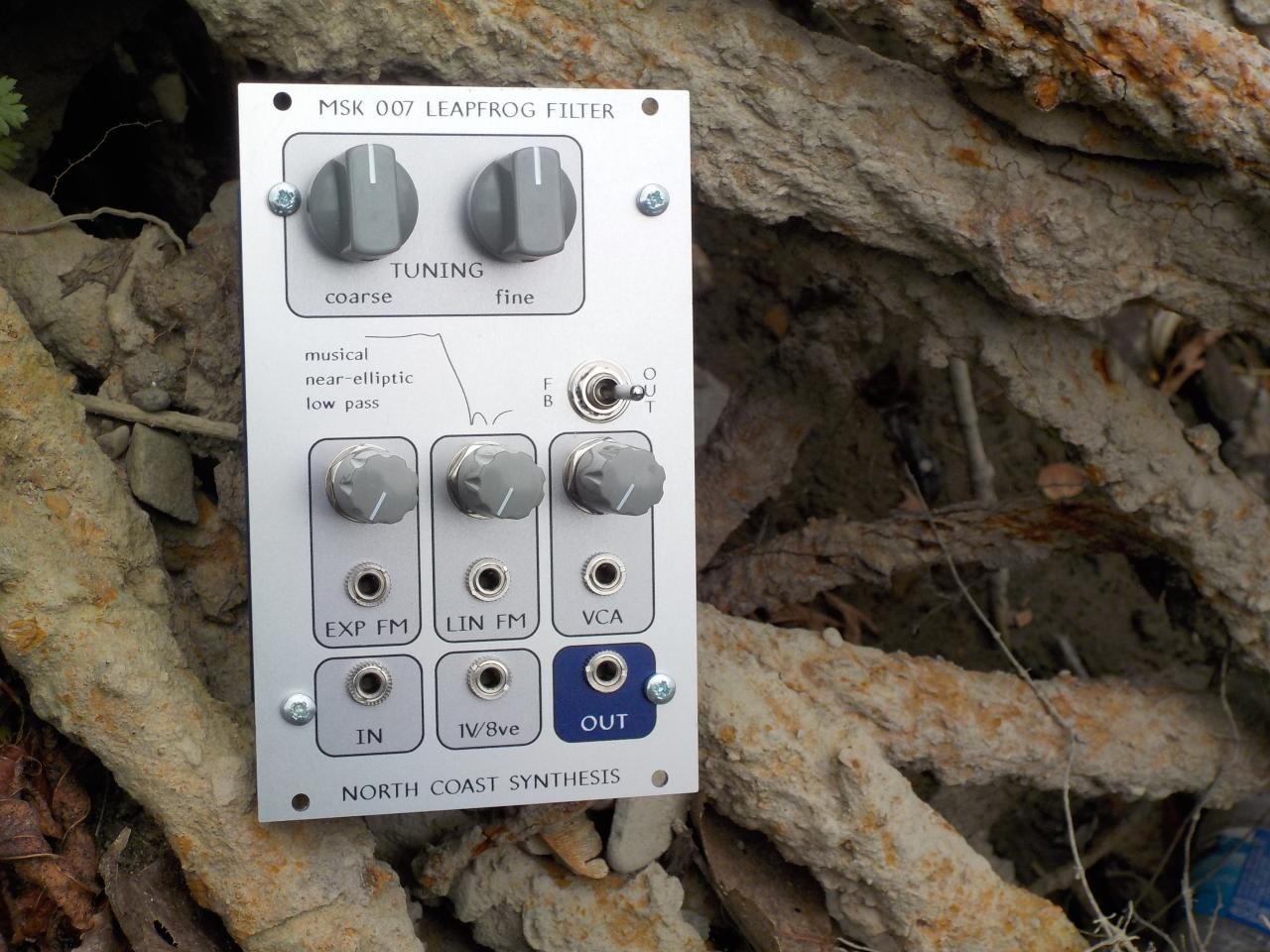