Homemade traditional resin flux
2019-05-26 SDIY chemistry science!
For most of the history of electronics, rosin has been the main ingredient in electronic solder flux. Anybody who learned electronics Back In The Day™ will be familiar with the piney smell of solder smoke. In this second article of the series on flux, we'll look at how to make your own traditional rosin or resin flux. For some background on the chemistry and physics of how flux works, see Part 1: "What is flux?"
Resin and rosin
The most important question, obviously, is what's the difference between "resin" and "rosin." Resin with an "e" is a general term for almost any kind of gooey solid or semi-solid substance. It's often used to describe synthetic plastics, especially in their raw form ("nylon resin," "Bakelite resin," and so on). A gooey substance that oozes out of trees and solidifies is also "resin" - often more specifically referred to as "oleoresin" in botany.
Rosin with an "o," on the other hand, is an industrial product made from the oleoresin of pine trees in particular. The traditional way of producing turpentine is to cut into live trees so that their sap oozes out, collect the sap (which is called "crude turpentine"), and distill it. The liquid that distills over is "spirit of turpentine" (the most familiar form of turpentine to us today, traditionally used as a paint solvent) and the glop left in the stillpot, which will harden into a glassy solid, is "rosin" - which is a kind of resin.
Cutting pine trees and distilling the sap for turpentine was formerly a huge industry, especially in some parts of the USA where there are or were pine forests and slave labour; but it's no longer a really big thing largely because real turpentine is not at all popular anymore. Other products are better (more effective, less toxic) and cheaper in most of the applications formerly served by turpentine. The sustainability of large-scale turpentine production is questionable too, because it does eventually kill the trees and the old-timey traditional industry made no provisions for replanting them. Nowadays, it's possible to extract nearly identical substances (which have come to be called "turpentine" and "rosin" even though they are not produced in the same way) as byproducts of paper-making and similar industries, and so a lot of the turpentine and rosin on the market is from byproduct sources.
Rosin is basically a waste product from the industries that produce it, which are more focused on the volatile turpentine, but rosin has many specialist uses mostly related to its stickiness. Bows for instruments like fiddles are usually rubbed with rosin to provide the necessary friction against the strings. Rubbing rosin on your bow is called rosining the bow, and there's a traditional Irish song (YouTube link) about the death of a fiddle player named "Rosin the Bow" as a pun on that. (I've seen the title of this song distorted into "Rosin the Beau," etc., by people who evidently didn't know what it meant.) Baseball players, and occasionally athletes in other sports, rub rosin on their hands for a better grip on bats, balls, and other equipment. Rosin is even used as a cooking medium for traditional Southern "rosin potatoes" (another YouTube link). And it's a common ingredient for solder flux.
What makes rosin so special as a solder flux ingredient is that it combines, in a single substance that is basically naturally-occurring, the main properties a flux needs to have. Referring back to the functions of flux ingredients described in my earlier article, rosin is both a resin and an organic acid. It consists mostly of abietic acid, and the rest is mostly other organic acids with very similar properties. This is basically a large, bulky hydrocarbon molecule. Being a bulky hydrocarbon gives it the desired physical properties of being solid at room temperature, forming a glassy inert film instead of crystals, and melting into a high-boiling liquid when it's heated up during soldering. But abietic acid also has an organic acid functional group attached, which allows it to become chemically active and react with metal surfaces when hot, as well as making the molecule polar enough that it can be put into solution with alcohol or some other relatively gentle solvent for application to the solder joint.
Although it works well, rosin is not the last word in solder fluxes. As a natural product, its composition and quality can be variable. It's a contact allergen and produces toxic smoke, both of which create safety issues for workers using it. It requires the use of organic solvents both to dissolve it in flux formulations and to remove the residue after soldering. And by itself it may not be sufficiently "active" to make solder wet the joint, especially not with the newer lead-free solder alloys and delicate surface-mount soldering processes, where a very active flux is needed. So, very much of the rosin flux used today is "activated" by adding other, stronger, acids to augment the abietic acid of the rosin itself.
Collecting and purifying pine resin
Please note that it's easy to just buy industrially-produced rosin. If you do that, you can skip all the steps in this section, go down to the "Formulating the flux" section, and make your flux with the purchased rosin directly. That may really be a better idea.
