What is flux?
2019-05-24 SDIY chemistry science!
The details of soldering are always popular discussion topics in synth DIY fora: what kind of soldering iron should I use for building something like a Coiler VCF kit? What temperature? What kind of solder? And that last topic, in practice, is often really a discussion of what flux to use, because flux is usually built into the solder and the differences among fluxes are often the most important differences among solder products. There's been a lot written on recommendations for what kind of flux to use in different SDIY applications, but in this entry I'm going to take a different perspective on flux: the chemistry and physics of the flux itself. What is this stuff that we use every day, and how does it work? In planned future entries, I'll go through flux formulations you can make at home, videos of my own experiments with homemade flux, and so on.
Here are quick links to the other articles in the series:
- Homemade traditional resin flux
- Make your own water-wash flux
- DIY no-clean-style flux
- Testing homemade fluxes
The idea here isn't so much that making your own flux is really a practical exercise. Limitations of a home lab, minimum order quantities for chemicals, and so on mean that for any practical hobby electronics it makes more sense to just buy solder with built-in commercial flux. But I've found the project of learning how to make my own solder flux to be fun and educational, and I hope you will, too.
Water is wet
The basic problem flux solves is that of getting liquid solder to stick to the joint. Solder, under the conditions where it's applied, is a liquid. As human beings we're mostly familiar with water and water-based liquids, and the thing about water is that water is wet. That's such a familiar and commonplace statement that most people don't even have a clear idea of what the words mean. Water being "wet" means that water sticks to, and spreads out across, most surfaces. It soaks right into porous surfaces.
Liquid solder is not particularly wet, because it's a liquid metal and liquid metals in general are not wet. Solder doesn't stick to and soak into things the way water does. We are long past the era during which children had the opportunity to play with liquid mercury, but if you have ever dealt with that stuff, you may recognize the behaviour of solder: solder behaves like mercury, because this is the typical behaviour of liquid metals. On most surfaces, solder just forms little balls that roll around without sticking. So one of the main problems in soldering is to make the solder stick to the surface, and that's where flux comes in.
Exactly how it works depends on the flux formulation. There are several different mechanisms by which flux can operate, and most fluxes use more than one of them. Flux is usually something that will form a thin wet liquid at soldering temperatures - it may be solid, a thin wet liquid, or a thick, gooey liquid when it's applied at lower temperatures. Its first job is to flow over and wet the joint.
Solder likes to stick to hot clean metal. Having the liquid flux between the soldering iron (or other heat source, like the bath in wave soldering) and the joint helps heat the joint by thermal conduction; the liquid flux is a much better conductor than air or whatever random contamination might be on the surface. Flux may also serve to help clean the joint just by the mechanical action of its flowing onto the joint. Some fluxes are designed to boil, or decompose, producing gas bubbles which can dislodge dirt.
Depending on the surface metal of the joint (which is often tin or tin alloy, plated over a copper base) there may tend to be an oxide layer which inhibits solder from sticking, so flux may react with or dissolve the oxide, exposing the plain metal underneath. The layer of liquid flux over the surface also keeps out air, preventing the surface from immediately re-oxidizing. These effects make the surface more attractive to the liquid solder.
Even on surfaces that do not corrode as such, such as the gold plating of the circuit boards I include in North Coast Synthesis module kits, the surfaces in their natural state after manufacturing may not be as solder-attractive as they could be. Many fluxes, especially the more "active" ones, include acids or other chemicals that become active at high temperatures and etch the joint surface (or modify the surface of the liquid solder ball itself), making these surfaces rougher on a microscopic scale by exposing the crystal structure. Acids in flux can also react with and destroy organic contamination such as oils that may be on the joint.
Although it's not a good idea to do this deliberately, if you've ever sucked on a lemon or consumed some other high-acid food and then noticed that your teeth feel rough afterward, it's a similar effect: etching a surface leaves it rougher, with more friction and more ability to be wetted by liquids. Exactly the citric acid found in lemons is in fact a common ingredient for water-based fluxes. At the very high level, it's meant to do the same thing to the joint during soldering that it can do to your teeth.
After the flux has prepared the surfaces, its surface tension and that of the liquid solder combine to draw the solder into the joint. Then after the solder joint is formed and has cooled down, the job of the flux may not be finished. Almost any flux will leave some kind of residue. Depending on the formulation and the soldering process, that residue might be cleaned off (in which case it has to be something that will dissolve in the cleaning solvent, whether it is water or something else) or the residue might be left in place permanently (in which case it had better not be something that will cause corrosion, but there's the possibility that it may help protect the joint from other issues). One major practical distinction among fluxes is according to whether the residue is meant to be cleaned off, and if so with what (organic-solvent flux remover, or water). Some fluxes are called "no-clean" and meant to be safely usable without cleaning afterward.
