Green modular, part 2: the big three metals of RoHS
2019-01-18 chemistry environment
In this second part of the series on modular and the environment, I'm going to look at metals. Modular synthesizers are made of many different materials including wood, plastic, and glass, but a significant part of the mass of a synth (or any electronic device) is in metals. Even though metals are often used in small amounts, they often make up a disproportionate fraction of the environmental impact of electronics manufacturing because of all the energy that goes into mining and processing them. There are also unique issues for specific metals: some are toxic, some are rare, some have important social consequences, and so on. I had planned to have just one posting on metals in this series, but it became too long, so I'm going to cover just the "big three" forbidden by RoHS here, and talk about the others in one or more future postings. There's a lot to say about metals.
The European Union Directive on Restriction of Hazardous Substances (RoHS) is a good starting point because it's something manufacturers selling electronics into Europe need to think about a lot. The Directive's main purpose is to reduce the harm from toxic substances getting into the environment when electronic products reach the end of their usefulness and are thrown out. There are a lot of complicated rules and some exemptions applicable, but in general RoHS forbids ten "harmful substances": the metals lead, mercury, and cadmium; "hexavalent" chromium (primarily used in anti-corrosion coatings) but not the metal as such; and six organic chemicals generally used in plastics (two brominated fire retardants and four phthalate-ester plasticizers). Manufacturers selling products into Europe have to be able to certify that the products do not contain those ten things.
Lead
Lead is the most significant item for electronics because, pre-RoHS, lead solder was for decades the standard way to make connections between components. In terms of actual amount of lead used, I think more of it was going into batteries than into solder. But solder was certainly also a major application of lead, and determining that we had to stop using it was certainly a blow to the electronics industry. Lead was not only in the solder that we would actually melt with a soldering iron or wave-soldering machine, but also in the coatings applied to the leads of components to allow them to be soldered. So to comply with RoHS it's not only necessary to buy different solder as such, but also to make sure that all the components are themselves designed for a lead-free process. It has taken a long time to come up with substitutes that would even sort of work, and there are still plenty of annoyances in parts sourcing and trying to document that every component in a product is lead-free.
Traditional solder over most of the history of electronics was 60/40 alloy: 60% tin, 40% lead. Toward the end of the lead-solder era "eutectic" solder started to become popular too, with just a little bit more tin (63% instead of 60%). The eutectic alloy was a little more expensive and may have had some disadvantages for corrosion resistance, but it also melted better than traditional 60/40. The big advantage of both lead-based formulations was that the solder would melt at a low temperature, which meant a minimum of thermal stress on sensitive components. It was also durable, "wet" (in the sense that it could easily stick to the other metals that it was joining), and it produced nice shiny-looking joints. With 60/40 lead solder there was a significant issue of "cold" or "dry" solder joints, where basically the tin would melt but not all of the lead, producing a slushy not-quite-liquid substance that would harden to look dull instead of shiny, and give a bad electrical connection. It was easy to recognize bad solder joints on a lead-solder board by looking for the dull ones.
I've been required to follow RoHS rules at North Coast Synthesis right from the start, and so I've been using "Sn96" lead-free solder alloy in all my assembled products. That is 96.3% tin, 3% silver, 0.7% copper. This alloy needs to be heated a little hotter than old 60/40, and it sticks less well to the surfaces being joined, making it somewhat annoying to work with when one first makes the switch. I found it didn't take me very long to get used to the new stuff, however. The Sn96 solder is also a fair bit more expensive than the old lead alloy, and when it solidifies it looks dull regardless of whether the joint is good or not.
The appearance of the lead-free alloy has gotten me some complaints from people who've seen dull-looking joints on North Coast products and assumed that that meant the joints must be all 60/40 lead solder and all defective. I'm not sure what I can say to such people. Using lead-free solder is not something I have a choice about; and although there are other lead-free alloys than Sn96, some of which are shinier, the other alloys have disadvantages of their own and I'm not about to switch to a less-appropriate alloy just to satisfy some idiot who doesn't know what real quality looks like.
Some controversy exists about whether avoiding lead solder is really the right environmental choice after all. Most of this controversy to be honest is not legitimate. In particular, there's a common claim that lead is harmless if you don't put it directly in your mouth and chew - which is simply not true - or that it's all okay provided you wash your hands after using lead solder. Hand-washing is nice for the persons actually applying the solder, but they were never the ones at most risk of harm from lead solder anyway. It is inevitable that the solder in an electronic product will eventually get into the environment and the point of RoHS is to reduce the toxicity of the waste. It's not the assembler but someone drinking groundwater years later who ends up poisoned by the lead.