For my own experiments, I wanted to go all the way with collecting resin from real-life pine trees myself, but doing that made the project a lot more complicated, time consuming, and expensive, and it's not necessary if you just want to mix up some homemade flux. If you want to experiment with purifying pine resin but you can't easily collect it from the trees yourself, you can probably also buy that; Etsy seems to be a good source, with sellers there mostly catering to the crowd that want to use raw pine resin as an ingredient in homemade incense.
Pine trees grow in many parts of the world and there are a lot of them in the parks around Toronto, where I live. Especially right now as the weather is getting warmer, but to some extent all year round, pine trees will ooze sap which drips down their bark and hardens into globs.
This sap or oleoresin oozes out anywhere the tree has been injured, such as from a branch cut or fallen, often for years afterward. Pines will ooze a little bit of resin in hot weather without any obvious injury, and even the dead stump where a pine tree has been cut down will often produce beads of resin. You shouldn't hurt a tree just for this project, and removing resin directly from where it covers a fresh wound is probably not a good idea because this dried resin is part of how the tree defends itself from insects and disease. But there should be no harm in picking off some of the globs where they have run down the trunk below an older wound.
It occurs to me that some readers may not know what a pine tree looks like. I'm not sure I can give a definitive spotter's guide here (try searching the Web or looking at the picture above), but in general the easiest sign to look for is the leaves. Pines are evergreen trees with needle leaves, and in comparison to other needle-leaved evergreens, pines usually have noticeably longer needles with very sharp points. The needles grow in little bundles instead of one at a time, with the number of needles per bundle (two, three, maybe five) being one of the ways to recognize different species of pine trees. They grow in different sizes depending on the species, from small shrubs on up. I think of them as being trees that grow in dry, sunny locations, but especially in parks where they were planted by humans, that may vary a bit. And other evergreen trees have significantly less tendency to ooze resin.
I spent a Saturday morning walking around my local parks and gathering bits of pine resin, and I was able to collect about 13g of sticky globules, which was far more than I needed. The advantage to having more is that it's easier to work with and makes the small amount of preservative needed, proportionally larger and easier to measure; in fact just one or two grams of resin would probably be enough to make a small batch of solder flux for testing.
Be aware that there may sometimes be things on pine trees that look a little like resin globs, but are not. While I was collecting mine, I found some spiders' nests and Silly String, and neither of those would be welcome additions to a flux formulation. Plenty of people saw me and nobody seemed to object when I removed a few little bits of resin from trees in public parks, but obviously you should also exercise some discretion about interfering with trees that might be on private land, or doing anything that might attract the wrong kind of attention to yourself. If you get in trouble for trespassing or any other reason, then I didn't tell you to do whatever you were doing!
Raw resin picked right off the trees contains a fair bit of contamination - insects, dirt, particles of detached bark, and so on. I purified mine by dissolving it in a 3:1 mixture of acetone and isopropyl alcohol, as demonstrated in the video further down in this posting, but if I were doing it over I'd make a few changes to the procedure and so I'll describe what I now think is the best method rather than exactly the one I used.
My decision to use 3:1 acetone:alcohol came from a bunch of calculations I did with Hansen Solubility Parameters to come up with something that would dissolve the resin as effectively as possible. The very best (that is, most effective) solvents for pine resin, limiting it to things I could actually buy as a private individual without needing to go to specialist chemical suppliers, would be mixtures including things like xylene and toluene. But those are too toxic and flammable for me to be comfortable working with them, especially given that they dissolve most kinds of rubber gloves (pine resin is so much like rubber glove material that anything which dissolves it well, will also dissolve gloves) and I'm thinking not only of my own safety but also that of anyone who might try to follow my instructions and do it themselves. Isopropyl alcohol is reasonably non-toxic and often used in electronics anyway; acetone is possibly even less toxic than isopropyl alcohol (depending on whether we're talking about inhalation, ingestion, or skin contact), and both acetone and isopropyl alcohol are routinely used in applications that involve contact with people's bare skin (nail polish remover and massage respectively).
The problem I had was that when I tried to evaporate off the solvents, the acetone came off relatively fast but then it took longer than I liked for the last vestiges of the alcohol to evaporate. And neat acetone is already such a good solvent for pine resin that adding some alcohol to get the theoretically best dissolving power, probably makes no practical difference anyway. We don't really need to get fancy. One other little detail - which I kick myself for not thinking of in advance - was that the raw resin probably contained some water and I could have removed that with anhydrous magnesium sulfate, which I happen to have on hand for a different experiment anyway. So my new recommended procedure is to use neat acetone, with drying agent if available.
