Green modular, part 4: Wood, and toxic waste
2019-02-22 environment chemistry PCBs
In this part of the Green Modular series, I'd like to talk about wood, and toxic waste. Part 1 focused mostly on saving energy; in parts 2 and 3 I wrote about metals, and some of the environmental issues related to metals are caused by their toxicity during waste disposal. But there are also other kinds of toxic substances relevant to synthesizers, and those become important during manufacturing rather than at the end of the product's life.
Wood
There isn't a lot of wood used in synthesizers and that's partly why I'd like to mention it: to make the point that other kinds of musical instruments also have important environmental consequences. If someone wants to prefer acoustic instruments over electronic for purely aesthetic reasons, fine, but if the talk turns to a claim of environmental superiority of acoustic over electronic instruments, well... it may not be so simple.
Rosewood is a big issue for musical instruments in general. That word is sometimes vaguely applied to many different woods that are botanically unrelated, but the so-called true rosewoods are those of genus Dalbergia, including Brazilian rosewood (D. nigra); East Indian Rosewood (D. latifolia); and cocobolo (D. retusa). These are used for the bodies of stringed instruments like guitars, as well as for general applications in fine furniture, which makes rosewood appear incidentally in many other instruments that may happen to have wooden parts. African blackwood is usually not called "rosewood" but is actually a Dalbergia species too, D. melanoxylon. That's a traditional material for wind instruments like clarinets, oboes, and bagpipes. Without Dalbergia wood, the average orchestra would certainly look and possibly sound a lot different.
The many species of Dalbergia vary a lot in how endangered they are, with some being in much worse straits than others, but in general, these are all slow-growing trees that grow in disappearing specialized habitats and have been heavily overharvested in the past, so there are a lot of problems with continuing to cut down such trees to build acoustic instruments. And since 2017, there have been CITES (Convention on International Trade in Endangered Species) restrictions forbidding international trade in all species of Dalbergia. Narrower bans on the most endangered species have been in place longer. As this article from Reverb describes, persons travelling with rosewood-containing instruments face obligations and difficulties getting the proper permits and other documentation to carry their instruments across international borders. Part of the reason for making the ban so broad is that it's hard to verify exactly what species of tree, and which population, any given piece of wood came from.
Professional-quality bows for violins and similar instruments are traditionally made of pernambuco wood, also called brazilwood. The country of Brazil is named after this wood. There've been attempts to substitute other woods, and high-tech materials like carbon fibre, but so far nothing else is really considered to be as good. And the tree that produces pernambuco wood only grows well in long-undisturbed South American jungles. Excessive pernambuco logging going back centuries, and destruction of the forests to clear land for other uses, has made it an endangered species. It's listed as such on the IUCN Red List and subject to trade restrictions under CITES. In general, buying and selling this wood internationally in unfinished form has been illegal since 2007. It remains legal to travel with existing completed bows, but musicians who use them are often advised to carry documentation to help avoid problems when crossing borders. And the trade restrictions are certainly making it that much harder for any new bows to be created. About 15 years ago Smithsonian Magazine had a pretty good article called "Saving the Music Tree" about pernambuco conservation, which is one starting point for reading further.
Then there is ebony, traditionally used not only for the black keys on keyboard instruments, but also for miscellaneous smaller parts in many other instruments - fingerboards, tuning pegs, even guitar picks. (Pianos have white keys, too, of course, but I won't get into the issues surrounding ivory; that isn't a wood.) The term "ebony" properly refers to several different species, grown in multiple locations around the world, and they don't all have the same conservation status. Some are more endangered than others. Ebony in many applications can be substituted by plastics, which are probably better for the environment, but there is ongoing customer demand for the real thing, and it puts pressure on manufacturers and on the environments where the trees grow. The Gibson guitar company was in the news for a while in 2011 and 2012 because of repeated raids of its factories and seizures of illegally-imported Madagascar ebony. At that time they were making an effort to switch to ebony grown in India; but although better, Indian ebony is still not completely harmless to the environment.
There are three species of mahogany (Swietenia), of which only Honduran mahogany is used today in significant quantities. It is listed as "vulnerable" on the IUCN Red List, and holds the dubious distinction of having become in 2003 the first major hardwood to be restricted by CITES. Many of its applications are more in furniture than in music, but it sees application in some of the same places as rosewood, for things like guitars. It's also considered to provide a very good "warm" tone in drum shells. I'm mentioning it here largely as an excuse to link to this video from the Acorn to Arabella project. These guys are building a wooden boat from scratch, and at this point in the project they're respectfully, maybe I can even say reverently, disassembling another boat that has reached the end of her life, to reclaim as much as possible of the nowadays unobtainable old-growth Honduran mahogany from which she is made. Whether we're making boats, furniture, or musical instruments; out of wood, plastic, metal, or even software; I hope all of us who make things can have that respect for the materials.
