Testing homemade fluxes
2019-06-13 SDIY chemistry science!
In the last four articles (start here) I've gone through a lot of the technicalities of flux: what's in it, how it works, and how to make your own. Now, let's bring it together and try out all these experimental fluxes.
What about the solder?
The only solder I normally have on hand is MG Chemicals 4900. This is a lead-free Sn96 alloy with a built-in no-clean rosin flux. So to test my homemade flux formulations by themselves, not just as additions to the built-in flux from the solder, I needed to first obtain some fluxless solder.
Some of my buddies on the Net were saying I ought to go out and mine my own tin and lead and make artisanal solder too, but that's really beyond the scope of this project and anyway Cody already covered it (YouTube link). Instead, I just took some of my flux-core solder wire, put it on a chunk of aluminum foil, and cooked it on the kitchen stove until it melted and the flux mostly came out. At that point the liquid solder rolled up into little balls. I washed the balls carefully in isopropyl alcohol to remove the flux residue, and then flattened them with pliers and cut them into small pieces.
This flux-removal process was a bit fiddly and didn't work really well. I had a hard time cutting the solder balls into small enough pieces to use, and (as you can see in my video below) using the cut-up chunks with flux as a separate liquid wasn't convenient. I also had an issue with an earlier attempt in which I tried slowly baking the solder in the oven instad of heating it on the stovetop, and when I did that, it ended up oxidizing pretty badly. Using the stovetop and stopping as soon as it was fully melted worked out better. But given that I only needed a couple of grams for this entire project, and the project was already overbudget on other things, I didn't want to run out and try to buy no-flux solder.
Soldering with homemade flux
In an effort to do this at least semi-scientifically, here's the procedure I worked out. I selected ten circuit boards left over from prototyping runs during development of my commercial modules: five each with lead-free HASL and ENIG plating. Then the idea was that for each of the four homemade fluxes, and the original MG Chemicals solder with built-in flux, I would solder in three 12Ω resistors in a fixed patten across six terminals of a DIP footprint. I'd make notes on how well the flux seemed to work when soldering, then measure leakage resistance among the soldered terminals, before and after cleaning.
The value of 12Ω was chosen on the basis that I have some resistors of that value that I'm unlikely to use much in the future, so I basically got them for free, and also it's small enough to be effectively negligible in comparison to the multi-megaohm leakage resistances; so these resistors would look like short circuits to the leakage test and I could measure just leakage and not have the resistor values interfering.
Here's the video of me actually soldering with my homemade fluxes, and commenting as I go on how they seem to work. Then I'll summarize in the text below.
As an additional control, I tried soldering a resistor with no flux at all - after all, before we get into which flux is best, it's worth knowing whether flux in general is even worth having. I found it quite difficult, ending up with connections that would probably conduct electricity but certainly didn't look good and might not stand up to mechanical stress.
Proceeding to the five different fluxes under test, I'm summarizing my comments into ratings for wetting and easy of making joints on a {poor, fair, good, very good, excellent} scale; wicking (how well the flux draws the solder through the board) on the same scale although I wouldn't trust that too far because it's affected by many other variables besides the flux; amount and nature of residue; smoke and odour; and any other comments. I'll talk about my leakage resistance measurements - which actually contained some important surprises - in the next section.
Built-in flux from the commercial solder: wetting very good, wicking fair (better on HASL board); light residue; some smoke, no odour; residue turns into a white powder if cleaned without a fair bit of scrubbing.
No-clean-style activated with 3% betaine: wetting very good, wicking good. Spatters a lot if soldered while still wet; as seen in the video, I tried waiting for it to dry before soldering some of the joints and that reduced the spattering significantly. Moderate residue which vanishes with water washing, feels moist on the fingers. Noticeable puff of vapour that condenses on the board all around the solder joint. Mild but distinct fishy odour to the smoke - which I was pleased with, because I'm sure that's the trimethylamine (YouTube NileRed video link) coming out as the betaine decomposes. It basically proves that this random white powder I bought from the bodybuilders really is betaine after all. I don't have an analytical chemistry lab to check, and otherwise I pretty much have to take their word for it.
No-clean-style activated with 3% beta-alanine: wetting good, wicking good. Residue and spatter similar to the betaine flux; no perceptible odour during use. I had a lot of trouble with the wetting of the water-based liquid at room temperature (not the solder wetting) when applying this flux, especially on the ENIG board. In the video I comment on the difficulty of making joints with this flux and going back over the video and looking at the finished board, I think it's because of the wetting issue during application.
