Marbled and hydrographic panel gallery
2021-05-02 panels
As described in an earlier posting a month ago, I've been experimenting with painting and printing on a batch of defective Eurorack module front panels, trying to both salvage them into something usable and develop some techniques that will be useful in my future products. Here are some photos of my progress on marble painting and hydrographic dipping.
The earlier gallery covered tape masking. Next on my list of things to try was marble pianting: applying paint to the surface of a tank of water, swirling it around, and then dipping the panel to pick up the swirled pattern. This is similar to what people traditionally did with paper to create the endpapers of fancy hand-bound books.
I got some pretty good patterns out of this, but it was variable. Some colours behaved a lot differently from others and it was hard to control the results.
It was the grey and pastel colours that really seemed to produce the most consistent stripes. Black tended more toward smearing. I guess which is the nicer effect depends on personal taste, but my original plan was to do some panels mostly black with thin bright-coloured stripes, and that didn't seem to be possible with these particular paints because the black was just too greasy.
If I end up doing this again I will probably experiment with using liquid, non-spray paints instead of the spray cans I was using here. That would reduce some of the safety issues, and would also give me the chance to possibly mix things into the paints to change their behaviour on the water surface - which might help with the controllability.
Next after the marbling, I wanted to try printed hydrographics. I've heard both this process and the marbling process called "hydro-dipping" (because they both involve transferring ink or paint from a water surface) but I'm trying to call them "marbling" and "printed hydrographics" to keep them separate. Anyway, here are some surplus circuit boards covered with primer for use as test pieces for the printed hydrographics. I made up four of these, which turned out to be not nearly enough to debug the process and I ended up doing a lot of debugging on the aluminum panels that had been intended as more like "production" pieces.
Aluminum panels, similarly prepared. The prep consisted of sanding off as much as possible of the original, defective, UV-printed graphics (320-grit silicon carbide paper, used wet with a block); cleaning and degreasing (99% isopropyl alcohol); spraying two coast of "galvanized metal" primer; 72-hour cure time; scuffing (grey Scotch-Brite); then cleaning and degreasing with alcohol again.
Hydrographics films prepared for dipping. I bought a grab bag of ten randomly selected patterns from a Chinese company, and I suspect these Pokemon films may not have been properly copyright-licensed, so I reserved them for test dips that I knew I wouldn't be selling. The tape around the edges in this picture has more snips in it, to allow for expansion, than is really ideal. It would be better to have more than zero snips, but fewer than shown. That was one of the things I learned from doing the test dips.
The way the hydrographics process works is that the design is printed on a special plastic film. The bulk of the film is polyvinyl alcohol (PVA), which slowly dissolves into slime on contact with water. It's the same stuff they make laundry detergent pods out of. The printing ink is sandwiched between that and a very thin layer of some other plastic that dissolves in oily organic solvents and not in water. So you lay the film PVA-side down on the water surface, wait a certain amount of time for the PVA to turn into slime but not completely dissolve, then spray it with something that's called "activator" - an oily solvent that dissolves the other film, and converts the ink into a liquid that floats as an oil slick on the water. Then you dip the part to be printed. The activator is supposed to make the primer or undercoat that's already on the part, tacky enough to retain the ink; and the whole paint/activator/ink system is hydrophobic, that is, "oily," so it doesn't dissolve into the water.
Here are some of my first dips. I was experimenting with the amount of activator and the soak time needed to soften the PVA enough for it to stretch smoothly but not fall apart. You can see some gaps in the design where the film either tore, or failed to stick.