Semiconductor manufacturing
Solid-state electronics all comes down to semiconductor wafers, usually high-purity silicon, rarely other substances like germanium or gallium arsenide. These are produced in specialized factories called "fabs" under extremely tightly controlled conditions, and it's an environmentally expensive process.
First, there is the semiconductor material itself. Silicon is smelted like a metal out of its oxide, quartz - usually in the form of sand. That in itself is not a huge environmental issue. There are in some issues with sand being in short supply in some places in the world, but its use by the semiconductor industry pales in comparison to that of the construction industry and sand consumption is not really on the radar as a big problem for electronics. It's smelted using a process somewhat like those used for steel and aluminum, using carbon in an electric arc furnace to separate the silicon from its tight bond with oxygen. Then there are multiple steps involved in refining it to the ultra-high purity needed for electronics purposes. The main issue is simply the amount of work, and therefore of basic inputs like energy, needed to do all this processing.
Processing silicon into components involves many steps of adding and removing layers of other materials on the surface of the wafer, modifying it by exposure to radiation and specific gasses and environments (vacuum, ion beams, etc.), and above all washing. After nearly every step the wafer needs to be washed with ultrapure water. Some of the reagents used are quite dangerous (for instance, hydrofluoric acid), but at least they tend to be used in very small quantities, so that the total amount of waste involved is also small. The water consumption is probably a bigger impact: all that washing requires a source of clean water, all the more so because raising water to the ultra-high purity needed has the effect of wasting some, and the total can be significant, especially for a fab located in a place like California where clean water may not be plentiful.
There can be concerns over toxic solvents used in semiconductor manufacture for dissolving things that won't dissolve in water - whether in the context of process chemicals, or more washing and cleaning operations. The US government designates heavily polluted places needing special clean-up as what are called "Superfund sites," and there are 23 of them in Santa Clara County in Silicon Valley, more such sites than in any other county of the USA. Many of these are associated with old semiconductor plants, and much of the pollution is from trichloroethylene (TCE), a solvent formerly much used for cleaning and degreasing electronic components and assemblies. It gets into the groundwater and then is nearly impossible to remove. Another important pollutant in such sites is 1,1,1-trichloroethane (also known as "methyl chloroform"), used for similar purposes. That one is less toxic, but a serious ozone depletion threat; tradeoffs between different hazards are sometimes significant. Chlorinated solvents like these have become less popular since the mid- to late 20th Century because of their effects on human health and the environment, but much damage from that era remains and will take a long time to naturally dissipate or to be cleaned up.
At left trichloroethylene, at right 1,1,1-trichloroethane.
I titled this section "semiconductor manufacturing" and it's probably the case that the worst of the environmental impact from electronic component manufacturing is that associated with semiconductors. Because the materials for semiconductor ICs need to be purified so much and processed through so many steps, per weight of final products there are more toxic substances to dispose of from, and water and other resources consumed by, an IC fabrication facility than let's say from a factory that makes resistors or capacitors. Those are basically just high-precision chunks of ceramic or plastic, and their environmental impact tracks that of manufactured products in general. However, in principle similar issues can apply to all the electronic components that go into a synthesizer.
PCB manufacturing
First, let me be clear that "PCB" in this context means Printed Circuit Board. I'm not talking about polychlorinated biphenyls, also known as "PCBs," which were a class of substances formerly used in some electrical applications and banned decades ago because of their extreme environmental toxicity. I have heard tell of people encountering that other kind of "PCBs" when restoring some very old Hammond organs and similar historical electronic instruments, because polychlorinated biphenyls were used as dielectric material in oil-filled capacitors; but such stories have become rarer and rarer over the years and today you'd have to look pretty hard to find polychlorinated biphenyl-dielectric capacitors in real life.
PCBs in the sense of circuit boards are the rigid boards to which components are fastened with solder to make up circuits. This form of construction is nearly universal in modular synthesizers. There is a division between "through-hole" construction, typically used in handmade products like mine, and "surface-mount," more often used in robot-assembled products, but the circuit boards themselves are made by the same processes with the same environmental footprints.
