Green modular, part 5: Behind the scenes
2019-03-20 environment
In this final part to the green modular series I'll talk about environmental and related issues associated with the modular business, going beyond the manufacturing of the modules themselves. We began this series with RoHS and there may be a temptation to end it there as well: if the actual products are free of a short list of toxic chemicals, they're environmentally friendly, right? Someone who really cares about the environmental impact of buying and using modules should be looking at the whole business.
You can start reading this series with Part 1.
Paper and printing
Every module that goes out my door goes with a few pages of laser-printed paperwork; usually at the very least a shipping label and an invoice, often one or two other documents depending on Customs requirements. Every incoming package of parts comes with at least an invoice or packing list, and usually several pages of Customs papers. On top of these documents there are statements and invoices from banks, credit card processors, online service providers of different kinds, and so on. I use printouts for internal physical control of manufacturing. Many of my customers will choose to print the electronically-provided manuals for my products, which may be substantial (52 pages in the case of the Fixed Sine Bank, even more for some other modules).
It's not realistic to expect business to run paperless. Nearly all of the printing I do really is necessary - the result of requirements imposed on me from outside. But one thing I do to help reduce the impact of all this printing is that I load my laser printer with 100% postconsumer recycled paper. All the fibres have been used at least once before; no new trees are cut down just to provide for North Coast's local printing needs. The recycled paper costs more than generic, but paper overall isn't really a big enough expense for this to be a problem.
If you go to an office supply store, at least in North America, and ask for "recycled" paper, there's a good chance that a well-meaning employee will direct you to packages with the Forest Stewardship Council "certified" logo on them. It's not easy to find out just what this logo means, and in particular, what percentage of recycled content a product must contain to qualify for the logo, but if you dig carefully through their Web site you can learn that the answer is zero. It's not really about recycling at all, nor entirely about the environment, but rather a vague, extremely political, and somewhat controversial definition of "responsibility" that covers a lot of non-environmental stuff like corporate governance and hiring unionized employees. The same organization does also have a recycling-related logo, but that's not the one you'll commonly be directed to look for. If you're specifically interested in buying recycled paper for environmental reasons, then you must - as I do - actually read the small print on the specific products.
While I'm on the subject of recycled paper, here's a useful tip for those configuring laser printers: if there is an option in your printer driver for "recycled paper," that is probably not what you want! The printer driver option is actually for printing on the unused side of paper that has already been printed on one side. Choosing this option may cause the printer to stop and prompt you to put the flipped paper in a special tray or something. If you are printing on fresh paper that has not been previously printed but is made of recycled fibre (that is, the ordinary meaning of "recycled paper"), you should configure your printer driver as you would for generic paper.
Beyond the paper, there's ink and printing itself. I use a relatively efficient laser printer, which saves some significant amount of waste in terms of ink and packaging compared to inkjet printers. I also recently decided to get a new toner cartridge and keep my 10-year-old printer going through at least one more cartridge's worth of printing, rather than buying a new laser printer. That decision has some cost in time and effort (because the old printer needs some careful margin adjustments on each print job) but it'll save the resources of manufacturing a replacement and disposing of the old printer for at least a little while longer.
Shipping
As I've mentioned before, the environmental impact of shipping for the modular business is considerable. The modular industry deals in small, high-value packages that are typically shipped long distances, air freight. There's a lot of fuel burned in jet planes to get your module to you. And there aren't a lot of other options. The product has to get to you somehow, and customers demand the speed of air freight. I wouldn't be able to stay in business shipping on the multi-week schedules of ground transportation. Behind the scenes of the final shipping of assembled product to customer, there are additional shipping steps from component manufacturers to distributors, distributors to me, and possibly from me to a module retailer. The environmental impacts add up.
One thing that can help is to make shipments as big as possible. It costs a certain amount of both money and energy consumption to send one package, no matter how small the package is. After a certain point, making the package smaller does not make it cost less energy to ship. That's one reason I no longer sell certain low-priced DIY items: the cost of shipping them was almost as much as the cost of shipping a full kit or assembled module, and there was never anything I could say to customers to get the point across that that's really what it costs and not some kind of "gouging" on my part. The customer who puts a $10 PCB set in the cart and then gets a $30 shipping quote does not (as I'd first hoped) turn around and buy several more items to make the shipping cost smaller in proportion. Instead, they just go away unhappy. But because it's really true that most of the cost of shipping is per package and not per weight or per item inside the package, I at least can apply the logic myself that that customer didn't: I can make my incoming packages as large as possible to reduce the cost of shipping in both money and energy. Buying the parts for ten or a hundred modules all at once - as many as I can afford to include in a production run - means the environmental impact of shipping them is proportionally reduced.
