Power cycling and extra switches
2022-10-19 electronics environment power
As human beings we're quite familiar with the idea of things wearing out with use. If you hang a piece of clothing up in a closet and seldom wear it, then unless something happens like moths eating it, you can take it out years later and it'll still be good - whereas if you're wearing it every single day and washing it frequently, it may show visible damage and no longer be as good after just a few weeks. Many things in our world are like that, and we naturally expect electronic equipment to be included. Many synth users have, consciously or unconsciously, the idea that for each module there's an hour meter ticking away somewhere, like a car's odometer, measuring the time until the module will die or need servicing, in terms of the number of hours power is applied.
If we believe the module's life is being consumed whenever it's turned on, then it makes sense to try to get the most out of this limited resource by not having it turned on unnecessarily. So there's a recurring pattern of threads on synth fora: how can I turn off unused modules? Why don't modules have individual power switches? What about a power system with per-row power switches? Is it safe to leave my rack plugged in overnight? "List of modules with individual power switches 2022." And so on. The idea of turning modules off except during the moments you are directly using them, to conserve their limited hours of useful life, makes sense if you think that they are wearing out all the time they are powered up. But electricity doesn't really work like that.
Module lifespan
Module lifespans aren't measured in hours. They are basically measured in power-ups.
I described mechanical friction in an earlier article. Things literally wear out because of friction and similar effects: moving parts slide against each other, causing microscopic damage, tiny bits break off, and over time it adds up to the parts no longer being their original shapes. Moving parts get looser, or in rare cases tighter. Materials move and change, like liquids evaporating and metals oxidizing. Lint fibres come out every time you wash your clothes, leaving fewer fibres to actually be the clothes. But electricity flowing through wires and components does not normally have any such effects. In a powered-on module without someone's hand wiggling the knobs or patching and unpatching the cables, there is nothing physical moving except electrons, which have effectively no mass or momentum. The electrons disturb nothing except each other. If the module is being overheated, okay, that can be damaging through mechanisms like speeding capacitor aging - but it would be true regardless of whether the module was turned on and overheated, or overheated while turned off. There just isn't a physical basis for modules to wear out solely from being powered up. There is no hour meter ticking away. The main reason put forward for frequently turning modules on and off, of conserving their limited operating hours, is a non-issue.
But isn't it at least harmless? If someone wants to frequently turn modules on and off, shouldn't they be able to do so? What about secondary reasons, like saving power to reduce environmental impact? In fact, there are some important reasons not to frequently turn modules on and off, and why having extra power switches may be a bad idea.
Electronic equipment does produce heat while operating, so when you turn it on, it warms up, and when you turn it off, it cools down. If it's reasonably well-designed and operated in an appropriate environment, then these temperature fluctuations won't be large, but they will be more than zero. A basic physical effect is that almost all materials expand a little when heated and contract when cooled; and this expansion and contraction is different for different materials. So there is some mechanical movement and resulting stress - things changing shape just a little and getting looser or tighter, and different materials straining against each other because of their different expansion - every time you flip the switch. Over time those small movements do add up to create mechanical wear, as friction does. If you turn something on and off ten times in a day, you're putting much more wear on it and its lifetime will expire sooner than if you turned it on once in the morning, left it on for the whole day despite only really using it 10% of the time, and then turned it off. To the extent that there's a lifetime meter ticking over in the background, it is doing something more like counting number of times you turned the machine on, than like number of hours.
I'm not sure I even want to mention "tin whiskers," which are a tin can of worms and a non-issue in almost all real-life situations, but if you are a person who wants to worry about tin whiskers, it's also a fact that temperature cycling is an important part of the process that would create tin whiskers. You basically get no tin whiskers in real life anyway, but you also get fewer with a module that goes through fewer power cycles.