As the name implies, printed circuit boards are made by a printing process, usually some form of photolithography, in which different layers of metal, plastic, and paint are added to a substrate which nowadays is usually glass-epoxy. There are multiple steps of gluing on metal foil, etching away parts of it, and then adding different kinds of plating, and it's those metal-processing steps that are probably most significant for the environment. After etching away the unwanted copper from a board, the manufacturer is left with a toxic soup of dissolved metal salts. What's to be done with that?
PCB manufacturing is especially likely to worry people because it's usually outsourced to contractors in China in particular, and there's a popular image in the West that Chinese factories routinely just dump waste directly into rivers.
There are a few important things to understand about that, however. First, environmental regulations do exist in China. The Chinese government works on the basis of long-term plans, much more so than is true of Western governments; there's a saying that the Chinese government plans by decades, while the US government plans by Presidential terms. The Communist Party doesn't want to trash the planet or the local environment in a way that will cause them problems 50 years from now, because they still intend to be in power then. That does change the priorities - in particular, they may be more likely to prioritize longer-term issues like climate change over some of the other environmental stuff we might care about in North America - but it also means that the things which really will make a difference on that time scale, do get regulated and do get enforced. Many of the photos we're shown of environmental disaster areas in the Far East are actually of "artisanal" recycling facilities where small operators break down used products - not factory manufacturing, which is more heavily regulated.
Second, North American governments are not necessarily so good about environmental regulation and enforcement as citizens like to pretend. As I write this, the US federal government's environmental agency recently spent more than a month shut down, just so that their President could make a point about immigration. Even before the funding ran out, he and his party were trying their best to kill the environmental agency and just not have environmental protection anymore. I'm located in Ontario, Canada. The provincial government of Ontario was recently forced to walk back its initiative of creating exceptions to environmental regulations to make its own point about being "open for business"; and the federal government of Canada has redesigned its environmental assessment process for large projects to prioritize "intersectional feminism," to make a point about that, over real environmental issues. The common thread is that all these governments, some on the left and some on the right, put the environment in second place to scoring points for their unrelated political agendas. It's not clear we are really better in the English-speaking world than China is when it comes to the actual results.
A third, and really important, issue for circuit board manufacturing is that many of the toxic substances produced are not exactly waste and are not just thrown out. The dissolved copper, nickel, gold, and other metals in spent etching solution are worth enough money that nobody doing this work on a serious commercial scale discards that stuff; instead, it is reprocessed to recover the metals.
As a designer, I outsource my board manufacturing to contractors who at least are legally required to handle the waste responsibly, and I don't worry too much about it beyond that. To be honest, I have more concerns about some basement DIYers in North America and Europe who etch boards at home - it's hard to believe their chemical waste is being properly reclaimed, simply because doing so is out of reach of the average hobbyist. And the cavalier attitude I've seen displayed by electronics hobbyists towards substances like peroxide-boosted acids doesn't inspire my confidence about personal or environmental safety. Better to leave it to the professionals.
One small detail, which I'm not sure really makes much difference in the grand scheme of things but it at least makes me feel better, is that I try to leave as much unetched copper in my board designs as possible. Compare these images of a North Coast PCB (from the Dual Octave Switch) and a classic PCB from an earlier time (Buchla 281). I used a rendered image rather than a photo for the North Coast board because the real ones are covered by a plastic solder mask that makes the copper hard to see in photos. Both boards are made by starting with a sheet completely covered in copper foil and then dissolving away all the copper that will not be in the finished product. The board with lots of empty space on it uses up much more etching chemicals to do that, and even though the resulting waste will be recycled, it's lower-impact not to generate it in the first place. My board covers almost all the spare area with copper, saving my contractors from needing to expend chemicals removing that copper.
The main reason for using a copper fill over most of the surfaces of a circuit board is actually electrical rather than environmental: keeping the extra copper helps maintain a low-impedance connection to ground, which fights noise and interference. But leaving a lot of copper on the board also doesn't hurt for the environmental friendliness of the manufacturing process.
Final assembly
Once the components are made and shipped to me, I assemble them into final products, and the environmental impact of that is important to me because it happens on my watch, so to speak, and I have some direct control over it. I'll talk in Part 5 of this series about the simple municipal garbage associated with my operation. Other than that, the main activities of North Coast that have environmental impacts are applying the solder, and washing off the flux afterward.
Soldering produces fumes and smoke, mostly from vaporizing the flux used to make the liquid metal sticky. This flux is basically a purified form of pine rosin, or a synthetic material with very similar properties. It's not good to breathe the smoke, and so I use an exhaust fan to expel it from my work space - but isn't that just turning it into an environmental hazard for others? In fact, I don't think that this is a big threat, because (as with many of the other points I've described) the amounts are so small. One good wood bonfire puts out more smoke than a year's worth of module assembly, and the composition of the smoke is not much different. Flux fumes are also not really persistent in the environment; that stuff is organic acids of the kind that naturally occur all over the place, and it will be degraded very quickly by natural processes, much like other smoke.