I should mention that here I'm discussing flux for wetting surfaces during low-temperature soldering, such as is used in electronics, plumbing, and so on. The word "flux" in this sense basically just means "chemicals added when melting metal." In processes other than soldering, there are other fluxes used for very different purposes. For instance, in fire assaying for precious metals, the assay flux might include borax (which helps the tiny particles of liquid metal gather into a single bead) and litharge (which creates liquid lead that in turn acts as a solvent for small amounts of precious metals). These other fluxes are very interesting, but beyond the scope of my articles. There are some Cody's Lab videos about fire assaying, using its associated flux. Someone calling themselves "The Gayest Person On YouTube" has a series of videos featuring calcium fluoride flux for slowing down thermite reactions. Dwarf Fortress players will also know all about the (basically realistic) importance of flux in making iron and steel.
But what's in it?
Bearing in mind that soldering as a process has existed for many centuries, I think the first soldering fluxes were probably just naturally-occurring resins - sap out of trees, especially pine trees, eventually refined in some way. The physical and chemical principles by which these substances operate would not have been well-understood at first. It makes intuitive sense that if you want your solder to be sticky, you smear the joint with something sticky; and then trial and error would quickly lead people to pine sap as a sticky substance that seems to work well. Scientific study of such things in the last few centuries has led us to a better understanding of why pine sap works well as a flux, and to the development of synthetic fluxes.
A quick spin through the patent database shows that there's a wide variety of different ingredients used or proposed as things that could be in flux, but the major ones fall into a few simple categories.
Resins: gooey solids or liquids at room temperature that melt into thin high-boiling liquids and serve the mechanical purposes I described above. Note that "resin" with an "e" is a general term for substances in this category; the most popular one for solder flux is "rosin" with an "o," a purified form of the sap from pine trees. One example of a synthetic resin that sometimes replaces pine rosin would be polyethylene glycol (PEG). After soldering, resins leave a plastic-like film which might be intended for easy removal or to be left in place, protecting the joint.
Activators: ingredients that react chemically with the surface or with contaminants to boost wetting. These might include inorganic acids like hydrochloric or phosphoric acids (very effective, but not often seen in electronics because they're usually considered too corrosive); organic acids like citric acid or succinic acid, or the abietic acid found in rosin and shown by my molecular model above (organic acids tend to be much more active when hot than when cold); amines like triisopropanolamine (nitrogen componds which have a similar effect to organic acids); and a few others that do not fit into those categories. It is often possible for a single activator to combine more than one function. For instance, modern water-based fluxes often contain amino acids like glycine and alanine, which include both organic acid and amine functional groups in the same molecule.
Solvents: allow solid ingredients to be applied in liquid form, and bulk up the formulation to make it more convenient to apply things like activators in the necessary small quantities. Water and isopropyl alcohol are the most common solvents in flux formulations, but others are possible. In addition to being able to dissolve all the flux ingredients, it's important that the solvent should be something that will not damage the work (for instance, not dissolve plastic parts on a circuit board); evaporate at the desired rate; not be too toxic or flammable; and so on.
Surfactants: in general these are things that make liquids more wet. A big part of the point of flux itself is that it's a high-temperature surfactant for liquid solder; but the flux as a liquid at room temperature also needs to wet the surfaces, and (especially if water-based) it may contain detergents or other low-temperature surfactants that help it spread by reducing its surface tension.
Other ingredients: depending on how a given flux is designed, it may contain other things for a number of different purposes. For instance, in all my DIY formulations to be described in future entries here, I'm specifying potassium sorbate as a preservative to help keep organic substances from growing mould; citric acid in one formulation even though it's not the main activator, to act as a chelating agent that mitigates the effects of using tap instead of distilled water; and glycerol in another to thicken the liquid at low temperatures and help it stay on the joints.
Quite often a single ingredient will serve more than one of these purposes. For instance, pine rosin consists mostly of abietic acid and other closely related organic acids, and it serves as both a resin and its own activator - although modern fluxes based on rosin usually also include other activators too. If you're interested in the ingredients of a specific commercial flux, you can often dig around on the manufacturer's Web site and find legally-required safety data sheets which list the ingredients (though usually not their exact proportions, which are considered trade secrets).
