Eurorack is not a synthesizer format
2025-03-27 eurorack power design
Despite my having been involved in Eurorack for a number of years, there are still some important points that mystify me about the system and the community. Often I look at forum threads in which Eurorack users are looking for specific modules or features and I wonder, why would anyone want that? I recently figured out something I think sheds light on the situation: Eurorack is not actually a synthesizer format!
Let's unpack that a bit. For years I have wondered:
- Why do people think they want "stereo filters" in Eurorack? It makes no sense to have a "stereo filter" in a patch that's doing analog synthesis as such. The place where you'd want your signal to be stereo is far downstream from where you'd want to filter it. And yet this is a common request. The closest thing I've ever gotten to a straight answer, when I've tried to engage in discussion over it, comes down to "I actually want a parametric equalizer and I think a 'filter' is what that's called." But that raises some further questions.
- Why do people think they want mixing boards, especially "stereo" mixing boards, in Eurorack? The power and physical form-factor limits mean one of those can't be as good as a basic standalone mixer, and the structure of the market means it will cost much more in Eurorack format than standalone. Does the guitarist, in a band or even solo, also operate the mixing board while performing? Does the drummer? Why would a synth player expect to? It's hard to imagine what possible advantage there could be to having this function "in the rack" that would outweigh these points, and yet it's a common request, so there must be some perceived advantage.
- Why the constant emphasis on modules being "small," to the point that they are literally unusable? Why not just get a rack big enough to hold all the modules you want to put in it? I once thought that this was a simple expectation for "small" modules to also be cheap, because everyone obviously wants to save money, but the preference for small size seems to be so strong that users will sometimes pay extra for it.
- Why are there requests for individual modules to be controlled by MIDI instead of by control voltages? Doesn't that defeat the point of the format? Wouldn't a separate MIDI-to-CV interface be preferable?
- Why are there surprisingly frequent requests for signal connectors on the backs of modules? How does one imagine being able to actually use those?
- Why are power bricks anathema, and why is fine-grained power switching (such as per-module or per-row) requested and seen as useful?
- Why does every Eurorack newbie buy an unnecessary "output module"? (I did, myself.)
- Why all the emphasis on absolutely minimizing noise? We don't just get requests for a "low-noise" whatever module; the request is always for the lowest noise whatever module. Nobody seems to treat this as a priority in the same way with other electric and electronic instruments. Guitarists in particular seem willing to tolerate a lot of hum and similar issues just to get the main sound the way they want it, in a way that Eurorack users would consider unacceptable.
- Why do these same issues not come up in other modular synthesizer formats?
The thing is, where I'm coming from that leads me to ask the above questions is my basic assumption that Eurorack is a modular synthesizer format. I used Csound for a long time before I was in a position to get a hardware modular synth. I listened to a lot of music from people who unquestionably used modular synthesizers, and analog synthesizers more generally, as musical instruments. It's understandable I would think Eurorack was a modular syntheizer format, and I'd assume that other users of Eurorack also thought of it as modular synthesizer format. Web sites that introduce Eurorack usually say, as Wikipedia does, that "Eurorack is a modular synthesizer format."
But I think there's a better way to understand it, that better explains the behaviour and desires of Eurorack users at the present time. Accept this proposition and the things I find confusing, become much less confusing.
For many Eurorack users, as of the mid-2020s, Eurorack's real purpose is to be a miniature substitute for 19" studio racks.
More or less the rack standard we know today, with front panels 19" (482.6mm) wide, a multiple of 1U (1.75" or 44.45mm) high, and specific arrangments of holes for mounting and so on, originated with AT&T in the early 1920s - that is, just over a century ago. It hasn't much changed since. Electronic audio and video studios, and computer server installations, have used standard 19" racks throughout their history. It has been a standard assumption for a long time that if you want to buy electronic equipment of any kind that will be for professional use, installed more or less permanently and wired up to other electronic equipment in a large installation, then you're going to be getting it in a 19" rack format. That's just how electronic equipment is built.
But in the 21st Century, electronic equipment is smaller and cheaper now than it used to be. And in the world of modular synthesizers in particular, we have a lot of non-professional users who want to use, and can afford to buy, what would formerly have been professional-level equipment. It doesn't make sense to these users that building a studio should require the physical space and associated cost and weight of installing full-size racks.
If Eurorack isn't really a framework for building synthesizers in particular, but rather for putting together studio audio equipment in general (and having the result be physically small, even portable), then maybe users don't see themselves as instrumentalists. Maybe they see themselves more as producers, or possibly DJs.