This is also another reason I don't encourage "PCB and panel." If you buy a set like that from a small manufacturer, there's the environmental impact of shipping the kit, and then there's also at least one package shipped to you from some other vendor for the other parts. One if you're buying all the parts from the same place, but that's seldom really possible; usually, you'll have to make two or more purchases on top of the "PCB and panel" purchase to get all the parts you need for a given project. As I've discussed before, every project requires a few new parts and you're not realistically going to be able to find them all in pre-existing stock. Buying full kits means you have just one shipment for all your parts, and you're participating in the lower environmental impact of the kit-seller's larger incoming packages.
For those buying assembled modules, a simple and effective way to reduce the environmental impact of shipping is to buy modules from local dealers wherever possible. Even though your purchase has to be shipped to your local dealer from the manufacturer wherever in the world, it's reasonable to guess that your local dealer is buying more than one module from the manufacturer at a time. That reduces the impact of shipping per module.
Packaging and packing material
Since I started running a mail-order business I've learned more than I ever thought I'd need to know about cardboard boxes. The ones I use are made mostly (maybe not all of them 100%; it varies) from recycled Kraft pulp. I can't really claim any special environmental consciousness, though, because these are the same kind of cardboard cartons everybody uses. Even the ones that look white (and therefore bleached) are usually just a thin bleached-paper surface over the same standard recycled Kraft material.
Inside the carton there's usually some amount of bubble wrap, and because of the need for static protection there's not a lot of flexibility on what kind of bubble wrap to use. It's plastic, which isn't great, and it's usually not recyclable. To the extent possible I do reuse the bubble wrap from incoming parts shipments; especially on outgoing shipments to retailers, it's often the same kind of bubble wrap for both, so I can just move any sheets that are in decent condition over to the next package. Only those bubble wrap sheets that have served their purpose by taking the damage that would otherwise have hurt my components, end up being thrown out. But for use inside module boxes, and for padding the flat envelopes I use for kits, I still have to buy and use some fresh bubble wrap. Just recently I finished my first large roll of fresh bubble wrap; here's the empty roll and the next one ready to be unwrapped.
Parts are usually shipped in plastic bags, plain plastic for most things and the shiny laminated shield plastic for semiconductors. I reuse bags as much as possible, especially in making kits, but there are a number of issues that limit how far I can do it. For one thing, the bags in which my suppliers send me components are usually bottom-rank in terms of quality. For parts inside a kit I like to use bags made of thicker, more rugged plastic, and that means buying new bags. Bags need to be consistent sizes or I won't be able to handle my finished kits in a uniform way, and that too can limit which bags I can reuse and how many of them I can reuse. I use reused bags wherever I think they'll do, for instance on relatively rugged components without a lot of sticking-out parts where the thinner plastic won't be a problem, but that is not everywhere. It remains necessary for me to buy some fresh bags.
Another issue for reuse of plastic bags is that when I get them, they usually have stickers all over them from the previous use. I have to remove those stickers to reuse the bags, and doing so basically requires washing them in solvent (I use isopropyl alcohol). Just peeling off the stickers leaves a sticky residue which will cause problems if it's left in place, and it can't really be removed except by dissolving it. The weight of solvent to bring a component bag up to the condition where I can reuse it is often greater than that of the bag itself, and I honestly don't know whether on balance that's better or worse than throwing out and replacing the bag. I think that, on balance, it's still better to reuse the bags than to throw them out. I do what I can to minimize the solvent used this way, and to reuse that as well to the extent possible. But it's not a gimmie, and it's an example of how really getting environmental footprint right can require some careful thought.
Recycling
What I can't reuse, mostly gets recycled. For cardboard boxes and office paper (which I shred, first) that's easy. A lot of larger electronic components, like the expensive panel potentiometers that nobody properly appreciates, come in vacuum-molded plastic trays and my local recycling system accepts those, too. There's still a fair bit of plastic film (shrink-wrap, etc.) that ends up going to landfill, but I'm usually impressed at how little total landfill waste my operation produces. Really, a whole lot gets recycled.
One of my long-term projects involves saving all the cut-off bits of wire from when I install through-hole components. There are a few hundred of these from every module I build, and they're nice metal, usually (in this RoHS era) pure tin-covered copper. After I have a few kilos of these I want to melt them all down and cast a bell or a gong or something.
"Fair Trade"
Even if it's not really an environmental issue, lots of the same people who care about the environmental impact of electronics also want to know that the people making the electronics are receiving a fair wage. The biggest single thing you can do to ensure products are clean in this respect is to buy products made in places where labour laws are real and are really enforced. Avoiding certain large corporations may be a good idea, too.
Unfortunately, experience has made clear that modular synth customers care about "fair trade" for electronics exactly until they realize that it costs money. My products are made in Ontario, where the minimum wage is $14, not in Shenzhen where it's $4. The difference in the price of labour has a real effect on my prices, because labour is a big part of the cost of a module or even a kit (all that counting and sorting). But the market doesn't gladly pay for higher labour costs in order to achieve better treatment of workers; the large majority of modular customers still demand that North Coast must compete on price with mass-produced Chinese-assembled products. And it would be even worse if I actually had any employees paid minimum wage (let's not dream of the somewhat higher wages considered appropriate for electrical engineering work). At the moment I'm not making a profit but personally paying out of pocket for the privilege of assembling North Coast modules, and that's only legal at all because I'm the owner of the company and the only employee. All in all, maybe it'd really be more responsible for you to stop encouraging me in this madness and go buy from the Chinese factories, who at least do pay their workers.