So: collect your raw resin into a suitable container. Note it had better be a container capable of resisting acetone, and many plastics will not. Add a scoop of anhydrous magnesium sulfate if you have it. Here's a YouTube video by NileRed about how to make anhydrous magnesium sulfate at home from Epsom salt. Note you must slow-roast it as described if you're starting with Epsom salt. Using ordinary hydrated Epsom salt without making it anhydrous first would only bring even more water into the mixture and be counterproductive. But if you don't have anhydrous magnesium sulfate, just leave it out; I did not use it myself even though I had some, just because I didn't think of it in time.
Be aware that acetone is volatile, meaning it produces a lot of vapour, and the vapour is both toxic and flammable. You must do these steps in a very well-ventilated place, away from sources of ignition. Using gloves or other personal protective equipment is your decision. Bearing in mind that acetone is routinely applied to people's skin, and very few gloves can resist it in any meaningful way anyway, I worked without gloves; this describes my own practice rather than any specific recommendation for others.
With appropriate safety measures in place, add acetone, about five or six millilitres per gram of raw resin, and mix well. It will probably take a few minutes of stirring (with an implement that will not dissolve in acetone; I used a wooden popsicle stick) to get the resin to dissolve. Even if it dissolves faster, if you are using magnesium sulfate to dry the solvent then you should let it sit a few minutes after stirring for the drying agent (which will not dissolve) to absorb the water, before giving it a final stir.
Get another container to filter the purified resin into, and if possible, weigh it accurately, empty, and record the weight - this will make it easier for you to know how much resin you actually have after the purification is finished. You will need a funnel that does not dissolve in acetone (that is, not plastic). I made a disposable one out of aluminum foil by forming it around a plastic funnel to get the shape. A metal or glass funnel would be fine, but they may not be easy to find and are hard to clean afterward; being able to just throw out my sticky foil funnel was kind of nice. Put a paper coffee filter in the funnel, and pour the dissolved resin through the filter into the receiving container. It should be a yellowish to brown liquid, and may be a little cloudy (with particulates that made it through the filter) but should not be fully opaque.
Then leave the container somewhere well-ventilated where it will not be knocked over by animals or become a hazard to inquisitive people, for 24 to 36 hours until all the acetone evaporates away. Ideally, it should become a glassy solid, but mine ended up as a very thick gooey brown liquid when I ran out of patience after six days of evaporation. At that point it was only losing a few milligrams of weight per day, and it no longer smelled like solvent, so I think it was unlikely to really dry any further no matter how long I might wait.
Weigh it after evaporation and subtract the weight of the empty container to determine how much purified resin you have. From about 13 grams of raw resin I was left with 11.07g purified, which was more than I was expecting. Maybe my raw resin was more pure than I thought, but I suspect some of that weight was actually residual solvent (water or isopropyl alcohol).
The purified resin can be used instead of rosin in the flux formulation below. If you're careful in planning how you use your glassware, it should be possible to mix the flux up in the same container into which you filtered the resin, without needing to scrape out the sticky resin and transfer to a new container.
Formulating the flux
Here's my suggested formulation for a homemade version of traditional pine soldering flux. Percentages are by weight.
- Commercially-available rosin, or pine resin purified by the procedure above: 30%
- Potassium sorbate: 0.2%
- Tap water: enough to dissolve the potassium sorbate (should be less than 1%)
- Isopropyl alcohol: to make 100% total
Mix the potassium sorbate with just enough water to get it to dissolve, then combine with the rest of the ingredients. The theory here is similar to how a bartender makes a traditional Old Fashioned: just enough soda to dissolve the sugar cube before adding the alcohol, which doesn't dissolve sugar (or potassium sorbate) very well if applied directly.
Here's a video of me making this flux, including purification from resin I collected myself.
This flux may be applied wherever you'd normally use solder flux. It should be compatible with both lead and lead-free electronic solder alloys. After soldering, the residue should be cleaned off with any common organic-solvent flux cleaner, such as isopropyl or ethyl alcohols, and a brush. It should be washed from skin with isopropyl or ethyl alcohols. Water will not remove it. This is not meant to be a no-clean flux. If left in place without cleaning, it's unlikely to cause any serious damage, but it may attract water, be a path for leakage currents, and so on. At the very least, it will probably remain sticky more or less forever. It is irritating on extended skin contact, you shouldn't breathe the smoke, and persons who are allergic to other rosin fluxes will probably also be allergic to this one. In general, it's similar to other traditional rosin fluxes.