There are other effects that exacerbate the harm from turning things on and off too often, beyond thermal cycling. When equipment is first powered up, it inevitably goes through a sort of intermediate state of being partially powered up for what might be a few milliseconds as the filter capacitors charge, the voltage regulators settle on their correct output voltages, and so on. During that time the circuit is not really operating in its normal specified conditions. To the very small extent that electricity can cause any "wear" on or damage to equipment, much of it happens in the very brief power-up interval. If you remember incandescent lamps, there's an analogy: you may remember that when a light bulb burns out it's usually at the moment you switch it on. Similarly, as ads for motor oil remind us, much of the wear on a mechanical engine happens while starting it up; most of the protective oil is in the pan instead of the bearings then, and that's the time at which high-quality oil, with more ability to maintain a film in the bearings, is claimed to be most beneficial.
Some very few modules containing specialized and mostly-obsolete components - such as vacuum-tube amplifiers, and older EL backlit displays - may really have an hours-of-operation limit inherent to the technology and likely to bite faster than more ordinary lifespan-limiting effects. These components are not common today. And, of course, if you really do have an overheating problem in your rack as a whole, then the rack is more likely to overheat when it's turned on, or when more things are turned on, than when everything is turned off. I'm more interested in the idea of whether it's a good idea to power-cycle a rack, or parts of a rack, in more normal operating conditions.
I plan to write in a future article of this series about start-up current surges associated with capacitors charging up, and about the issue of patching signals from powered-up modules into powered-down modules. Obviously, the less often you switch your modules on and off, the fewer chances there are for surges to happen. Many modules, including North Coast's, are only officially rated for signals described as "between the power rails," because that is a specification of the ICs inside the modules. If the module is powered down, then the power rails are all at zero, and any signal from a powered-up external source is technically outside the power rails and you're depending on whatever protections against misuse may be built into the chips or the surrounding circuits. If two modules are on the same power switch, you never have to worry about their being in different power states.
I don't want to overstate the wear that might be caused by power-cycling, because it really is likely to be very small. In practice your modules are likely to wear out for other reasons (like mechanical friction from twisting knobs and plugging in cables) long before you'd notice any problems caused by power-cycling. If you add an extra power switch and flip the switch way too often, you'll probably wear out the switch itself before it seriously affects the lifespan of any module it's controlling. You shouldn't go to lengths to keep equipment turned on for multi-week periods of disuse just to reduce power-cycling. But you also shouldn't convince yourself to do many extra power cycles per day, and demand module or rack features to support that, on the mistaken belief modules will last longer if kept turned off. Really, your modules will last longest if switched infrequently, whether they sit on or off while unused, and they'll probably last a very long time regardless.
Saving electricity: money, environmental impact, and milliamp count
A secondary reason sometimes put forward for frequent power-switching has to do with saving electricity. We're all conscious of wanting to save the environment; unnecessary energy use has a cost in both money and environmental impact; and independently of the cost of the electricity, modular users are concerned about the limited number of milliamps available from their power supplies and whether the modules will add up to more than the power supply can support. Estimated milliamp counts (whether accurate or not!) are a big part of what keeps ModularGrid in business.
Now, first of all, if your power supply cannot power up all your modules at once, then you are in a bad situation. You really don't want to be switching off one module just so you have enough power to switch on another one in the same system. Remembering which combinations of modules (or rows, or other switchable things) are and are not usable within the power limit will be difficult, and will limit your patching possibilities. Some day, you're certainly going to flip too many switches on, and the power supply will be overloaded. In the best case, then it automatically shuts itself off. Next best case, it provides a reduced voltage; then you hope that your modules (now being operated outside their specifications) will not be damaged. Probably, they won't be damaged, because they'll be designed to withstand low-voltage conditions during startup anyway, but it's a technical violation of the rules and even if undamaged, they may not work under such conditions. Worst case, overloading the power supply damages something, most likely the power supply itself. None of these outcomes is good. Really: you ought to have a power supply capable of powering all the modules attached to it, so you won't be forced to pick and choose moment-by-moment.