From the point of view of a tool for producers, not instrumentalists, we can tick off each item on the list. Emphasis on "stereo" is frankly absurd from the point of view of an instrument as such, but it makes sense that finished tracks are likely to be stereo and the user is building a finished track, so they think they need stereo. Users want mixing boards because they think they are producers, and mixing boards are what producers use. It's important for modules to be "small" because that's not a side issue, it's the whole point of Eurorack. Eurorack is the miniature studio rack. Users want MIDI control because the idea of voltage control, and the history of other modular synthesizers using voltage control and the reasons they do, are not front and centre; the users just want something that is compatible with other generic studio equipment and that's more likely to be MIDI than voltage. Studio rack equipment has connectors on the back, and a hard-wired but configurable default signal flow implemented through those connectors, so of course a miniature studio rack ought to have that capability as well. And so on.
It's easier to be charitable about Eurorack users who ask for bizarre features that clash with the format, once one understands that they are coming from a different world, a world in which those things are considered normal.
Eurorack is a poor substitute for 19"
As someone who designs and sells Eurorack products, it'd be really nice if I could give users what they want. Unfortunately, there are a number of reasons why Eurorack can't actually be the miniature studio rack format users want it to be. I can't sell my customers what they really want, nor talk them into wanting something else that would be easier for me to sell them. The format itself creates these issues. Attempting to solve them would mean going so far outside the definition of Eurorack that it wouldn't really be right to call the product that resulted a "Eurorack" product. Many of the most fundamental technical issues come from the Eurorack power specification - a thing that can't really be changed without breaking compatibility.
Headroom: On ±12V power, analog electronics start having trouble once signals get outside about ±8V. Native Eurorack signal sources often generate ±5V, which doesn't leave much margin, and there are interfacing issues if you want to take input from something with wider dynamic range. It isn't realistic to expect ±10V input and output on ±12V power, but some users ask for that. Compare to 19", in which each piece of equipment steps down mains AC power as needed, typically to ±15V, and the usual signal voltages are much lower, leaving more headroom.
Power distribution: Eurorack power is distributed at a low voltage, the same low voltage actually used by the modules. Final regulation is not usually done per-module, and can't easily be. That makes the resistance of wiring inside the rack significant in setting up crosstalk between modules. It becomes more noticeable in larger installations and when processing multiple independent signals. Compare to 19", in which (again) power is distributed at the relatively high AC line voltage and regulated per-device, so the resistance of longer-distance power wiring is not so important.
Unbalanced signalling: Over the short distances signals must travel inside a single piece of equipment, it usually makes sense to transmit one-sided voltages relative to a common zero. Eurorack is designed on the assumption modules are parts of a single piece of equipment, and that works if it's true. But once the system becomes larger than one "instrument," it's a problem to use unbalanced signalling. You get interference and crosstalk. Compare to 19" rack, where balanced signalling on XLR connectors is common between modules.
Ground reference shared with power return: There is only one 0V rail on the Eurorack bus, and it serves two purposes. It is the reference for unbalanced signalling, and also the power return for any imbalance between the +12V and -12V rails. Combining the reference with a power voltage is a recipe for crosstalk, beyond just the issues that come from unbalanced signalling and low-voltage power distribution already. Studio rack equipment, if it uses unbalanced signalling, usually separates the reference voltage from the 0V power return. Eurorack designers today cannot meaningfully make such a distinction; even with the best possible separation inside each module, having only one 0V connection back to the bus board spoils it.
Limited standardization of power requirements: Do you have a +5V rail in your case or not? How many milliamps on each rail? Do you believe that your 1000mA power supply is really capable of 1000mA, or do you follow the standard advice in Eurorack of not loading it to more than 80% of its specification? Compare to the situation with studio racks, where because of the higher voltage and consequent lower current going into the modules, you seldom need to think about whether you have enough power, at all - and when power does become an issue, it's simpler to understand, and you're allowed to expect that the equipment can actually do what it's specified to do.
Small row height: In a 3U row there is only about 110mm of space available between the rails. That narrowly constrains the way panels can be laid out. In particular, the customary layout of a studio mixer, with vertical "channel strips" and sliders, is impossible to achieve in Eurorack. Everybody seems to want one of those anyway but I have yet to see a credible design concept for what the panel would actually look like. People with eyes smaller than their fingers draw mock-up sketches of mixer panels in 3U that they would never be able to really use. Compare to 19" racks, where the vertical dimension is unconstrained, and the limit on the horizontal dimension is wider than almost anything you'd want to put in the rack; there is much more flexibility there for any piece of equipment that needs a lot of front-panel space in a specific layout.