It's hard to get commercially-prepared hydrographic activator solvent here in Canada, and the kinds I can relatively easily buy all contain dibutyl phthalate (DBP) - a substance banned by European environmental regulations. If I used that, it would probably all evaporate away before my products were ready to sell, so there wouldn't be a residue left in the product to entertain the European testing labs, but I don't know that for sure. It might be hard to prove my products ended up DBP-free if I made them using DBP, and it would certainly be a big hassle, never mind the safety and local environmental-reponsibility issues of using DBP in the first place. So I ended up trying to develop my own less-toxic alternative that would be compliant with both European and Canadian rules, could be mixed from ingredients I could actually get, unlikely to attract the wrong kind of legal attention, unlikely to poison me or my neighbours, and so on. The mixture I devised is called "775 activator." It's a mixture of orange peel oil; a solvent/surfactent commonly used in window and whiteboard cleaners; and petroleum distillate. It seems to at least sort-of work in the hydrographic printing process, and it's a lot less toxic than the DBP, xylenes, and other such things usually included in the commercial solvents; but it's still dangerous enough to require some serious safety precautions and it may not really work as well as the more-toxic versions do. That's why I'm not publishing it as a do-it-yourself project. Since I'm probably not going to be doing much more printed hydrographics after this batch, it doesn't make sense to invest more time and money into trying to improve my proprietary activator formula futher.
Here are the first of what were intended to be "production" printed hydrographic dips - but I was still experimenting with the soak time and activator level, and half of them ended up getting scrubbed off and re-done. After dipping, it's necessary to rinse the dipped parts in water to remove the remaining PVA, and that's a lot of work, several minutes per panel. If the activation wasn't right, or if they're rubbed too vigorously while rinsing, the graphics detach from the primer and wash away. But the PVA does need to all be removed or it'll interfere with clear-coating later.
On the next batch I had something else happen, which I hadn't been expecting: the primer on some of them, especially the white-background "love and death" ones, wrinkled up and then fell right off the aluminum! I think that may have been another effect of too much activator: it's meant to dissolve the primer layer a little, so the graphics will stick, but I think if there's too much activator it may make the plastics in the primer soften and swell, losing their adhesion to the metal, and then the flowing rinse water can pull the primer layer away. Anyway, the panels affected by that needed to be not only re-dipped, but re-prepped all the way from the bare metal stage.
Here are the panels on which I needed to start over re-priming them, after all the other dipping was done. I experimented with taping them into a shallow cardboard box, and to each other, to make them easier to carry outdoors and back for the spraying, and that turned out to work better than having them loose - so I'll be doing it again for all the panels when I get to the clear-coating stage.
I got some enamel "paint marker" pens for adding panel graphics - jack socket labels, model numbers, and so on - to all of these panels. Those are just visible at centre right in the photo. Here are some of the tape-masked panels with those markings added by hand. The pens can't do really fine lines, and the graphics are less detailed than on normal, UV-printed, production modules. I didn't want to detract from the custom painted and printed graphics, and I basically figure that users of these customized modules will be able to learn what each knob and jack is for, using the labels only as reminders.
Coiler VCF panels with marbling and panel graphics. In this image you can really see how the different colours of paint also have different textures, because of differences in how they interact with the water surface.
Middle Path VCO panels with marbling and panel graphics.
Here are some of the printed hydrographic panels with panel graphics. The printed graphics are often "busy" enough to make it hard to see the labels, and I only had the pens in black, white, and silver metallic; so it wasn't always easy to make the labels very visible. But, it may be better that they not detract from the printed imagery anyway. As I say, I expect most users to basically learn the functions of the jacks and knobs by position and only use the labels as memory aids.
The last batch, dipped but not yet rinsed. I was really hoping these would survive rinsing and not need yet another round of dipping.
Here are the same panels after rinsing. If you look closely you may be able to see some places where the prints were damaged during the rinsing process, especially on the "flame skulls" design; but I think all are good enough that, maybe with touching up in a few places, I can use them without needing to start over yet again with additional dips.
And that's where the project currently stands. I still have to do panel graphics on that last batch of printed-hydrographic panels, then clear-coat all the panels. The clear coating involves a two-part polyurethane, which I have to use outdoors in good weather with a lot of safety gear and within a short space of time (because once mixed, the spray can is only useful for a day). So it requires some careful planning. Then after the clear coat has finished curing, I guess I can try to figure out how to sell these panels, to make back some of the development expenses. I'm thinking they will probably go into a special edition of assembled modules.