That's not an issue for most users. Most people who want local switches for just parts of the rack do have enough power available for the whole works, but want to reduce consumption of it by powering up less than everything, most of the time. Unnecessary energy consumption costs money and has an environmental impact. Here we have to think about scale, and energy consumption entailed elsewhere.
A large module might consume 100mA of Eurorack power; that could typically mean 100mA on each of the ±12V rails, a total of 2.4W of power delivered to the module. A typical Eurorack power supply in real life, operated well below its maximum load because you're trying to keep parts of the rack turned off, might operate a little below 50% efficiency measured from the mains outlet, so the module ends up consuming slightly more than twice as much, that is about 5W, as measured at the point the power supply plugs into the wall. A "linear" power supply would be worse, consuming more wall power to deliver the same amount to the module. Switching power supplies used for computers advertise much better percentage efficiencies, but are operated, and especially are tested, under more favourable conditions than typically apply to a modular synthesizer in real life. So, it's reasonable to say 5W per module. Multiply that by let's say ten for a row full of modules: 1000mA load as Eurorack users count it, and 50W of power consumed by a row or saved by turning off a per-row switch. I'm saying "per row" to make the switch look as good as possible; of course a per-module switch would be much less valuable for saving power because it controls a smaller amount of power.
How much is it worth to save 50W? For comparison, an air conditioner or small electric heater might consume 2000W. A non-electric heater consumes a similar amount of energy in some other form. A mid-size personal computer might consume 500W - higher at the peaks of intense gaming, but lower on average over time. If you use one extra minute of heating or cooling, then you need to keep the synth row switched off 40 extra minutes to provide an equivalent saving. That's true both of the money to buy the energy, and of the environmental impact associated with generating and spending the energy; and it's ignoring other effects, assuming there is no other cost associated with installing and using the extra power switch.
People are inclined to think of energy savings in terms of how many switches they flip off, but it really matters what's connected to those switches, and having extra switches doesn't help much if they are on the wrong things. If you can make even a small reduction in your use of heating and cooling in particular, it blows the savings from reduced synthesizer use, and most other household electricity consumption, right out of the picture. Everything except heating and cooling counts for comparatively little.
The cost of the switch itself
It does cost something to buy and install an extra switch. A decent power switch as a component, in manufacturing quantities, might cost $2. A lower-quality one with a lower price tag would not really be cheaper because it would wear out too soon. Electricity prices are highly variable with time and place in 2022, but it would be reasonable to estimate that power might cost $0.20 per kWh. Swapping some other currency (perhaps £ or €) or arguing about whether I mean Canadian, US, or some other dollars, doesn't make much difference at this level of estimation; they are all close enough. At those prices, the switch costs as much as 10kWh of electricity.
But that's the price of just buying the switch. The retail price of having a power system with the row switch built into it is going to be about five times as much, thus $10 and 50kWh - see EEVblog's YouTube video on the economics of selling hardware for more about that point. The retail price includes not only the BOM cost of $2 for the switch, but also the labour to build it into the equipment, testing and so on, and the retail markup. If the switch saves 50W, then to save 50kWh, it needs to save 1kh - one "kilohour" or one thousand hours of operation - to pay for itself.
I did that calculation in terms of money because money is relatively easy to measure, but the cost in energy and other resources to manufacture, install, test, package, and sell the switch itself, will be proportional to its price tag too. It's reasonable to say that in the best case you might use a switch to switch off a rack row, when it wouldn't otherwise be switched off, for at most about three hours per day, and then you have to do that every single day for about a year just to pay off the money and environmental costs of having the switch, before there'll be a real net saving from using it. Ten years if it was a per-module instead of per-row switch.
Then, of course, if the extra power cycles actually did reduce module lifespan, we'd also have to consider the money and environmental costs of needing to replace the modules sooner.