My finished batch is a thin, cloudy, yellowish liquid. I think the cloudiness is from particles that made it through the coffee filter. It could also possibly be something in the raw resin that dissolved in the 3:1 acetone:alcohol purification solvent and can't dissolve in neat alcohol, and that's supported by the observation that the finished flux is more cloudy than the filtrate was. I suppose potassium sorbate coming out of solution is another possibility, though I don't think that's likely because it didn't happen in my earlier experiments trying to dissolve potassium sorbate in isopropyl alcohol. Anyway, I plan to just give the flux a quick swirl to make sure it's fully mixed, when I apply it.
The cheapest convenient source for rosin is probably the rosin blocks sold to stringed-instrument players in music stores; for a few dollars, one of those will provide enough rosin for several large batches of flux. Cut shavings from the block with a sharp knife. Another possibility is to buy a "rosin bag" as used by baseball players, from a sporting goods supplier; these are little cloth bags full of rosin in chunk or powder form. Rosin is also sold as a pure product for use in "beeswax wraps" (which are apparently some kind of hipster substitute for plastic food bags, or something - almost every page about them on the net is written assuming the reader already knows what they are) and a number of other miscellaneous purposes. If you want to purify your own resin instead of using rosin, see the earlier comments on that.
Potassium sorbate is included as a preservative. It's probably less necessary (you could leave it out, and the associated water, making the flux just simply rosin dissolved in alcohol) if you're using commercial rosin; I included it in my formulation because I think there may be enough sugars and so forth in the natural resin, for mould growth to be a potential issue. The easiest way to obtain potassium sorbate is probably from a supplier of home brewing ingredients, because it's used as a fermentation stopper in wine making. It's also a common general food preservative. I ordered mine online from Canadian Home Brew Supplies, which was also my source for some other equipment and ingredients used in the flux formulations I will post in later articles.
If you have access to sorbic acid (also a food preservative, but harder to find) it may be a better choice than potassium sorbate for this particular formulation because sorbic acid should dissolve directly in the alcohol solvent without needing water, and (as an unsalted organic acid) it may function as an activator too. However, sorbic acid won't work in my other formulations, which require water solubility, and I could only find it being sold for use in cosmetics with larger quantities and higher prices than I wanted to pay when I'd be using just a tiny amount in this one experiment. I actually considered trying to refine my own sorbic acid from unripe rowan berries (Sorbus sp., the original natural source for which this acid is named) but decided that would be too complicated.
Note that sorbate and sorbic acid should not be confused with ascorbate and ascorbic acid, which are forms of vitamin C, and not recommended for use in this project; they would not have the desired effect.
The isopropyl alcohol in this formulation (and my others) ought to be 99% pure. Even though we're adding a small amount of water to it, which may take the percentage down just a little, starting with the common 91% (or, worse, 70%) means it'll take longer to evaporate and may not perform as well for dissolving the rosin or resin.
This is not listed in the formulation but if I wanted to experiment with making this flux more active, I would try adding between one and three percent citric acid. That's a cheap and easy-to-obtain activator also used in my other formulations, and it should have no trouble dissolving in the alcohol solvent at that concentration. I haven't tried adding activator to this resin flux, however.
Preparing this flux requires having a reasonably accurate scale. I bought one designed for weighing hops in beer-making, from Canadian Home Brew Supplies, but I wasn't thrilled with it. It only went down to 0.1g precision and the "auto-zero" feature, which could not be turned off, meant it could not track gradual increases in weight such as from adding solvent drop by drop. I ended up getting another digital scale which is the one you can see in my video. That one is "Insten" brand, of cheap Chinese manufacture, and with shipping it came to Ca$17.98 from Walmart online. It weighs at 0.01g accuracy (on small weights; less accurate for weights over 100g), and for the money the Insten scale is surprisingly good. My biggest gripe is simply that because it's so small, it can be tricky to weigh anything bigger than about a 100ml beaker on this scale.
