Green modular, part 1: Energy, carbon, and power supply regulators
2019-01-12 design environment electronics
I'm sometimes asked about the environmental consequences of modular synthesizers. It's an interesting question with a lot of ramifications, and there's a lot of misinformation circulated. That may be inevitable given the nature of this business: synthesizers combine engineering, where hard facts rule, with music, where subjective aesthetics are the order of the day, and it's very easy for someone to start from one bad guess or wrong idea and then follow it into constructing an entire unfounded theory. There's also an unfortunate overlap between the synthesizer hobby and the whole morass of audiophile woo.
This is the first part of a five-part series on modular and the environment. In this part, I'm going to look at energy consumption of synthesizers; especially, the electrical efficiency of the power supplies.
If we're going to be serious and put accurate values on the risks and returns, the most important environmental issue facing the world today is climate change caused by carbon dioxide pollution, and the key variable for that is energy consumption. Most sources of energy for technological use end up releasing carbon dioxide, either directly when they burn fuel or indirectly (as with nuclear power) in the work done to build the plants, maintain them, and clean up afterwards.
Electrical consumption
The energy and therefore pollution cost of a synthesizer module isn't only in the electricity to run it. There's significant energy spent to make the parts, to manufacture the module out of parts, to ship the materials and the parts and the module all over the world, and even to dispose of it when it eventually reaches the end of its lifespan. I'll cover some of those in future postings of this series. For this posting, my main interest is in the electricity consumed directly by the synthesizer in operation.
As a manufacturer of electronic modules, I can't control where you will get the electricity that you supply to my products when you use them, and where it comes from makes a difference. If your electricity comes from burning coal, it'll create much more pollution (mercury as well as CO2) than if it's solar. Battery power is probably worst of all. But from the module's point of view, all the electrons look exactly the same. There's also something critically important between the wall socket and the module: the power supply, which in fact is often a two-stage system consisting of a "wall wart" transformer and a regulator board mounted inside the rack. Each stage of the power system has to convert power from one form to another, and it will lose some. If your power system is more or less efficient, that will affect how much power you actually draw from the wall even if the module on the end doesn't change its power consumption.
Here's some good news: the amount of power involved in most synthesizers is arguably negligible. My most energy-consuming module, the MSK 007 Leapfrog VCF, is specified to consume (as a "maximum in ordinary operation") 70mA on the positive and 65mA on the negative 12V power bus. That works out to 1.62W in total - basically nothing, compared to other electrical devices. A common home LED light bulb might consume 14W, a incandescent bulb of the same brightness might be 100W, and an electric space heater could drain about a thousand times the Leapfrog's power consumption: 1620W. If you run an electric space heater, or an air conditioner, in your studio for a couple of minutes, then the power consumption of the synth module for the day basically comes for free; and heating with means other than electricity will usually entail burning fuel and releasing carbon dioxide directly. Heating and cooling dwarf the power consumption of a Leapfrog.
There is some possibility that very old synthesizer designs, or those attempting to imitate very old technology, may use significantly more power. In particular, if you have a circuit using vacuum tubes, which need their cathodes heated with filaments similar in nature to incandescent bulbs, then its power consumption may be greater. Newer solid-state and digital designs are often more economical of power. One or two tube modules probably still won't come to very many watts in total.
But when you start both hooking up dozens of modules of any kind and powering them through a power supply with an inefficient regulator, the total number of watts burned in the regulator may start to become significant enough to be worth thinking about at least a little, and thinking about this stuff from a circuits perspective is fun anyway, so let's do that.
Zener-diode regulators
The general outline of pretty much all electronic power supplies is that they start by putting the relatively high-voltage AC power from the wall socket through a transformer, which uses magnetic fields to trade off voltage against current, converting the high AC voltage to a lower AC voltage. People have been building transformers for well over a century and we've gotten quite good at it; this step usually runs at at least 95% efficiency, often considerably more.
The low-voltage AC goes through diodes (often four of them in a "bridge" configuration) which change it into pulsating DC; that is, a voltage that varies but only goes in one direction. Then a filter, usually consisting of just a big capacitor, smooths out the pulsations. For sensitive electronic circuits the resulting more or less dirty DC needs to be regulated to a constant voltage that will remain stable in the face of changing loads, and the regulator is probably the most interesting part of the power supply from an efficiency point of view.