Natural pine-resin flux, unactivated: fair wetting, very good wicking, heavy sticky residue. Wetting better on the ENIG board. Strong, pleasant pine odour.
Water-wash flux based on citric acid: excellent wetting, good wicking. Some spattering, but less than with the wet amino acid fluxes. Heavy semi-liquid residue, which dissolves easily in water. Some smoke with a faint citrus-like odour, quite irritating.
Overall the citric acid flux is nicest to work with and seems most effective as a flux, though I have some misgivings about the safety of the smoke it produces. The two water-based fluxes (betaine and beta-alanine) I think need some work, especially for ease of application, but are already comparable to commercial quality. The natural-resin flux is not very active and probably not a great flux as it stands, but I'd say it is credible; it's comparable to the old-fashioned resin fluxes I used to use in the lead-solder days. And it does smell nice.
Leakage resistance tests
I mounted the three resistors in the same pattern across a DIP footprint on each board: two next to each other, then skipping a pair of pads, then the third resistor. This pattern was chosen so that I could find at least one place for it on every one of the ten boards without any of the six pads involved being shorted together by traces on the board. The positive input of an op amp is usually tied to ground, most of the DIP footprints on my boards were either for quad op amps or LM13700 chips (which also often have grounded pads) and so there were many boards where I couldn't just put all three resistors right next to each other and have no traces connecting any of their pads together.
My plan was to measure the leakage resistance with a multimeter on the 200MΩ range between the centre resistor and each of the other two, for two measurements, on each board. I discovered late in the game that my newer, higher-quality multimeter doesn't actually have a 200MΩ resistance range, it only goes up to 20MΩ, and so I ended up using my older multimeter. I'm not entirely confident about its high-resistance measurements. In particular, this meter seems to measure a short circuit as 0.9MΩ instead of zero when set to the 200MΩ range. But it's what I have.
Before cleaning, I measured the citric acid ENIG board's resistances as 94MΩ and 140MΩ and the citric acid HASL board's as one 93M and one out of range. The betaine ENIG board measured 54M and 21M, both measurements out of range on the HASL board. One measurement on the beta-alanine ENIG board was 163M. All other resistance measurements, including all measurements on the boards after I cleaned them, were out of range.
What are we to make of those readings?
I think it's a general pattern that the fluxes wet the ENIG boards better than the HASL during application (not the same as during soldering). These boards were from different manufacturers, are of different ages, and probably have differences in the exact nature of the plastic coating, cleanliness level, etc. So there may have been more tendency for a flux-residue film make connections among the pads that could carry leakage currents, on the ENIG boards. That could explain why I saw measurable leakage more on the ENIG boards for all of the three fluxes where I saw measurable leakage at all.
It is no surprise that the citric acid flux had the worst leakage readings. (That is, it had the largest number of readings not out of range.) This is a very corrosive, electrolytic, ionic, type of substance. It really needs to be cleaned off. However, the betaine and beta-alanine fluxes were both based on formulations I got out of patents that were claimed to be "no-clean." With residues that seemed likely to be hygroscopic, and measurable leakage resistances, I'm not sure I would really trust these two formulations to be left in place without cleaning. I might add that they were very easy to clean - the residue dissolved instantly in water.
Leakage resistances in the tens of megaohms will not actually cause problems in most circuits. So if these fluxes do not cause corrosion, and the leakage resistances don't decrease a lot over time, there may not really be any problem and they might work perfectly well without cleaning. But these leakage test results don't encourage my trust. It's worth bearing in mind that I may have been applying the fluxes wrong in some way (for instance, quantities too large). It also may well be that the 3% activator percentage I used, more or less arbitrarily (plus 0.5% citric acid in each batch), is too high and should be reduced to like 1% or so.
Further thoughts
I've now made four different DIY solder fluxes and tested them in comparison to each other and to commercial flux. This has been a fun project, and there is certainly more that could be done. If I were going further with it, I think I'd focus my attention on the no-clean-style fluxes and trying to get them into a form that I'd really trust to be no-clean. That might include reducing the activator percentages; maybe just reducing the concentration of the whole formulation (more water); and trying to get them to wet better during application. The patents I was looking at talked about adding surfactants to help with wetting during application and I didn't put any specific surfactant ingredients in mine largely because I thought it'd be hard to find a reproducible small-quantity source for them available to other experimenters as well as myself. But I could try harder on that point. Another thing to try might be adding some kind of activator to the natural resin; it was noticeably less active than the others and might be more realistically similar to commercial products if it had some activator mixed in.