It is sometimes claimed that "tin whiskers" are a real problem that cause many electronic products made with lead-free solder to fail after a few years and require replacement, resulting in an increased environmental footprint compared to lead-soldered products because of the manufacturing of all the replacement products. I've even heard a conspiracy theory that "tin whiskers" are actually the purpose of RoHS: that it's all a scam put forward by electronics manufacturers to implement planned obsolescence and sell more products in the future. That's nonsense and I'm not sure I should dignify it with a detailed response, but I'll just point out that RoHS has been in force 16 years now, with lead-free electronic solder deployed in limited applications long before then, and the supposed tin whisker problem has never manifested to any degree worth noticing in consumer products. If you are building spacecraft, which have much different thermal performance requirements from those applicable to consumer products, then okay, you may need to consider some special engineering issues related to solder reliability and whisker formation in both lead-based and lead-free alloys. We are not building spacecraft here.
Nonetheless, if you must worry yourself about "whiskers," you should be aware that it takes a much bigger whisker to short out a circuit board made with through-hole technology (connections seldom placed at spacing smaller than 2.54mm) compared to a surface-mount board (connections routinely at 1mm or less). If there were going to be a tin whisker growing on a synth board, which there won't be, then it would cause a lot more trouble on the surface-mount board. And although I can't promise that all North Coast products will always be this way, at present all North Coast products do happen to be through-hole.
There is a genuine issue, more safety-related than environmental, with lead-free solder as a result of its higher melting point. Because it usually melts higher, soldering with lead-free solder produces more toxic fumes from the flux (not from the metal itself) compared to soldering with low-temperature lead alloy. Because it's less "wet," lead-free may also need more flux, or a chemically more aggressive flux. What these factors add up to is that for the person actually applying the solder, the health risks of using lead-free may be worse. It may be more important to use proper ventilation after switching to lead-free.
Overall, I think it just makes sense to use lead-free solder. It doesn't really matter what I think, for my own practice, because I am constrained by legal requirements; but even for hobbyists who aren't selling their constructions, I think in this day and age there is no legitimate reason to insist on sticking to lead. Nonetheless, the kits I sell should build up well with either type of solder.
Mercury
Mercury is next on the list. It was formerly used in some batteries, and it still is used (under an RoHS exemption, because there is basically no substitute) in fluorescent lights. Mercury was also significant in some old vacuum tube devices, such as power rectifiers. But it never had significant application in solid-state electronics, so for anyone building synthesizers of the discrete-transistor historical period or later, there's no big difficulty in avoiding mercury. This one is pretty much a gimmie.
There is a different way mercury can be relevant to electronics, and it's by way of coal-fired power plants rather than RoHS. Coal contains mercury - not a lot of it, but the stuff is so toxic that even a little bit counts - and that mercury is released into the atmosphere when the coal is burned. If you're using electricity from coal-fired power plants, in an application that is not energy-efficient, then the mercury emissions associated with a product may be considerable even if the product itself contains no mercury. For that reason when you count the mercury released by the power plant, modern compact fluorescent light bulbs, despite containing mercury, actually result in less total mercury pollution than the equivalent incandescent bulbs powered by coal-fired power plants. That is even if the bulbs are not properly recycled at the ends of their lives; with recycling, the mercury in the bulb can be recovered for reuse instead of going into the air, too. However, for synthesizers in particular the electricity consumption is small enough for this kind of thing not to be a big deal. I wrote about electricity consumption in the previous posting of this series.
Cadmium
Cadmium is interesting because although it was easy for the electronics industry in general to give it up, it has become a serious issue for synthesizer manufacturers in particular. Cadmium was used sometimes in special low-melting solder alloys, but never to any great extent because it was too expensive to be practical except in small amounts and very limited applications. Nowadays, we usually use much less toxic indium to replace cadmium in those kinds of special-purpose solders.
The main application of cadmium before it was banned was in nickel-cadmium rechargeable batteries. Those were a huge thing; for a long time, anywhere you had a rechargeable battery, you had cadmium. But nickel-cadmium batteries also had many serious limitations. They didn't last through very many charge/discharge cycles; they had to be charged and discharged on a careful schedule or else their lifespan would be even shorter; they were not the voltage people wanted; cadmium was expensive, making the batteries expensive; and so on. At around the time RoHS came in, manufacturers were already switching to more recently-developed rechargeable battery chemistries, usually based on lithium, which has its own environmental issues too but is nearly non-toxic. So the RoHS cadmium ban only required the industry as a whole to give up something it was already in the process of giving up by choice.