So in summary, I've described pine rosin and resin and their use in flux. I've gone through the procedure I followed, and the changes I would recommend, for collecting and purifying natural pine resin. And I've described how to formulate a homemade flux from that purified resin or commercially-available rosin. I have not yet attempted to use this flux, because I want to make a couple of other kinds and do a comparison; but that will follow. My hope is that interested hobbyists will be able to experiment with this themselves from my description, and will comment about their own experiences with it. Making your own flux is probably not a substitute for just buying ready-made commercial flux, but it's fun and possibly educational.
◀ PREV What is flux? || Make your own water-wash flux NEXT ▶
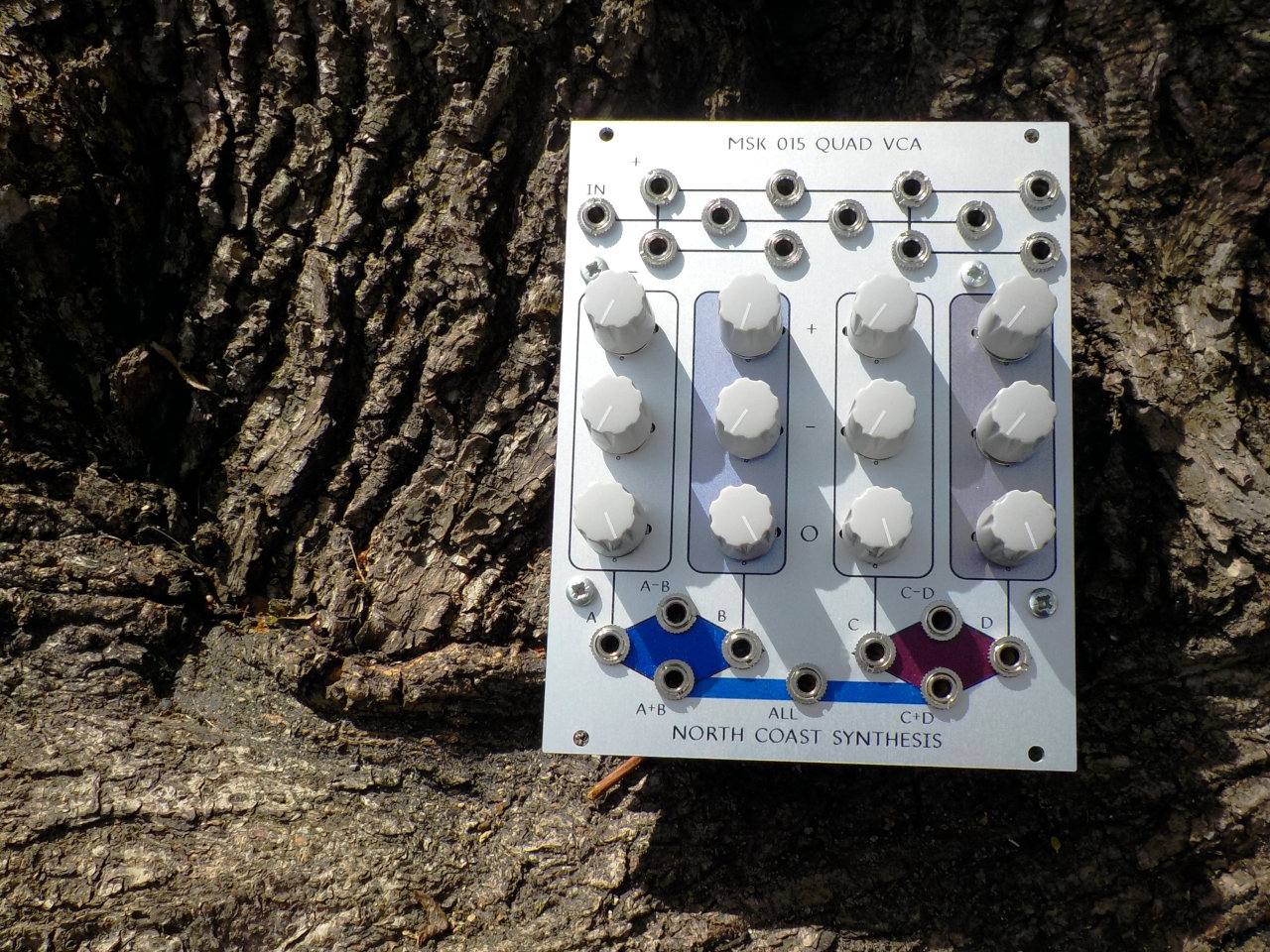