I don't think I'm really going to go much further with homemade flux, though, because it's been expensive in both time and money and I don't see much way to make it pay. As far as flux for use in actual electronics work goes, commercial products are already so good, and cheap enough, that making it at home isn't really a useful exercise. But it's educational. I hope others will be inspired to try their own homemade flux experiments and to share ideas. If there's significant public interest I might consider putting together ingredient kits - after all, I still have a lot of leftovers of some of these ingredients, which aren't easy to buy in small quantities - but the number of kits I'd have to sell and the prices at which I'd have to sell them to make it work don't look like a strong business case.
Let me know your results if you do try making your own fluxes. It would be fun to build up a list of links here.
◀ PREV DIY no-clean-style flux || More music of the dwarves NEXT ▶
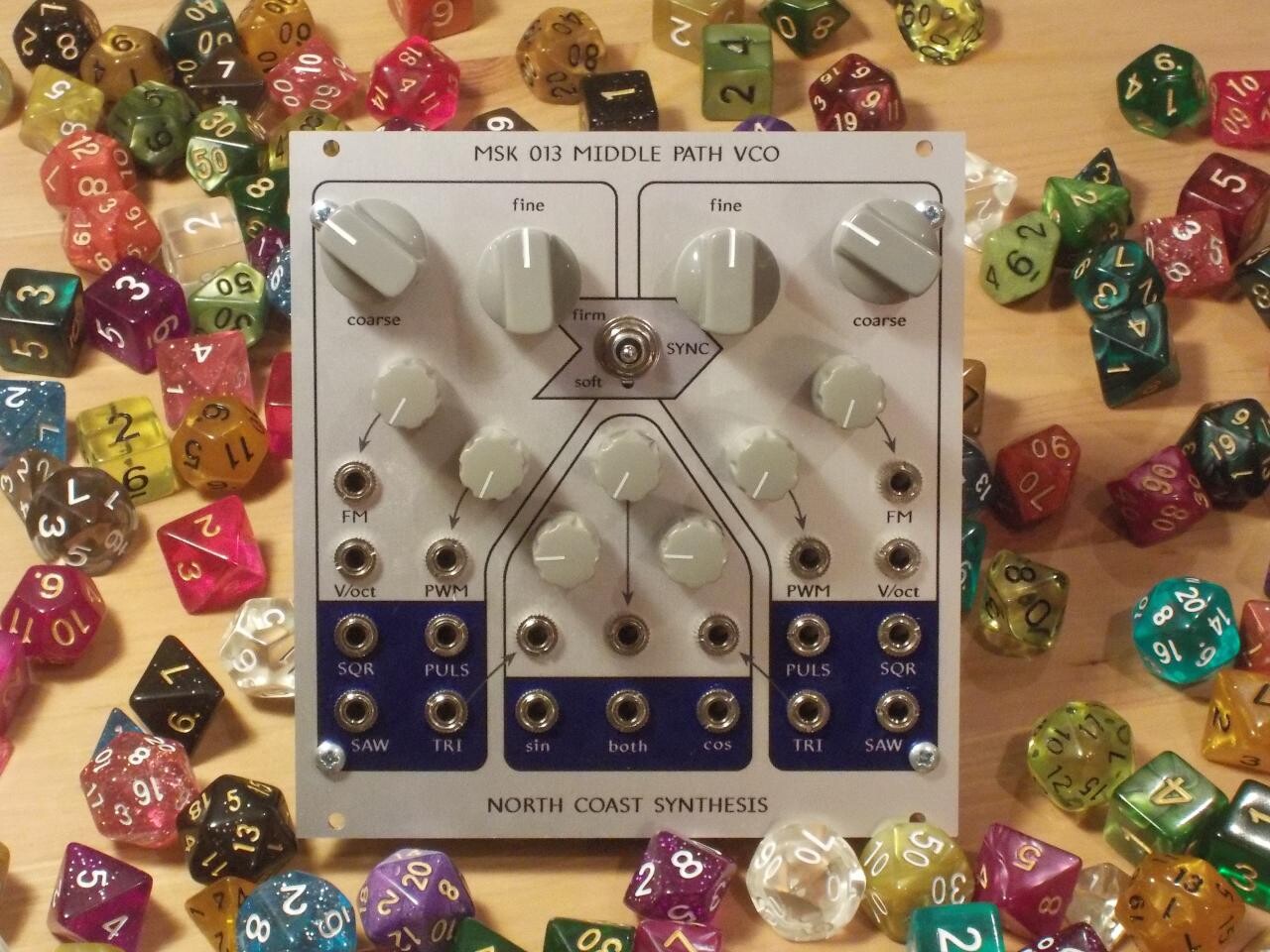
MSK 013 Middle Path VCO
US$486.59 including shipping
Comments
Anyway, I'm a spend thrift as well, so I totally get you trying not to spend extra money when it's not necessary! Heck, I basically have no other choice but to be as frugal as possible. I tried making flux years ago using pine resin and alcohol..I collected the resin from a tree in my yard. I took a small tin can and put a couple layers of aluminum foil inside it then took another double layered piece of foil over the top and made a shallow bowl shape over the top of the can and poked holes in it. Then I put the resin in the top and lit it on fire. That melted the resin causing it to drip thru the holes into the bottom of the can. After that was cool I pulled the foil out of the can, transferred the resin to another tiny container and added alcohol. It took forever to get them mixed but it did eventually mix. Unfortunately the entire container ended up getting knocked off the table and the lid came off, wasting every bit of it before I had the chance to try it out. Anyway, I've been thinking of trying to make a flux again because the kind I've got sucks at wicking solder (store bought kind) & I've got projects I'd like to pull out and finally finish.
So I have a question...Do you think it's better to just melt the resin over heat before adding alcohol or does lighting it on fire produce the same results? I've also seen where people just added the resin to alcohol without melting or burning it first. I was under the impression that the flammable chemicals within the resin needed to be removed with heat before making flux but I don't know. Are you aware of which method is best? Thanks!