But there was a trap for synthesizer makers in the shape of something called a Vactrol. The crystalline substance cadmium sulfide changes its electrical resistance in response to light (much lower resistance in bright light than in darkness), and so it can be used to make light-dependent "photoresistors." At one time, photoresistors based on cadmium sulfide or the closely related cadmium selenide were the only practical way for an electronic circuit to detect changes in light intensity.
If you put a photoresistor in an audio circuit, position an LED to shine on it, and block out other sources of light, then you've got a resistor whose resistance depends on the amount of light produced by the LED. And that's a really convenient way to make your circuit voltage-controlled. Modulate the LED brightness and you modulate the resistance of the photoresistor. It's an easy way to add voltage control (really current control at the LED itself, but that's easy to convert) to almost any circuit; thus attractive to synth designers.
Pre-packaged LED/photoresistor combinations were sold under the name "Vactrol," originally a trademark of Vactec, Inc., but now a generic term for any similar product. They never really worked very well. First of all, it is difficult to do good quality control on photoresistors. There is a large range of manufacturing variation on dark resistance, response to light, and so on. Different Vactrols of the same model, even from the same batch, will not necessarily respond identically. They also don't respond quickly. When the light level changes, it can take several milliseconds for the photoresistor to change its resistance.
Old-time synthesizer designers used Vactrols despite their problems because nothing better existed. Sometimes, as for instance in some compression circuits, they attempted to make a virtue of the Vactrol's failings - you don't want a compressor to respond instantly, so if you can find a Vactrol that slows the modulation down the right amount, then you can avoid needing to design some other way of slowing the response.
Because Vactrols were in some "vintage" circuits, they have acquired a certain mystique. Persons building reproductions of old synthesizer designs want to build them with authentic components, including Vactrols. There is no simple way to substitute a modern replacement for a Vactrol in an existing circuit. I go through some options in one of my earlier Web log postings but the bottom line is that you need to do a major redesign. The characteristic slowing of envelopes caused by the use of Vactrol VCAs is now considered "classic" and desirable. Designers continue putting Vactrols in new designs to cash in on the mystique and name recognition. Make Noise advertises "Uses Vactrols" as a selling point of its DPO complex oscillator.
And they're banned.
You can't really build a Vactrol without cadmium, and cadmium is forbidden by RoHS for consumer products sold in Europe. The story sometimes circulates on synth fora that there is an RoHS exemption for Vactrols, but it isn't true today - the exemption seemingly was only in force in 2013, and despite efforts of synthesizer manufacturers to beg for it to be reinstated, it has not been.
Vactrols are still legal in many places outside Europe, but the fact that they are basically obsolete combined with the European ban means that they are no longer attractive for new designs even in places where they're still legal. So they're getting harder and harder to find globally, with prices going up and availability of specific models going down. Only people building synthesizers still want them, only a limited subset in fact who either aren't bound by or are willing to break the European rules, and those people are too small a market to support the continued manufacture of Vactrols. So it seems clear that Vactrols will continue to fall out of use and eventually just not be available anymore at all.
Just for me it's not a huge hardship because I'm more interested in new designs than in cloning specific circuits of the past anyway. In a new design it's feasible to do everything that used to be done with Vactrols, using modern techniques instead. If you want poor quality control, add a trimmer and tweak it at random! If you want slow response, slow it artificially. But that means doing a complete new design. The way Vactrols were used in older circuits means that it generally is not possible to just take out the Vactrol, drop in a modern "Vactrol substitute," and leave everything else the same. So it's a genuine problem for anyone who does want to clone or recreate an old circuit from before the ban; they have to make much bigger changes than they would like to make.
I have sometimes thought that it would be fun to to make a "digital Vactrol simulator" VCA or LPG; it could use some of the same analog-modelling technology that goes into guitar-amp simulators, offering a configurable choice of which model of Vactrol to simulate, and maybe some optional extra features like zero-crossing detection to reduce clicking. I'm not sure that that would really be popular enough to be worth developing, though.
Chromium, etc.
I'm not sure whether to count hexavalent chromium as a "metal" at all, because although it is a metallic element, what's banned is specifically the Cr6+ ion, not the metallic form. It's nasty stuff - carcinogenic and in some compounds a dangerous oxidizing agent. Nile Red, on YouTube, has made some entertaining videos in which he uses hexavalent chromium compounds. I always get a kick out of procedures where he needs to lubricate his equipment with concentrated sulfuric acid because the stuff inside is too nasty to use regular grease.