In summary, in this part of the "green modular" series I've gone through environmental issues related to running a modular business, beyond just the impacts of the modules themselves. In earlier parts, I've talked about the energy efficiency of powering a module; the major toxic metals forbidden by RoHS; other metals of interest; and wood and toxic waste. Many of the issues are complicated and that's probably one of the most important larger-scale lessons here: there are tradeoffs and very few simple, easy fixes. But it remains that with some care, electronics in general and modular in particular can be built and used in a responsible way.
◀ PREV Green modular, part 4: Wood, and toxic waste || Building a telephone ring booster NEXT ▶
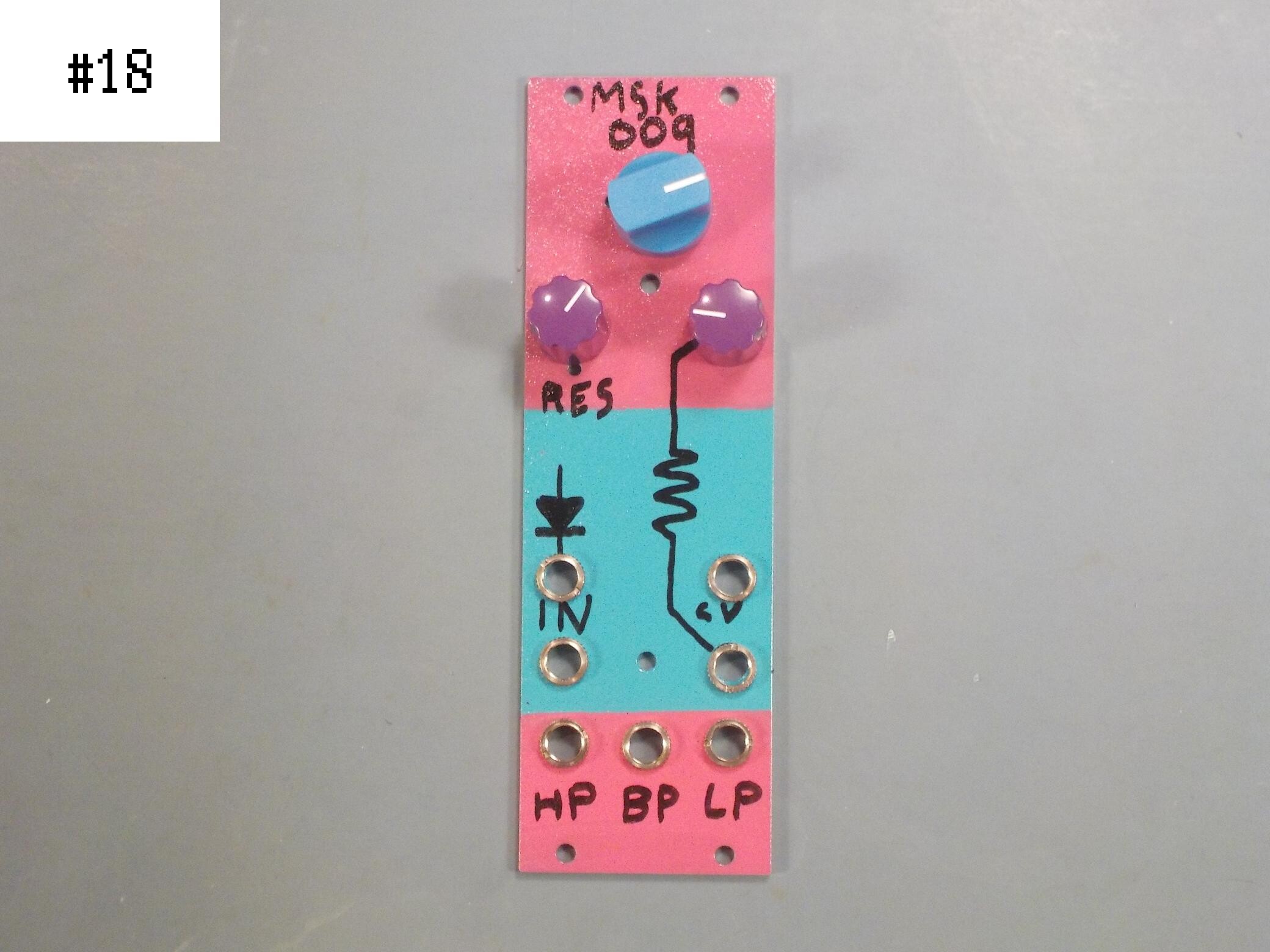