Removing the flux residue on the boards after soldering is a more interesting question. I use "no-clean" flux which is supposed to create a stable, harmless residue that doesn't need to be cleaned off at all, and when I first started making modules for sale I took that seriously and did not clean off the flux residue. After all, there's no environmental impact from disposing of solvent if you don't use solvent in the first place. But I quickly learned that removing the flux residue is a commercial necessity. After a few loud public complaints about "low build quality" and "sloppy soldering" in North Coast modules (from idiots who didn't know what quality actually looks like but it doesn't matter: they talk, and others listen) it was clear that if I'm going to stay in business then I have to ship modules with cosmetically attractive circuit boards on them and that means removing the soldering residue even when it's no-clean. Maybe I can make it up to Mother Nature some other way. There are other reasons to want to remove flux residue, anyway. In particular, in some high-impedance applications like sample and hold circuits, the minuscule leakage currents through no-clean flux that we would normally ignore, can cause problems.
So I wash my boards after assembly with isopropyl alcohol. Many factors go into the selection of solvent. First of all it has to be something that actually will dissolve the flux. For the flux I use, water won't work. There are such things as water-soluble fluxes, which some people prefer because they're especially effective at making the solder sticky, but they have tradeoffs in being themselves corrosive. If you use water-soluble flux you must wash with distilled water, sometimes even in the middle of assembly because the corrosion can become a problem within less than an hour after the flux is applied, and then you're faced with disposing of the metal-contaminated wash water (which, I suspect, many small operators would just put down the drain). Fluxes like mine that don't wash with water need something in the nature of a polar organic solvent, like an alcohol.
I put in a photo of some molecular models because those are fun. Water at centre; then clockwise from top right, these are isopropyl alcohol, ethyl alcohol, methyl alcohol, acetone, and a heptane isomer (2,3-dimethylpentane).
The alcohols are probably the most sensible choices for removing flux. Methyl alcohol is too toxic for me to be comfortable using it - it can be absorbed through skin, so I'd want special gloves and probably a respirator, and it doesn't really have any advantage for my purposes over the others. Ethyl alcohol works well, is often used for flux cleaning in this industry, and it is one of the least toxic solvents available; but the low toxicity is itself a problem, because this stuff is the same form of alcohol found in alcoholic drinks: an addictive mind-altering drug. So ethyl alcohol is a controlled substance. The authorities go to some lengths to see that ethyl alcohol is either highly taxed, or that it has other things mixed into it to make it less appealing for people to drink, and those other things often cause problems when it's to be used for cleaning in particular. I've had plenty of bad experiences with industrial ethyl alcohol leaving a residue after it evaporates, leaving the objects I was trying to clean dirtier than before. Such problems can be avoided with careful attention to exactly what's in the alcohol, and so it does end up being a good choice with some care, but there are still some headaches involved. Ethyl alcohol (to a lesser extent methyl) is also of note as the most common solvent for the shellac finishes used on fine wooden instruments like violins. Isopropyl alcohol is nice because it has the right level of toxicity: poisonous enough that it is not thought very many people will try to drink it, while still being non-toxic enough that I'm not too worried about being exposed to it in a well-ventilated work area.
As for the other two solvents in the picture, the heptane isomer is an example of one of the many things that might be in the mixture of an "oil-based" paint thinner/petroleum distillate type of product. Solvents like those are not commonly used in electronics because they don't dissolve well the things we usually want to dissolve, but I do keep a small bottle of paint thinner around for use when I do occasionally have a special cleaning job that requires it. Acetone is an interesting one. I don't normally use it because it may dissolve or damage some plastics and provides no particular advantage over isopropyl alcohol for removing solder flux. However, acetone is special in that it is not considered a "volatile organic chemical" (VOC) in some environmental legislation, and that in turn is because acetone is thought not to contribute significantly to ground-level smog in particular. The VOC rules were written especially to combat smog in places where smog is a big problem, and some flux-cleaning products based on ethyl or isopropyl alcohols have notices in their data sheets saying that in certain jurisdictions you're supposed to dilute them with acetone to meet the VOC rules. That's another example of the trade-offs among different environmental considerations: acetone is probably at least as toxic as the alcohols, but it's less of a smog problem, so if smog is the priority, you trade off for low smog.