◀ PREV Aconcagua || Gracious Host development adventures NEXT ▶
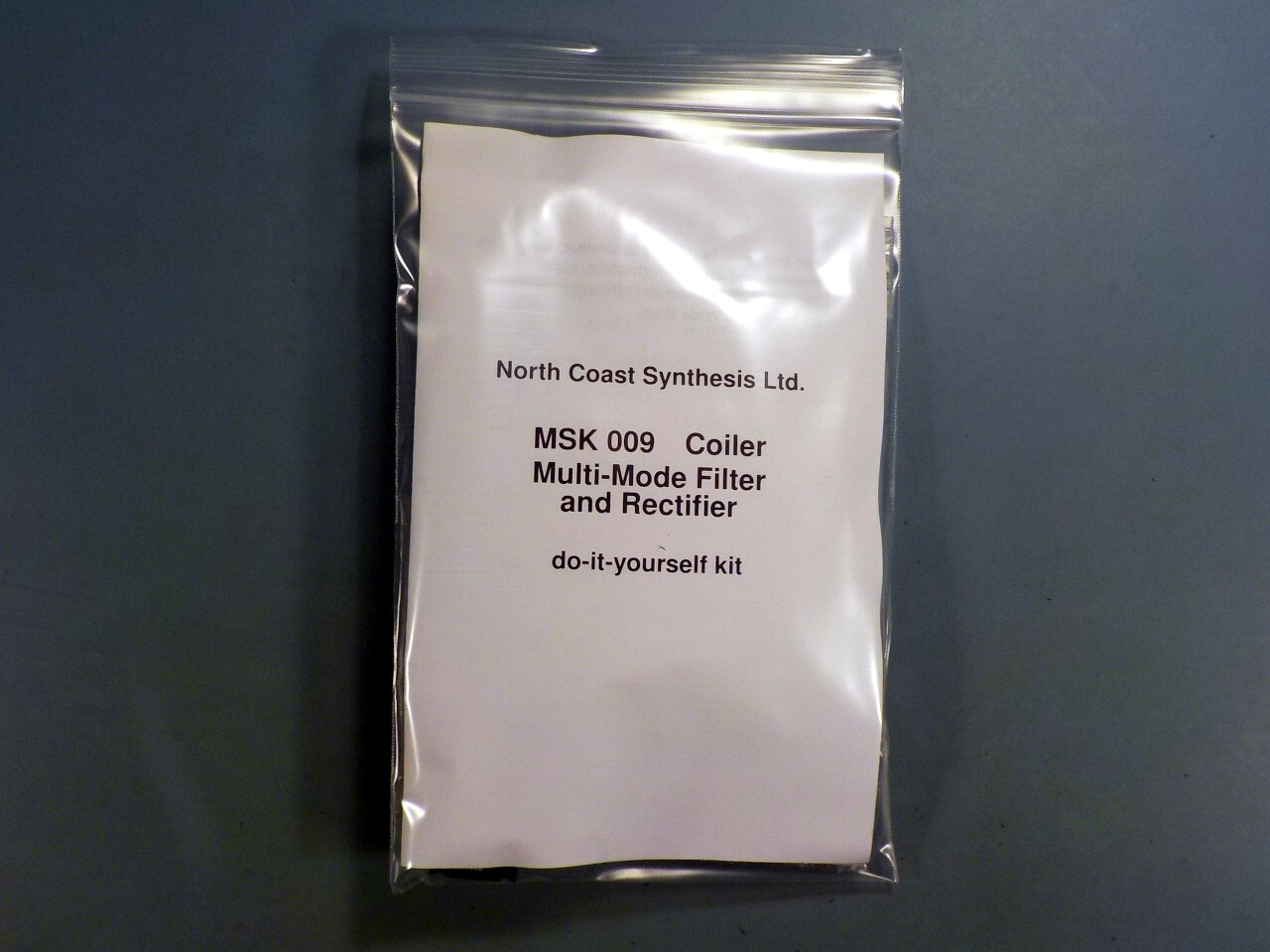