The idea of heating pine resin to drive off the more volatile components is interesting. I guess that's just what was going on with the old-time turpentine stills (discussed in an earlier article of this series). Raw pine sap contains both volatile components (turpentine as such, easily evaporated) and non-volatile (rosin) components. In that time and place it was the volatile turpentine that was considered more valuable, so they would heat the mixture, distill off the turpentine, and then they'd be left with the rosin byproduct which could also be sold but was less valuable. It makes some sense that if you want just the rosin, you might go through some process to remove the turpentine.
However, if collecting dry or semi-dry sap crusted on the outsides of trees instead of cutting them to get fresh liquid sap, then I think the turpentine will have already naturally evaporated anyway. And I think setting the resin on fire, necessarily heating it much hotter than would happen during soldering, is probably going to degrade the desired rosin components. So if I were attempting this I would try to do it at as low a temperature as possible *without* setting the product on fire. Oxidizing and overheating the abietic acid (which is the main flux-relevant thing in pine rosin) is likely to reduce its usefulness as a flux. I'd also seriously consider a solvent extraction: dissolve in alcohol, then heat gently to drive the alcohol off and with it anything that boils lower than alcohol. Boiling off a liquid has the effect of limiting the temperature.
This whole process bears an uncomfortable resemblance to some of the ways people process cannabis resin, and it has the same hazards and may be likely to attract the wrong kind of attention if you do anything that looks too much like that. I certainly wouldn't recommend trying to use butane as a solvent! But it's understandable that there'd be a similarity because the physical considerations are roughly the same: it's a matter of separating a mixture of components with different solubilities and boiling points, while ideally not heating it too much.
I made up rosin/91% IPA liquid flux, found it works amazingly well with 2-sided tinned proto board (just 0.1" grid) and crap SnPb solder.
Maybe that means isopropyl alcohol would be useful as an active ingredient, not only an inert solvent, in a soldering flux for aluminum. But it'd evaporate very quickly during soldering so I'm not sure how useful it really would be. Citric acid surely seems like it'd react effectively with the aluminum surface but there's the question of getting it *to* the aluminum surface, under the oxide.
When people deliberately prepare aluminum isopropoxide in the lab (NileRed has a good YouTube video about this) they usually use a mercury compound to get past the oxide layer. But you definitely don't want to be messing with soluble mercury in a soldering process, and you don't want to be exposing aluminum to mercury if it's an aluminum object you want to keep. (NileRed has a couple good videos about *that*, too!)
Also when tests are complete store them in an inaccessible area but exposed to air and review corrosion after 6-12 months. I'm only up to 'testing-homemade-fluxes' so not sure if you done much stuff with gel fluxes but there is a few expired patents on it.
Great work! Probably needs to be on odysee (LBRY) or youtube.