◀ PREV Module wear and aging || All about levels NEXT ▶
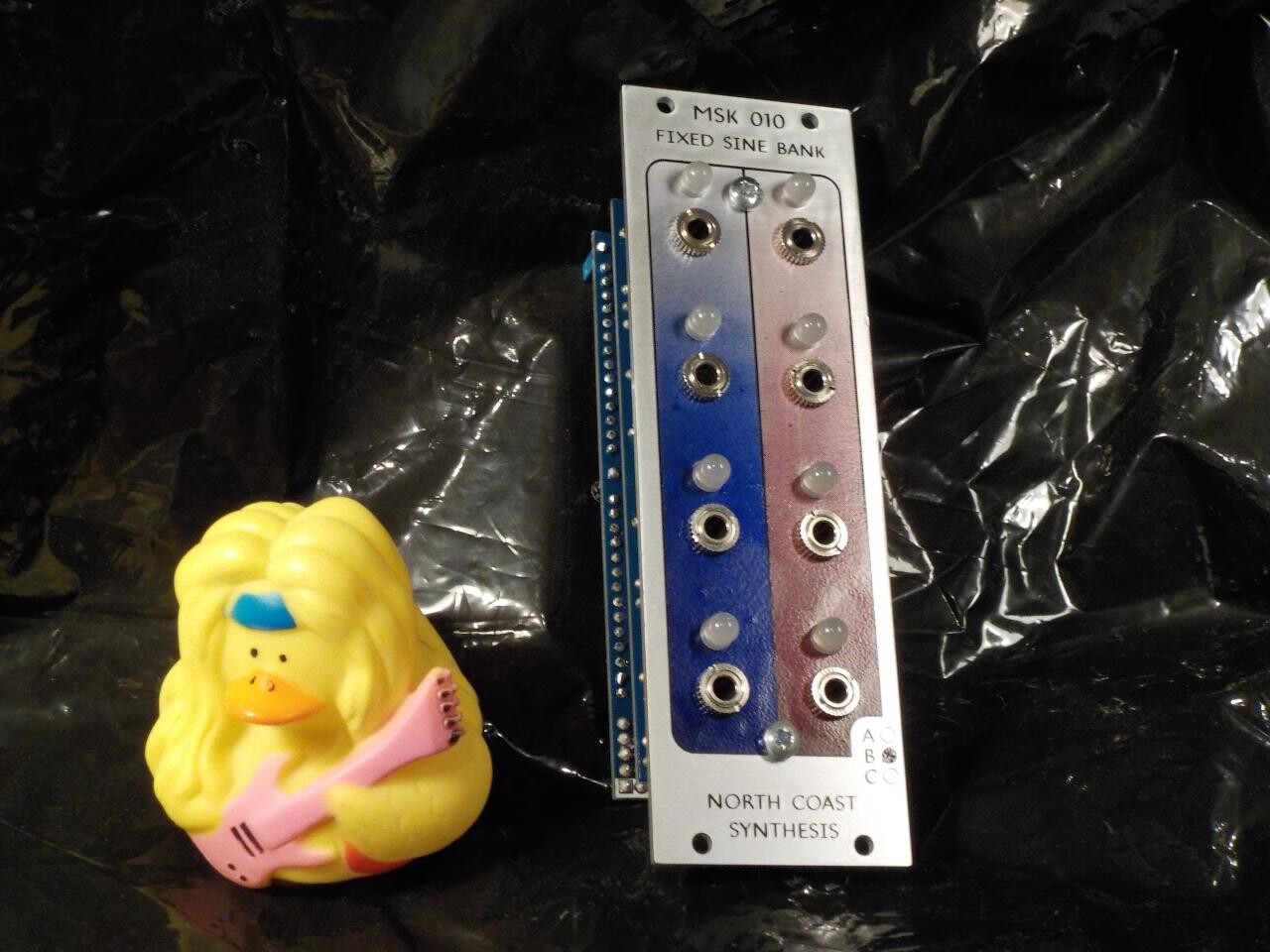