Here's a sketch of an old-fashioned Zener shunt regulator. I don't think anybody actually uses this design for Eurorack power supplies, for reasons that will become clear; but something similar using a gas-filled vacuum tube was standard in the days when those were state of the art devices.
The Zener diode conducts as much current as necessary to prevent the voltage across it from exceeding some specified level, in this case assumed to be 12V. I'm feeding it from a 15V unregulated supply (the transformer/diodes/capacitor arrangement) through a 3Ω resistor, which has 3V across it (15V-12V) and therefore conducts 1A (1000mA) of current. With no load on the regulator, all that current goes through the Zener diode, so it had better be able to dissipate 12W of power, and it'll probably need to be attached to a heat sink and so forth; but such diodes are routinely manufactured, and were even easier to find Back In The Day when this kind of regulator was more popular.
If we connect a load to the power supply output at right, it will see 12V as it should, and whatever current it draws is simply subtracted from the Zener diode's share. As long as the load current stays between zero and 1000mA, the voltage will be kept quite stable. The Zener diode responds quickly to changes in load, and it's generally quite a well-behaved circuit. Zener diodes do produce some noise - they are sometimes used, as I discussed in a previous posting, as synthesizer noise sources. But if that's a concern, we could attach a capacitor or a more elaborate filter to the output to soak up some of the noise, and it'll still compare well to the other regulators discussed below.
So what's the problem?
Consider the following graph, which shows the input current in relation to the output current. Just for fun I've also plotted a line for the input current consumption if we increased the input voltage to 20V instead of 15V without changing the regulator design.
Input current doesn't change with output current! This regulator always draws the maximum possible input current, all the time. And because of the 3Ω input impedance, it also doesn't respond well to changes in the input voltage. Increasing the input voltage from 15V to 20V means more than doubling the current consumption and the power dissipation of the Zener diode itself, which could easily blow up if it wasn't specifically chosen to handle such a case. The resistor, too, needs to be designed to handle the maximum power it will see under any expected input and output conditions. Here's a plot of the percentage efficiency of the Zener regulator at different output currents, with 15V and 20V input.
Note that 80% efficiency means we must feed about 1.6W/0.80 = 2.0W of power into the regulator to supply a Leapfrog VCF; similarly, 20% efficiency requires 1.6W/0.20 = 8.0W of input power for the same module, four times as much. Percentage efficiency makes a real difference to overall consumption!
The Zener regulator only starts to have reasonable efficiency when it's near maximum load, and then only with 15V input. In any other cases, we are burning far too much power in either the Zener diode or the ballast resistor. Not shown on the graph is that if the load current goes over the design maximum (1000mA for 15V input), the resistor will drop too much voltage and the output voltage will droop, with the Zener never reaching its standard voltage at all. So to maintain a regulated output voltage we would have to balance out the desire to keep output current near maximum for efficiency, with having a safety margin against loss of regulation.
Note that (because the Zener burns all the power that the load doesn't) the Zener regulator is actually working less hard and is less likely to overheat or similar, when it is more heavily loaded within its design range. Higher load doesn't put more stress on it.
In fact this type of circuit still is used sometimes, but not for power supply regulation. For instance, I designed something like it with TL431 chips, which are functionally similar to Zener diodes, in the North Coast Octave Switch module. There it's not a voltage source but a voltage reference providing just a few milliamps at a stable voltage to set the input and output voltages of the quantizers. Having a simple circuit is of great benefit in such cases, and the efficiency is not important because of the extremely low power levels. But for supplying real amounts of power, the world has moved on to more sophisticated regulator circuits.
Linear regulators
A more sophisticated kind of regulator would replace the resistor with some kind of active element (often a "pass transistor" of some kind, whether bipolar or MOSFET) that will increase or decrease its resistance in order to soak up just the right amount of voltage at the instantaneous current level. That will require something to control it, but if done right it means there's no longer a need for a component like the Zener diode of the previous design to divert unused current. Here's a sketch of this kind of regulator, which is often called a "linear" regulator.
I have labelled the box on the diagram "7812," which is the part number of a popular building-block IC for this application, but real power supplies often use something a little more complicated to handle higher power levels or meet other needs, building up the regulator function out of multiple components instead of just using a single IC.