Limited physical standardization: We don't really know how deep, behind the panel, Eurorack modules are allowed to be. This particular issue also exists for 19" racks, which have no standardized depth either, but those are under less pressure to be small and so it's less often a serious limitation. There actually is a standard for what colour the front panels are supposed to be in Eurorack, but many of us want it to be something else, and think that's really important. Horizontal-width standardization, or the lack thereof, raises issues too - with the annoyance of odd-HP modules, out-of-phase Analog Systems panels, and users attempting with sliding-nut rails to defeat the thermal expansion/dimensional tolerance gap between modules. Although there are some standardization problems with respect to screw threads, I've never seen people try to make exceptions to the vertical grid in a 19" rack, and there's more general agreement that functionality is what matters, and on how to ensure functionality.
Locking in a patch: Users want to maintain a standardized patch for an extended period of time, even transporting the rack between uses of the same patch. The mini-jack connectors used for Eurorack are not good for that. Compare to the locking XLR connectors often used on 19" rack gear. Users ask for connectors on the backs of modules, to change the normalling. That is not realistically possible in Eurorack physical design, and it would multiply the loose-cable problem. Compare to 19", which is where the idea came from.
Standard Eurorack connector, signal, and control formats are wrong for desired applications: Apart from the balanced/unbalanced issue already mentioned, users want "stereo" signals in the rack. Eurorack works at a lower level than that - you can have as many channels as you want, but they are separate signals. That causes constant confusion and a mismatch between modules that exist, and user desires. Users also want to control multiple notes at once on a single cable. Control voltages don't really do that, so people want to use MIDI instead, but that's not Eurorack, and the connectors for it don't work well in Eurorack physical design, and so there are further compromises like poorly-standardized "TRS MIDI" and "sync bus" and so on. And there are constant interfacing issues between Eurorack and computerized DAWs, Eurorack and effect pedals, Eurorack and studio electronics in general, and so on. Some of these issues exist in 19" rack too, but with more physical space available there and no inappropriate original standard from which it'll be necessary to make exceptions, the problems are reduced.
Random impedance: Some Eurorack outputs are designed to be plugged output-to-output for mixing, while others will be overloaded, produce distortion, and possibly even be damaged when you do that; some are designed to produce precise voltages, but only into an open circuit, while others have a built-in assumption of driving a specific impedance, which may or may not turn out to be true; input impedance may vary from module to module or with knob position and it's unclear whether that is or isn't a problem; the typical impedance of inputs is high enough to create real thermal noise issues, while that of outputs is low enough to create power issues; every designer is forced to compromise on these points in order to make their modules work acceptably with others, and they still are not always sucessful; nobody is clear on what should be done; I've been attacked for making commonplace and true statements about what in practice is done; and so on.
Eurorack power connectors are physically capable of being plugged in backwards, modules can be destroyed when you do that, some cables are built to do it automatically by mistake, and the sins of the late Wowa Cwejman are well known: no comment should be necessary here.
I have spent years shouting at my customers about how they ought to want something other than what they think they want, and it's clear that's not going to work. Eurorack users are going to continue asking for Eurorack to be a miniature substitute for 19" studio racks, and merely pointing out it can never be good at that, isn't going to resolve the issue. So what are we to do instead?
Concept: yet another new format
Very many of the reasons Eurorack doesn't work as a miniature studio/audio product format just come down to the power supply. If we could only fix the power supply, a Eurorack-like format could work a lot better in the "miniature studio rack" space. Here's what I would do with the power, at a minimum:
- Supply ±18V power to each module. This is a high enough voltage to allow for local per-module regulation down to a lower, cleaner voltage to be actually used in the electronics, with headroom over the signal level. It's also just unusual enough to cut down on attempts to repurpose inappropriate power supply hardware from other equipment.
- Separate 0V power return and 0V signal reference, and mandatory GFCI in the upstream power supply. That is "ground fault circuit interruption," like the safety feature on mains sockets in bathrooms and other wet locations. Given the low voltage involved, in this case it would be more an anti-dumbass feature than for safety as such. Try to return DC power through the signal reference and the rack cuts off your power. No more of clueless designers combining power and reference because they don't know better, nor of more clueful designers being forced to do the same because it's the only way to work within the format.