So I've summarized what flux is for, how it works, and the kinds of ingredients that go into it. In future articles of this series, I'll go through actually making flux with ingredients available to home hobbyists, with comments on how to obtain the ingredients and videos of my own experiments. Then I'll go on to test my DIY fluxes, comparing them against each other and the commercial flux I normally use. In my next article: a traditional flux made from natural pine resin.
◀ PREV Driving LEDs digitally || Homemade traditional resin flux NEXT ▶
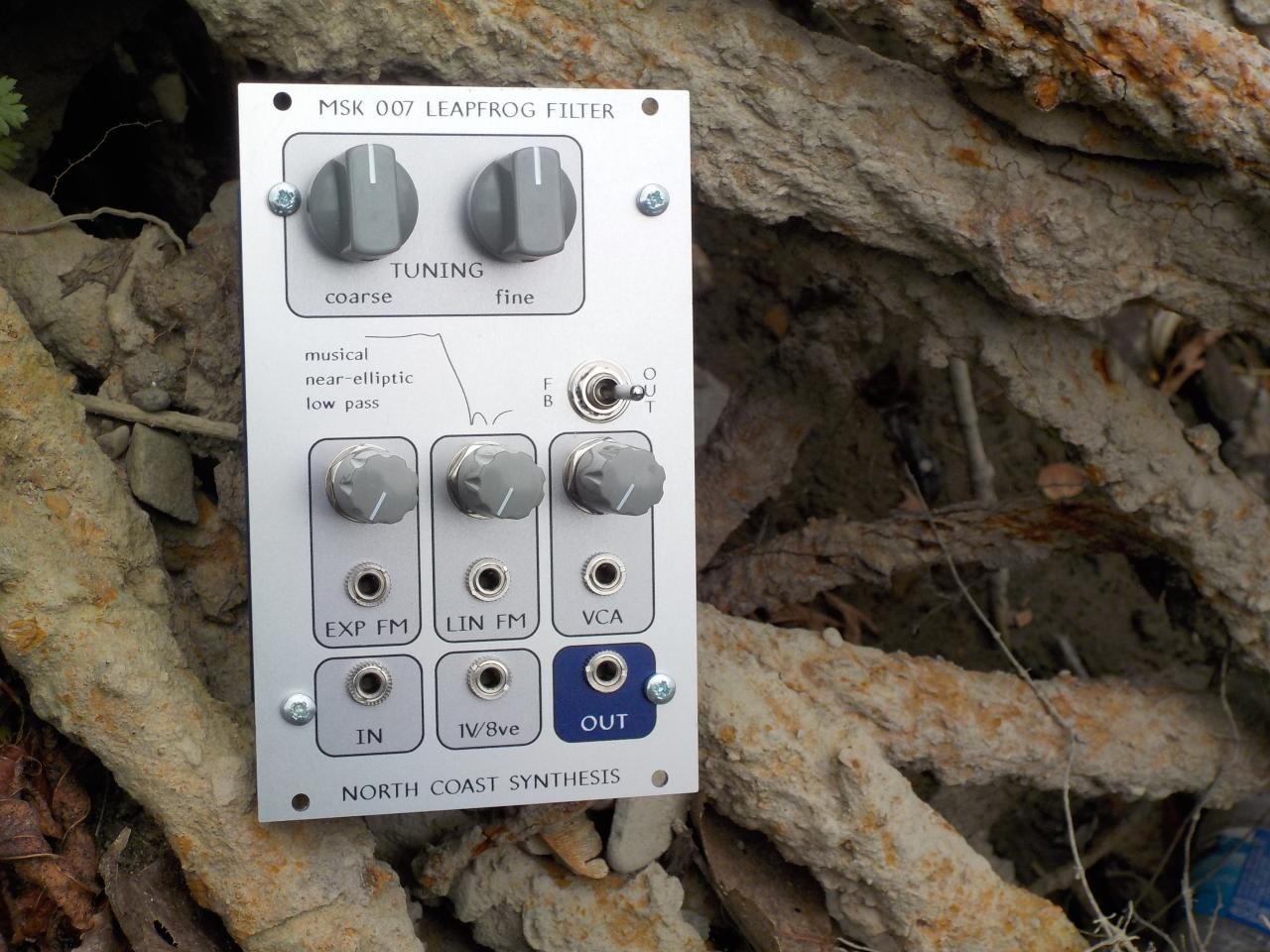