The nice thing about this kind of design in general is that it basically draws no more current from the input than it supplies to the output. There may be just a little current required to power the control system which adjusts the pass transistor's effective resistance; let's say 5mA bypassed into ground through the vertical wire on the diagram. That might be typical for a real 7812, which I think is specified to consume 6mA maximum as "quiescent current." But other than that, the regulator only drops as much voltage as it needs to, drawing the same current on the input as it supplies on the output, burning the power difference as heat. Here's a plot; the 5mA powering the regulator itself isn't even visible at this scale, and note that the lines for 15V and 20V input are right on top of each other.
Not drawing maximum current all the time means an important improvement in efficiency, because we're not burning extra power at low current levels. There is some drop-off in efficiency at the lowest output currents where the 5mA requirement becomes more significant in relation to the load's power consumption, but this design basically runs well at all but the lowest power levels. That makes it far preferable to the Zener regulator, which is only efficient near maximum load.
The maximum efficiency is better at 15V input than at 20V input, because it is limited by the voltage difference between input and output. With a higher input voltage, there is more that must be turned into heat and basically wasted in the regulator. We cannot take the input voltage much below 15V with a literal 7812 chip because it has a "drop-out voltage" of up to 2.5V, meaning that it is not capable of reliably dropping less; the minimum input voltage is then 14.5V. Other linear regulator designs can achieve lower drop-out voltages and potentially better efficiency, but there's a trade-off between pushing the drop-out voltage and accurate regulation, because the closer we bring the input to the regulator's limit, the less we can tolerate any noise or power-conversion ripple in the input. At the extreme, we would need a regulated power supply to feed the linear regulator itself, and must face efficiency issues there as well.
Synthesizer fans often attach a great mystique to linear regulators and will pay inflated prices for them as opposed to other kinds of regulators or upgrading other important parts of the power system (such as distribution wiring). I'll comment more on that in the section on switching regulators below, but at this point I'll say that when you insist on a linear regulator, you are not only paying a cost in money to buy it; it also has an environmental cost associated with its limited efficiency.
Even if we cared only about audio quality and not at all about efficiency, it's worth mentioning that when a circuit couples audio onto the power bus, demanding current from the power supply in proportion to the instantaneous audio voltage, it is essentially forcing the voltage regulator to act as an audio amplifier itself. Even a good general-purpose linear regulator may not really work well as a high-performance audio amplifier; that's not what voltage regulators are for.
In the context of something like a guitar amp, the power supply and the amplifier as such will be designed together with the final output signal in mind, and they can share the responsibility for the final output quality. High-quality guitar amp design does trace audio all the way back to the power supply filter. But in a modular synth, where the power supply is designed separately from the modules and must supply many different modules in varying combinations, such a synergy isn't possible.
Well-designed modules really need to isolate themselves as much as possible from the power supply at audio frequencies, and not depend on the power supply to pick up wildly-varying audio-frequency loads. And when modules are defensively designed that way, they won't be particularly sensitive to the quality of the power they receive, or what kind of regulator it came through.
Switching regulators
The power consumption in a linear regulator, which limits its efficiency, is basically all in the pass transistor, which must drop the voltage difference between input and output at the full output current. If we want to improve the efficiency any further, that's where we need to reduce power consumption.
There are two ways to reduce the power consumption of the pass transistor: we could cut the voltage drop, or cut the current. Power is the product of these two quantities, so if we cut voltage drop almost to zero, the power will be low despite high current, whereas if we cut the current almost to zero, power will be low despite high voltage drop. Consider an electromechanical switch, which can be open or closed. When open, it has effectively infinite resistance and no current flows. When closed, it has close to zero resistance, a great deal of current may flow, but the switch itself dissipates almost no power because it has almost no voltage across it. A switch can switch large amounts of power without heating up itself.
We can't drive the pass transistor into either low-power state and just keep it there while it's hooked up directly to the load in a linear regulator configuration, because that would mean delivering the wrong voltage or current to the load. But maybe we can switch between the two low-power states very fast, in such a way that on average voltage and current seen by the load are correct, but the pass transistor spends all its time in a low-power state. That is the operating principle of the "switching regulator," illustrated in the circuit sketch below.
Switching regulators started to become popular in the 1980s and are now pretty much the standard way to generate regulated power for electronic equipment. Virtually all the power supplies in consumer electronics products use switching regulators.