- Polarized connectors that can't be plugged in backwards, right from the start.
But making the minimum of necessary changes to the power supply alone, would already be enough that current Eurorack modules wouldn't work with the new system. That being the case, it makes sense to fix other problems too.
- Balanced signals. There is synergy between that and the power supply changes to reduce crosstalk and "bleed" - either change alone helps, but they're even better together.
- Standardized impedance, lower on the inputs and higher on the outputs than Eurorack. No intention that it should be possible to mix outputs by plugging them together (which is highly dubious with balanced signals anyway); you just need a mixer. Splitting should be possible, but exact voltages are not expected to be maintained if you do that.
- Pro or "prosumer" line level is standard; measured in dBu, not volts peak to peak. You need a preamp to interface to microphones or guitars, but no special formalities for most other studio equipment.
- Physical design based on nominal 75mm cubes (actually three inches, but we'll pretend "76.2mm" is a number with no history). A rack is one cube deep and however many cubes high and wide. Modules are one cube deep and a whole number of cubes high and wide. Want a big square panel for a mixer? You can have that with a big enough chassis.
- Modules plug into connectors in the back of the rack which provide power and normalled signal connections to nearby cubes, kind of like 500-series. You get a sensible patch by plugging in modules next to each other with no cables at all; then you can override it by having a separate patch bay module, or with a fancy smart rack that can rearrange the connections under software control. The front panels of the modules might have connectors for interfacing, or only controls, taking all their signal connections through the backplane. (I wrote "2 signals" per cube-to-cube path when making the sketch below, but on further thought, making it two in each direction would probably make most sense. We want to have a lot, even if it means many connector pins.)
- Fancier racks might have built-in patch bays and interfaces to make the backplane signal connections available conveniently, with or without patching via cables, on front or back. A basic rack would just offer power and let you use interface modules to get at the signals.
- A standardized digital network is available to modules through the backplane and this replaces the use of control voltages. At the margin, if you really want to convert between audio and control, then you can have an ADC/DAC module to do that; but that's not really what you'll want, because this isn't a synthesizer anymore, it's a modular miniature studio.
- Physical locking built into the rack holds modules in, and ejects them when desired, without requiring tools. Any fasteners used are captive and firmly standardized; no "is this an M3, M2.5, or US #4 screw?"; no sliding nut foolishness.
- I'm unsure what kind of connectors would be ideal for patching where modules have front-panel connectors at all (most wouldn't), but I lean toward 3.5mm TRS, balanced mono, despite that some people are going to be disappointed that these connections will not be compatible with the similar-looking 3.5mm TRS unbalanced stereo. You'll still need some kind of interface to connect to unbalanced systems, and you'll need to run two cables for "stereo." We can't have everything, having the signals between modules be balanced is important, and separate channels on separate cables is what real studio racks do, so it can't be a total disaster.
Concept: the Big Crunch portable studio
Another possibility would be to just give up on modularity. It's clear from their behaviour that many Eurorack users don't actually want their system to be modular as a high priority in itself, only as a means to an end. What they really want is a portable audio studio that can fit into an airliner's overhead baggage bin and plug into the mains without a separate box; modularity is only a means to that end because Eurorack is perceived as "small." So why not sell them exactly a portable audio studio that can fit into an airliner's overhead baggage bin and plug into the mains without a separate box?
- One box, the size of a small (airliner carry-on) suitcase.
- Protective lid also acts as a stand for the main unit.
- Hardware inside is an ARM PC running DAW software with several channels of audio interface and a small analog mixing board with a variety of connector formats for I/O.
- If you want to play it as a synthesizer, you can run software synthesis plugins.
- Touch screen, and connectors for attaching keyboard/mouse/monitor.
- Wireless networking.
- Built-in international mains power supply, takes a standard IEC cord. (Important to users not to have a separate brick.)
- Decent-sized battery for portable use; basically a laptop computer in a larger form factor with some audio hardware in the box.
- There could even be some space in the physical design for a small area to add one or two Eurorack modules, which might be a selling point for anyone who still wants that.