In this part of the "green modular" series I've written about tropical hardwoods and their use in musical instrument construction, even though those are mostly of concern for other instruments than synthesizers in particular. My point there is that everything has an environmental cost, and if someone has a distaste for electronic technology, they maybe shouldn't use the environment as justification. Then I've also covered several angles on toxic pollutants that are legitimately associated with electronics. In the next and probably final part of the series, I'll talk about some of the environmental issues I think about in running my office and the mail-order side of the business.
◀ PREV Green modular, part 3: More metal || Green modular, part 5: Behind the scenes NEXT ▶
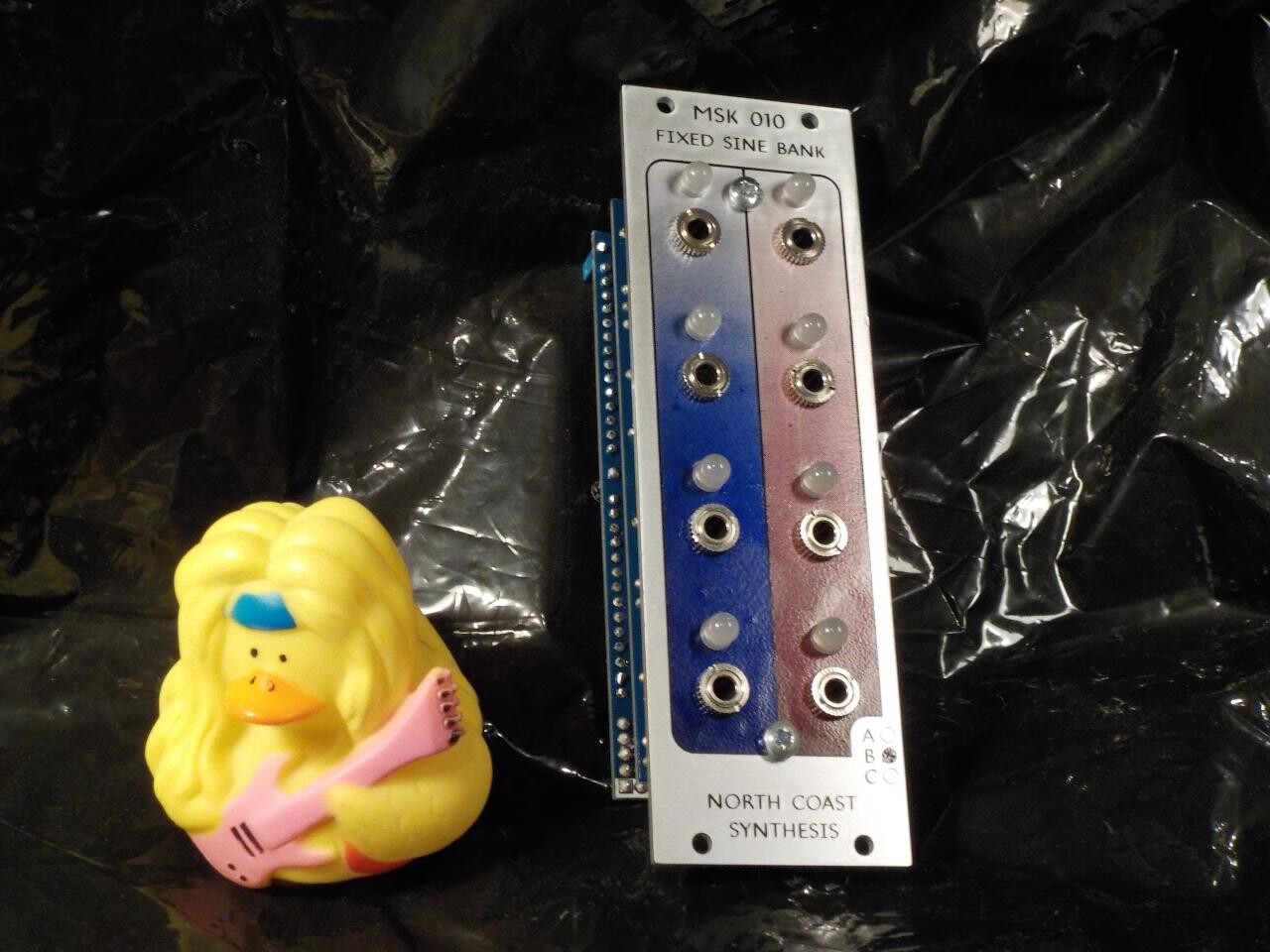