The box labelled "control" consumes a small amount of input power for its own purposes, measures the load at the final output, and determines how much (that is, what fraction of time on average) the pass transistor should be turned on. The pass transistor, which I've illustrated by a box with a switch symbol in it to emphasize that it's operating in a switching mode, is (except for brief moments when it switches between states) always either dropping a large voltage and essentially no current, or a high current and almost no voltage. It typically switches on and off at a rate of a few hundred kHz, though this can vary. Higher frequencies make the filter easier to design, but also are more likely to start behaving as radio waves and require shielding to prevent interference. The filter averages the pulse train out, rejecting the AC component to pass only DC power to the output.
It's worth knowing that "class D" audio amplifiers work in much the same way, with a transistor that switches on and off at rate high above audio, with a duty cycle determined by the desired output voltage. And they do it for the same reason as switching power supply regulators: to achieve better power efficiency than the typical "class AB" audio power amplifiers. As I mentioned before, power supply regulators are really not so much different from audio power amplifiers themselves.
When the load requires more current, the regulator needs to provide more power through the filter to keep the voltage up, so the control circuit will turn on the pass transistor at a higher duty cycle (larger fraction of the time in the cycle). When the load requires less current, the control circuit will back off the pass transistor, turning it on for less time to keep the voltage from going too high. The input voltage may possibly vary too, resulting in further changes to the pass transistor's switching pattern. Control circuits for switching regulators are sometimes quite complicated, because they must respond to multiple effects.
Something remarkable about switching regulators is that they can (depending on the design) actually generate a higher voltage at the output than at the input. I have indicated the input voltage as a range, 5V-20V, on the sketch to emphasize that. There is no magical source of free energy involved. The higher output voltage is compensated by higher input current so that the output power is no greater than what comes in through the input. The best way to think about what's going on here is that filters don't just filter frequencies. A well-designed passive filter can also match impedance, that is, the ratio of voltage to current. When a switching regulator is boosting a low voltage to a high voltage, the filter is just converting the low impedance at the output of the pass transistor into a high impedance to drive the load; that entails swapping current at the input for voltage at the output.
These are made-up numbers, but let's suppose that the control circuit in my example draws 20mA from the input to power itself. That is a little on the high side, but will emphasize some effects I'd like to talk about in the graphs, and it expresses the intuition that this is a more complicated control circuit than you'd find in the linear regulator. Then let's say the pass transistor has a voltage drop of 0.2V when it's switched on, and the filter operates at 95% efficiency. With those assumptions, the input current for different output voltages and different input voltages down to 5V, is as shown in this graph.
Note that for low input voltages, when the regulator is boosting the voltage, the input current is much more than the output current, which might look like poor efficiency but there's more to the story. At high input voltages, the switching regulator actually draws less current from the input than it provides at the output - a feat that would seem impossible under the basic theory of linear regulators.
We can get a better understanding of what's going on by multiplying voltage by current and plotting the power efficiency of the switching regulator.
At low output currents, as with the other regulators, the efficiency suffers because of the power consumed by the regulator itself (that 20mA quiescent current). As output current increases, this effect disappears because the power going through to the load outweighs it; but it takes longer to approach its final high-power efficiency level in the case of high input voltages because the quiescent power is 20mA multiplied by input voltage and that is more when the input voltage is higher.
As output current increases, the regulator approaches a limiting efficiency level which is determined mostly by the 95% efficiency of the output filter. But - unlike the linear regulator - this efficiency level is approximately the same for all the input voltages, only slightly worse when input voltage is low (because the 0.2V voltage drop in the pass transistor is more significant then). It actually works best with a high input voltage, which was the worst case for the other two regulator designs. And at all but the lowest current levels, for all input voltages, the efficiency is better than the best the linear regulator could do.
Switching regulators can easily be more efficient than other regulator designs. That not only means less wasted power directly, but also that because there is less wasted power turning into heat in the regulator, there is less need for a bulky heat sink to carry away that heat, large power-handling capacity in the pass transistor, and so on. The combination of these factors makes for a significant win as to the environmental impact of the regulator. Being able to accept a range of input voltages also makes it more possible to build the upstream unregulated power supply to accept the different voltages used around the world; there's less need for keeping the voltage coming into the regulator consistent.
The big disadvantage of a switching regulator is that there's a significant flow of high-frequency AC power going through parts of the system. If it's not designed carefully, a little bit of that stuff can escape, either passing through the filter or by electromagnetic coupling, and appear in other parts of the system where it shouldn't. The escaped high-frequency AC may or may not cause problems. Because there's a filter between where the control system detects the voltage, and the pass transistor where the control is applied, there can also be some complicated effects limiting the ability of the regulator to respond quickly to changing loads. This, too, places extra strain on the designer to get everything right.