Many of the pieces for that are available as commercial off-the-shelf products already; but they need to all be in one box. The main hard part of the project would be getting the physical design exactly right, because it and the price tag would be the critical issues for marketing. Hitting a marketable price tag would go hand in hand with making a large enough number of units. A product like this couldn't possibly fly at the "one to ten units" level of some of my own products, nor even the "one hundred to one thousand units" level of the most successful Eurorack companies. As a rough guesstimate, I think the project would have to be planned around selling several thousand of them, in order to be able to offer it for say $2000. And that means it's a project in the single-digit millions of dollars, bigger than any company that I think would want to take it on.
With either of these concepts, the focus on power and especially the customer-dictated requirement to plug into mains power without a separate box, means that international regulatory issues would be significant. That's another barrier to entry. Eurorack companies are accustomed to building modules that plug into a rack and then they depend on regulatory exemptions from strict safety compliance requirements, because it's whoever builds the power supply, not whoever builds the modules, that is responsible for the safety rules. Even Eurorack companies that sell power supplies (and you may note I don't) usually buy ready-made products from others to do the actual power-supply task, with minimal adaptation to the Eurorack role, specifically to minimize their own regulatory obligations. That's why there are so many Eurorack products that use separate power bricks. Unfortunately, I don't think there's a way out of this: users really, really want products that will plug directly into the wall. The only way to do that is to suck up the extra expense of dealing with all the compliance requirements. And then the only way to pay for that is to work on a much larger scale (selling more units of every product, spreading the cost over a longer production run).
And with that in mind, to the inevitable question of whether either of these concepts will the next North Coast Synthesis Ltd. product, I have to answer, yes! Sure! Certainly! When I get 1,000 preorders at full price!
◀ PREV Where is that site? || North Coast Synthesis at Open Ears 2025 NEXT ▶
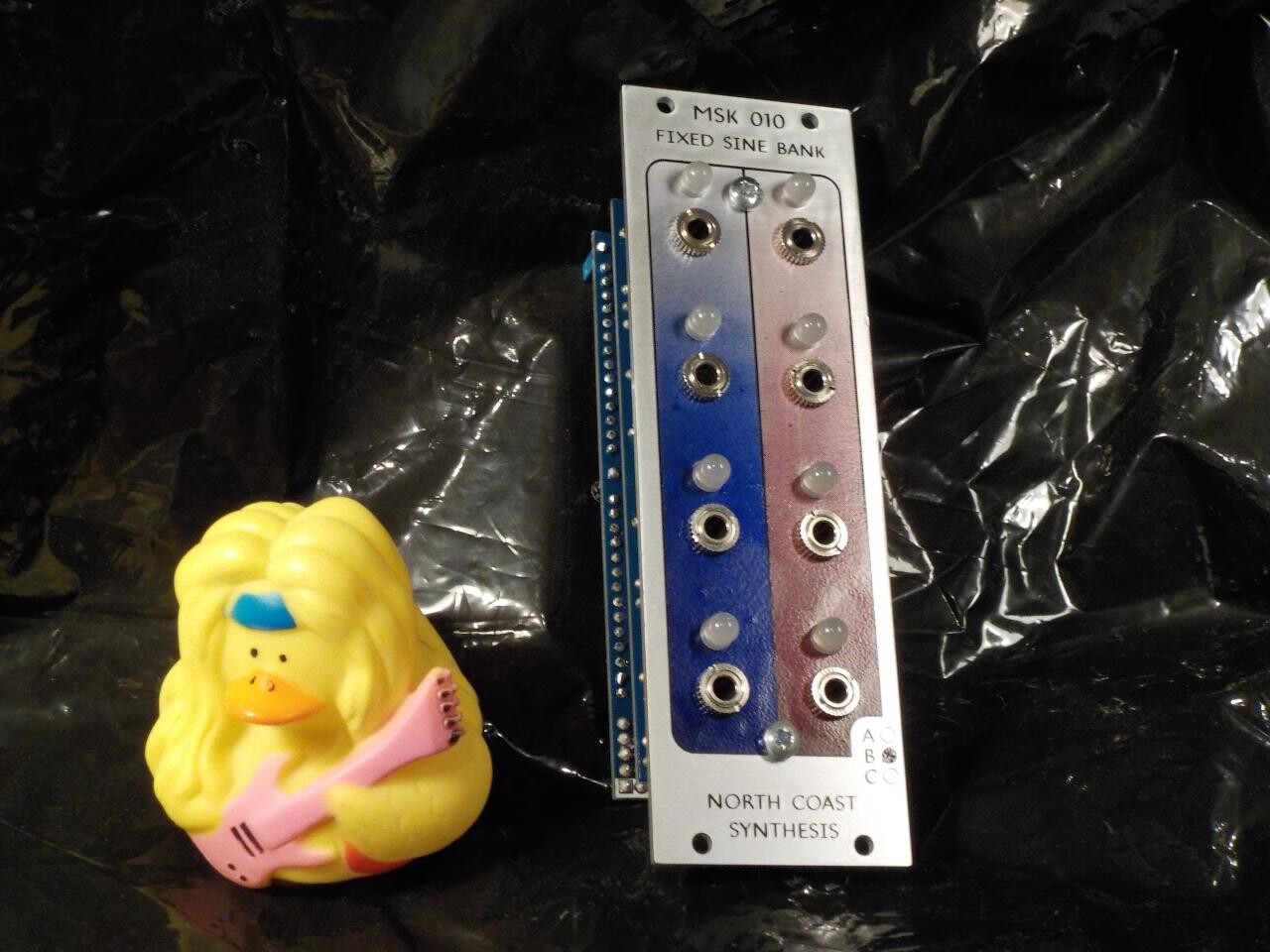
MSK 010 Fixed Sine Bank, variant A
US$200.20 including shipping
Comments
I dont know how serious the cubicle concept actually should be, so take this with a grain of salt. Don't overdo it! I imagine neighboring connectins to be a huge pain ** the *** mechanically and also for routing / module placement. Users should set this up once, so why not use e.g. keyed multi pin connectors and cable like 10pin IDC keylocked, D-sub (ok maybe not), ... Form a setup point, this is OK in Eurorack. Would preferre cables over rigid backplanes because of extra slack. even if more fiddly?