The places you'd most often encounter hexavalent chromium in electronics manufacturing are largely in anti-corrosion coatings on physical hardware kinds of things. Some steel screws receive a chromate coating, and I think some aluminum panels have chromate surface treatment (attractive in that case for its electrical conductivity). There are not all that many places where a synthesizer would be likely to contain Cr6+ and it's usually reasonably possible to find substitutes, maybe with a small increase in cost. Hexavalent chromium may also occur in some paint pigments, so there'd also be a need to look carefully at those in a product that had a painted finish.
So I've summarized the metals forbidden by RoHS. Those, especially lead, are probably the most significant ones for metal-related environmental consequences of synthesizer manufacturing. In a future part of this series, I plan to discuss the other metals in a synth: precious metals like silver and gold, and base metals like iron and aluminum.
◀ PREV Green modular, part 1: Energy, carbon, and power supply regulators || Green modular, part 3: More metal NEXT ▶
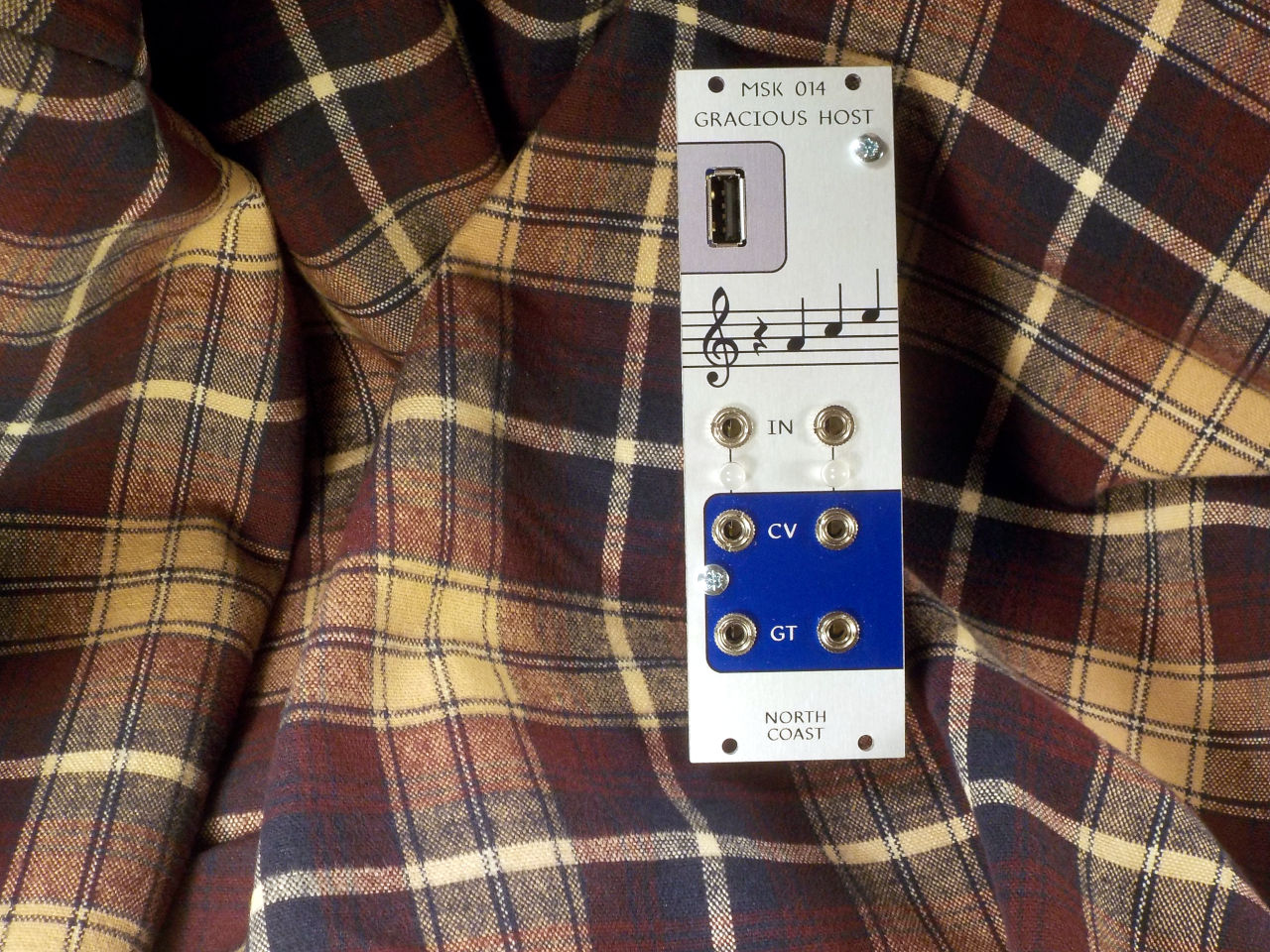