There is nothing you can ever say to an audiophile to convince them that they can't hear interference at 500kHz, 25 times higher than the highest frequencies human beings can really hear. If there's a switching regulator in a system, the audiophile will claim to hear it, regardless of the evidence of blind listening tests. And worst of all, the switching transistor and its control circuitry are, horror of horrors, digital. That alone is a reason for some people not to buy one.
On a more serious note, some circuitry (especially digital circuitry, which uses a lot of high-frequency pulses of its own) can respond in a bad way to interference human beings cannot directly hear. I've also heard a claim that high-frequency interference from a switching regulator can "mix" (in the radio sense of the term, which is what we call ring modulation in the synth world) with other signals or interference sources to produce modulation products at lower, audible frequencies. That's a little far-fetched but not completely impossible, and I'm sure there have been cases where it has happened.
So a poorly-designed switching regulator with dirty output may cause bad things to happen like microcontrollers crashing, or sequencers randomly advancing to the next step. A bad switching regulator could produce interference that screws up your AM broadcast radio receivers. Problems may be more likely with ultra-cheap commodity switching supplies that were repurposed from non-audio applications; and every idiot on the Web insists that switching regulators cause problems all the time, and they can never be talked out of this belief! Switching regulators are quite popular, nonetheless, because they actually do work, and they're cheap.
Switching regulators are the environmentally preferable solution; they have some other advantages, too; and they're more complicated. The design of the regulator, and particularly its output filter and the shielding of the internal high-frequency transmission, are important. A poorly designed regulator may provide dirty power, and especially when feeding sensitive audio circuitry, it may not be easy to get the design right.
One compromise sometimes used in modular applications is to use a switching regulator for the main flow of power from the unregulated "wall wart" supply, but then regulate it again with a linear regulator to a lower voltage, possibly on a local basis. Some of the fancier active bus board systems do that, and I did it myself internally to the Leapfrog VCF. Although the Leapfrog is designed on the assumption that the ±12V power busses are at least sort of clean (as they certainly ought to be), some of the more sensitive parts of the filter core make use of an internal 9V bus regulated down from the +12V by a linear regulator. The power level there is low enough that there's no significant waste involved. The two-level approach is necessarily less efficient, but it reduces the demand on the main system regulator, which quite likely will be a switcher, to really clean up the power as much as it should.
Final thoughts
The three most important points on modular synth electrical consumption as to environment impact are:
- You ought to be using a well-designed switching power supply. Some emphasis is necesasry on "well-designed," and if it really is, then there is no legitimate basis for the common claim that it's going to harm audio quality.
- Any power supply is going to be inefficient if it is loaded far below its intended capacity; having a safety margin is reasonable, but don't use a power supply specified for a lot more than your actual requirements, because it will be less efficient.
- Where the power comes from, such as hydro, nuclear, or coal, is more important than exactly what kind of power supply you use, and the power usage of even a bad modular power supply is insignificant compared to other electrical applications - notably, any electrical devices that manage heat, such as heaters and air conditioners.
Next up: the environmental impact of metals in synthesizers.