Modularity brings in interface issues, but I also enables rapid progress imho. See all these 3D printer guys. In particular, look at the Gridfinity format.
With a new format getting a bit established it maybe easier to combine enough functionality in modules to the last step for the Designer would be to merge your designed modules and the case and then strip off all extra interfacing, mouting, etc.
AS challenging as kickstarting a onefitsall product would be a new format. The initial offerings must be enough to be attractive for users. No one wants a half empty rack and wait for decades to get stuff thats needed. I dont know the industry, but maybe there are some manufacturers that can reach consensus on a "mini portable studio gear" (MPSG(tm)) format and bring together a useful set of functions / modules to the market? based on a fair distribution of who designs what for the common launch.
Reading this piece left me equal parts fascinated and frustrated.
Fascinated by the engineering insight. The proposed modular cube format is full of clever ideas, better power delivery, balanced signals, clean interconnects. There’s a lot to love there. But what frustrates me is the why. The entire argument hinges on a faulty diagnosis: that Eurorack’s problems stem from people trying to use it like a miniature 19” studio rack.
I think that’s exactly backwards.
Eurorack doesn’t “struggle” to be a studio rack. It was never trying to be one. Comparing it to a 19” format, then declaring it broken because it doesn’t behave like one, is like criticizing a violin for not being a saxophone. You’re looking at a vibrant, creative ecosystem through the wrong lens.
Users Aren’t Confused, They’re Evolving
There’s a repeated suggestion in the piece that Eurorack users don’t know what they actually want. That they ask for stereo filters when they “really” mean EQs, or mixing modules when they “should” be using external gear.
But this assumes there’s a single “correct” way to use modular synthesis. And that’s the core problem. Modern modular isn’t just monophonic subtractive voice chains. It’s complex generative systems. It’s interactive performance. It’s experimental signal processing. It’s stereo, and quad. It’s mixing as performance. It’s sequencing light, CV, and MIDI all at once. Are some uses technically inefficient? Sure. Are they less valid artistically? Absolutely not.
Stereo Isn’t a Studio Affectation
There’s also an odd resentment in the way stereo and mixing are discussed, as if they’re somehow impure, or incompatible with modular as an instrument. What, have you never seen a stereo delay hooked up to a guitar? Stereo isn’t just a “producer” thing. It’s a spatial thing. A movement thing. A texture thing.
When I’m performing live with a modular rig, I need stereo. I want localized spatial events, ping-pong delays, stereo reverbs, filter sweeps that pan. Saying that’s a “DAW mindset” or a misuse of the format implies a very narrow view of what performance is supposed to look like. If you don’t want stereo, that’s fine. But dismissing it as a symptom of user confusion is missing the point entirely.
Small Modules and Portability: It’s About Context
Yes, ultra-miniaturized modules can be difficult to use. We agree there. But the solution isn’t simply “get a bigger case and stay home.” For live performers, portability matters. Ergonomics matter. Tradeoffs happen. A few “set and forget” tiny modules in a compact skiff might make perfect sense in a real-world, real-stage, real-backpack scenario. The format gives us those choices. You may not like all of them. But they’re not mistakes, they’re decisions.
A New Format? Cool. But Don’t Burn Down the Old One.
Here’s the twist: I actually like your new format concept. A cube-based system with standardized power and signal? That could be amazing. There’s clearly room in the world for better electrical engineering in modular. And if someone wants to build a new prosumer modular audio platform, I’d cheer it on. But don’t build it on a rejection of what Eurorack has become. Don’t frame the community’s creativity as confusion. Don’t dismiss users for trying new things with old tools. Because the messy, inconsistent, gloriously hacked-together format of Eurorack? That is the instrument. That’s what makes it beautiful.
Want to fix the noise floor, sort out impedance, or invent a whole new box? Awesome. Let’s do it. But let’s not pretend Eurorack is broken because people are making art with it in ways you didn’t expect.
—Knobulism
On Aaron's comments:
There've been some efforts to push for different power cables in Eurorack, but I think as long as we routinely use unbalanced signalling between modules, referenced to a common "ground," we're not going to make much progress. We really need balanced interconnect, and that's not something that can be implemented without affecting the design of every module. It necessitates a new format.
In a new "miniature studio rack" format, yes, I think it is really necessary to have a fixed depth and a back panel on modules. I'd like modules to be fully enclosed on the sides, too. Modules are little boxes, more or less sealed, that fit into matching holes and can be put in and taken out by unskilled persons, ideally without tools. Compare to 500-series and 19" rack, neither of which usually have exposed circuit boards. The idea of Eurorack modules as being basically bare circuit boards with a front panel, comes from the Eurocard standard that inspired Doepfer (not designed to be interchangeable frequently or by unskilled persons) and the idea that you'd buy your synthesizer by telling Doepfer which modules you wanted, then the technician would assemble it for you, and then you'd have your synthesizer and would use it indefinitely. The idea of unskilled users swapping modules themselves, frequently, out in the field, was not part of the original Eurorack concept at all; but one of my points is that it *should* be part of the concept of a new format that could replace Eurorack as Eurorack is used today.
I think the connections to the backplane should be specified in a lot of detail - which pins connect in which direction to where, the protocol for communication on the digital control bus, and so on. The idea would be that it should be neither tempting nor possible for individual manufacturers to repurpose things, the way they've done for instance with Doepfer's CV bus; and conversely, there should be scope for "smart" backplanes to implement things like patch memory without needing any additional support in the modules or breaking the operation of more basic installations.
However, note that I don't see this system using analog CV. That's what the digital network is for. This does of course mean every module which accepts "control" needs to have digital components in it; but I think that's in line with manufacturing realities and market demand. Eurorack users are already eager to demand features that can only be done digitally, and are not eager to listen to the excuse that "we can't do that without adding a microcontroller."
I see the possibility of rotation as relevant primarily for modules that just provide connectors. At the end of a signal chain you want the signal to be available on the front panel (which, note well, is not the default). So you plug in an "XLR connector" module. And then, by plugging it in in the appropriate orientation, you can have it access the signal to the left, right, top, or bottom, depending on which way you are running your signal chain. It's only a small generalization of what 500-series already does. SCART is another possible reference point.
Having power on a separate connector from signals might make sense simply because of different physical requirements for power connections, but I don't think that makes a difference to it being "ground loop city." Sharing a ground reference between different pieces of equipment is always a problem, with or without a separate connector for it. Using balanced connections is the way to solve that; anything else, including a "star ground," is going to be a serious compromise. Note that Eurorack is already ground loop city, and can't not be, given the unbalanced connections among modules. My thought with the new-format proposal is to solve that problem in a more drastic way than just by attempting to have a "star ground."
The assumption that "users should set this up once" seems to have been part of the original Eurorack design (as I mentioned above in response to Aaron's thoughts), but I think it's solidly established that that's not really how people *do* use Eurorack as of 2025. It seems to be an important part of the use case now that users will be frequently pulling out modules and plugging in different ones. That's why stuff like the ribbon power cables, which may have been defensible when they were hidden behind the front panel and only ever touched by technicians, have subsequently become a problem. I'm not sure how "extra slack" is relevant; I don't see the finished assembly as a thing that would be physically flexible - it's a solid object. And note the experience in Eurorack with "flying bus" cables and the problems those can cause.