◀ PREV Coiler VCF (pre-) release, vacation || Green modular, part 2: the big three metals of RoHS NEXT ▶
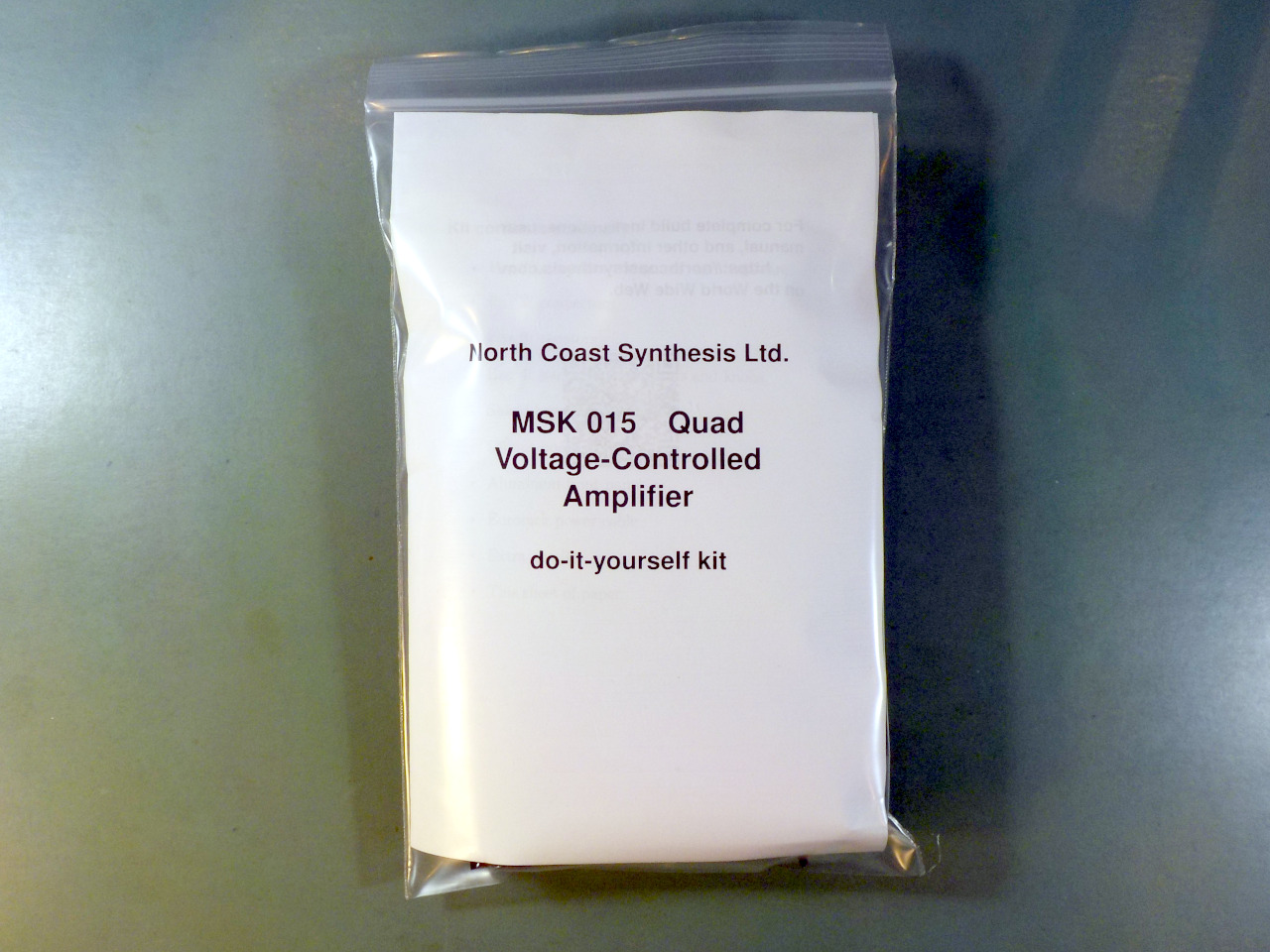
MSK 015 Quad VCA SDIY Kit
US$309.96 including shipping
Comments
My impression of their marketing on that is quite negative: it's a completely different design with different technology (CMOS instead of JFET input) and it looks like the only reason for giving it the model number they did, is to bamboozle customers into thinking it's a direct and perfectly equivalent replacement. However, just on its own merits it does seem to have decent performance for audio and lower power consumption in particular as compared to the TL074 classic.
Making LEDs dimmer, or switching to high-efficiency ones so they can still be bright at lower current, clearly also makes a big difference. I used a high-efficiency LED in the Transistor ADSR mostly to avoid loading on the circuit that drives it, but it'll also be saving some power there. There's less ability to do that when using a tri-state LED, which may not come in a high-efficiency version.
I routinely find LEDs to be too bright and I adjust to taste; for example personal builds of the Fixed Sine Bank use 11k current limiting resistors in place of the specified 510r. As a side benefit, the module's power consumption is reduced to around 31mA total between the two rails.
As a further experiment, I swapped the TL074s for TL064s, and now measure a total power consumption of just 6mA. I've build the full enchilada of Sine Banks A, B & C into a single panel, and I feel like ~18mA vs ~240mA in the stock configuration is a worthwhile difference.
Do you have any suggestions for when one might consider substituting in TL06Xs? I know they have inferior specifications for noise and slew; is it mostly a "try it and see" operation?