I don't really understand the comment about a capital-D Designer "stripping off extra interfacing"; are you envisioning this as becoming part of a larger product? Like, in a real professional-level studio where they hire someone to configure and install a whole permanent installation? That would be interesting, but my guess is that conventional 19" racks would be more appealing for someone doing that. I'm envisioning this concept as more for the people who are currently buying Eurorack and complaining about it.
On introduction of such a thing: I think the only way it could really work would be if a large company introduced it as a complete system, including a wide enough range of modules that someone could realistically build their miniature/portable studio out of just the modules available immediately at initial introduction. I don't know of any even moderately-successful modular-synth format, or (going further afield) any modular-equipment format, that was launched by a consortium of cooperating small companies. Herding cats, etc.
I'm glad you got something out of the article and gave it serious thought, but your perspective seems inside-out to me. I'm not saying Eurorack shouldn't be used creatively. Quite the contrary. I thought it was clear from the start that my whole perspective here is that I see Eurorack as a musical instrument. Yes, it's for making art. That is what I expect. It's not something I didn't expect and am objecting to.
However, it is quite simply not true that *everybody* seems Eurorack as a musical instrument. I don't know if you've spent much time on synth fora, but it's pretty clear from the practical traffic on those, the questions that actually get asked and answered, and my communications with my customers, that very many users of Eurorack today - so many that these users can be considered to be "the" typical users with classical synthesists a vanishingly small and shrinking minority - want to use Eurorack to build audio-processing machines that are simply not synthesizers, in the sense of the word "synthesizers" used by people like Moog back in the day. I think instead of calling them "synthesizers," "miniature studios" would be a good way of describing what the machines current Eurorack users want, actually are. Maybe some better, more descriptive term could be substituted for that.
I think it's important to stop objecting to the fact that users of Eurorack today want something other than the synthesizer format that Eurorack used to be. The user population and its needs have changed. We shouldn't blame the users for that, and we should think about how to give them what they actually want. That seems to be what you're saying, too, so I'm not sure why you think it's in opposition to my thoughts. Is it just because I started the article by describing in detail the confusion I felt when I first noticed, and had not yet processed, the way the world had changed?
The rear power connector issue is definitely a problem. I built myself a collection of DIY modules and instead used the 3-wire Molex MicroFit 3.0 connectors to distribute +/-12V + GND power. They're locking and idiot-proof keyed, both for the cable to jack and in mating the jack to the PCB. You can buy prefab cable assemblies or pre-crimped leads from digikey / mouser, and they're automotive-grade 18ga or 16ga wiring which minimizes the wiring resistance issue you mentioned. Amazingly, despite that chunkiness, the PCB footprint is slightly smaller than a shielded 10 pin IDC jack.
If you want to champion a new power cable, I'd advocate for those - or maybe use a 2x3 6-pin MicroFit which would have room for +5V, REF0V, and one left over for something else... I often locally generate a reference from a zener shunt rather than reference relative to a noisy +12V, so I think something like REF10V would also be a good choice, supplied from an LM4040. Or +3V3 power for LVTTL MCU use?
I think the biggest challenges I see with your "cube format" are related to the connector choice and layout situation, and I'm curious about your take on these:
1) As described (especially with the relative sizes shown), the cross-shaped rear interconnect you describe essentially requires the module to have a rear panel / faceplate, at the specified depth, essentially dedicated to interconnect and mounting. That seems like a bunch of expense and assembly complexity, vs a "ragged" rear side that simply must respect a max depth. Do you think it's all needed? Feasible? Vertically-mounted rectangular connectors on the left/right edges might squeeze into a standard module circuit board layout better, with standard front panel screw-based mounting, which eliminates the need for the rear panel and tight depth tolerance.
2) Would you devote some specific sections of a 2x24 pin (or whatever) rectangle to CV vs Audio, in vs out? Seems like a situation ripe for other mfrs to misinterpret / abuse and then it's just as much of a cluster**** as Euro. I'm also not sure how a module would think about how it interacts with its neighbors if it's supposed to be able to rotate?
3) The most "suggestion more than question" of these - I'd highly suggest a separate power connector, not part of the data plane, so you can keep to star grounding... Otherwise this seems like ground-loop city? I think you're a better EE than I am in general, so I feel like I must be missing something on this front :)